Sand Casting Metal Process A Comprehensive Overview
Sand casting, also known as sand mold casting, is one of the oldest and most versatile metal casting processes used in various industries. This method involves creating a mold from sand, which is then filled with molten metal to produce a desired shape. Due to its flexibility, cost-effectiveness, and ability to produce complex geometries, sand casting remains a preferred choice for many engineering applications.
History and Evolution of Sand Casting
The origins of sand casting date back thousands of years, with evidence of its use in ancient civilizations such as the Egyptians and Chinese. Initially, artisans would carve models from wood or other materials and pack sand around them to create molds. Over time, with technological advancements, the process has evolved to incorporate more sophisticated techniques, including the use of resin-bonded sand and automated machinery, which have significantly enhanced the precision and efficiency of the casting process.
Basic Principles of Sand Casting
The sand casting process comprises several key steps
1. Pattern Making A pattern, typically made from wood or metal, is created in the exact shape of the final product. Patterns can either be a single solid piece or consist of multiple parts, depending on the design.
2. Mold Preparation The pattern is then placed in a flask, a container that holds the sand used to form the mold. The sand is mixed with a binder (often clay or resin) and is packed tightly around the pattern to create a mold cavity.
4. Metal Pouring Once the molds are prepared, molten metal is poured into the mold cavity. The metal solidifies as it cools down, taking on the shape of the mold.
sand casting metal process
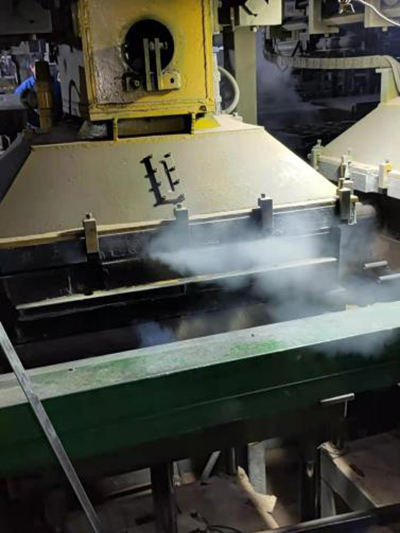
5. Cooling and Shakeout After a short period, the mold is opened (known as shakeout), and the solidified casting is removed. The properties of the mold can affect the cooling rate, which in turn impacts the mechanical properties of the finished casting.
6. Finishing The final step involves cleaning the casting, which may include removing excess sand, trimming additional material, and performing any surface finishing processes required to achieve the desired surface quality.
Advantages of Sand Casting
One of the most significant advantages of sand casting is its adaptability to various sizes and quantities of parts. It can effectively produce both small and large components, making it suitable for everything from intricate jewelry to massive industrial parts. Additionally, the use of sand as a mold material allows for easy modification of the mold for different designs, which is especially beneficial for prototyping and low-volume production.
Another advantage is the low cost of the raw materials involved. Sand is abundantly available and inexpensive, while the casting process itself does not require highly specialized equipment, making it accessible for many foundries. Furthermore, sand casting can accommodate a wide range of metals, including ferrous and non-ferrous alloys, which enhances its versatility.
Challenges and Limitations
Despite its many benefits, sand casting does have some challenges. The surface finish of sand-cast parts tends to be rougher compared to other processes like investment casting. Additionally, the dimensional accuracy can vary, necessitating additional machining for tight tolerances. The process can also be slow, particularly for complex molds or when producing parts in large runs.
Conclusion
In conclusion, sand casting is a time-honored and versatile metal casting process that continues to find relevance in modern manufacturing. Its ability to produce complex shapes at a low cost, combined with its adaptability to various metals, makes it an ideal choice for many industries. While it does come with some challenges, ongoing advancements in materials and techniques are likely to enhance the capabilities of sand casting, ensuring its place in the future of metalworking. Understanding the intricacies of this process is crucial for engineers and manufacturers seeking to maximize the potential of their designs and maintain a competitive edge in the marketplace.
Post time:Sult . 30, 2024 05:28
Next:Verwendung von harzbeschichtetem Sand in der Industrie und Bauanwendungen