Understanding Sand Casting in Metalworking
Sand casting is one of the oldest and most widely used metalworking processes, where metal is poured into a sand mold to create intricate shapes and parts. This technique is fundamental in manufacturing and has applications in various industries, including automotive, aerospace, and art. In this article, we will explore the fundamentals of sand casting, the materials used, the process involved, and its advantages and disadvantages.
The Basics of Sand Casting
At its core, sand casting involves creating a mold from a mixture of sand and a binding agent—usually clay or resin—which is then used to shape molten metal. The process begins with the design of a pattern, which serves as a replica of the final product. Patterns can be made from a variety of materials, including wood, metal, or plastic. Once the pattern is designed, it is placed in a sand mixture to create the mold.
The sand used in this process is typically silica sand, which is preferred for its high melting point and durability. The sand is often mixed with a binder to improve its cohesiveness and with other additives to achieve specific properties, such as improved surface finish or reduced moisture absorption.
The Sand Casting Process
The sand casting process can be broken down into several key steps
1. Pattern Creation The first step is to create a pattern that reflects the shape of the desired final product. This pattern is usually slightly oversized to account for shrinkage during the cooling of the metal.
2. Mold Preparation Next, the pattern is pressed into the sand mixture to form the mold. The sand is compacted around the pattern to ensure that it holds its shape and can withstand the high temperatures of the molten metal.
3. Core Creation (if necessary) For complex shapes with internal cavities, cores made from sand or metal may be placed in the mold. Cores are used to create hollow sections within the castings.
4. Pouring the Metal Once the mold is prepared, it is heated to eliminate any moisture. Molten metal, typically aluminum, bronze, or iron, is then poured into the mold. The temperature and composition of the molten metal are crucial for achieving the desired properties in the final product.
5. Cooling and Removal After the metal has filled the mold, it is allowed to cool and solidify. Once cooled, the sand mold is broken away to reveal the cast metal part.
6. Finishing The final step involves cleaning and finishing the casting. This may include grinding, sanding, or shot blasting to achieve the desired surface finish and dimensional accuracy.
sand casting metal
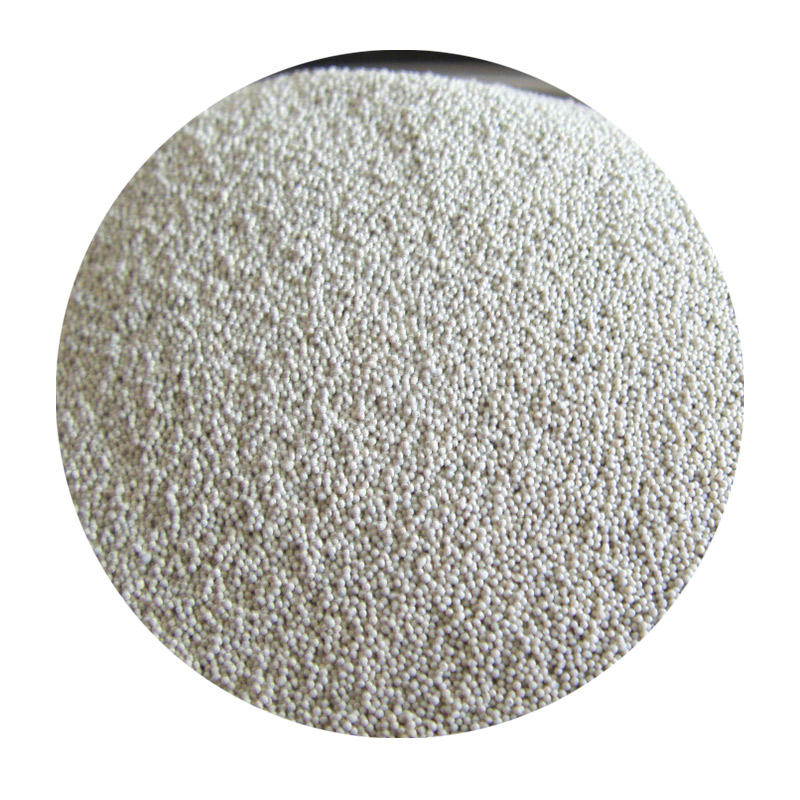
Advantages of Sand Casting
Sand casting offers several advantages, making it a favored method in the metalworking industry
- Versatility Sand casting can accommodate complex shapes and large components, making it suitable for various applications
.- Cost-Effectiveness The materials used in sand casting are relatively inexpensive, and the process is economical for both low and high-volume production.
- Ease of Setup Creating molds from sand requires minimal equipment compared to other casting methods, allowing for quick setup and turnaround times.
Disadvantages of Sand Casting
Despite its many benefits, sand casting does have some disadvantages
- Surface Finish The finish of cast parts may not be as smooth as those produced by other methods such as investment casting or die casting.
- Dimensional Accuracy Parts produced through sand casting may not meet tight tolerances, which could be necessary for some applications.
- Labor-Intensive The process can be labor-intensive, especially in small-scale operations, which may increase production time.
Conclusion
In conclusion, sand casting remains a vital technique in metalworking, prized for its adaptability and affordability. While it may not always provide the level of precision or surface finish required for every application, its capability to produce complex shapes makes it indispensable across many industries. As advancements in technology continue to evolve the metalworking landscape, sand casting will likely remain a cornerstone of manufacturing, fostering innovation and creativity in metal parts production.
Post time:Samh . 30, 2024 07:55
Next:Incorporating Foundry Sand into Concrete Mixes for Enhanced Performance and Sustainability