Sand Casting Iron An Overview of a Timeless Metalworking Technique
Sand casting, a Foundry practice dating back thousands of years, still holds significance in modern manufacturing. Among the various metals used in this process, cast iron stands out due to its versatility, strength, and casting properties. This article delves into the essentials of sand casting iron, its benefits, applications, and the processes involved.
What is Sand Casting?
Sand casting is a metal casting process characterized by using sand as the mold material. This method involves creating a mold from a mixture of sand and a binder, pouring molten metal into the mold cavity, allowing it to cool and solidify, and finally removing the casting from the mold. The process is popular for its ability to produce complex shapes and its relatively low cost compared to other casting techniques.
Properties of Cast Iron
Cast iron is a group of iron-carbon alloys with a carbon content greater than 2%. It is known for its excellent fluidity, castability, and machinability. Cast iron can endure significant wear and maintains dimensional stability, which makes it an ideal choice for sand casting. Different types of cast iron, including gray iron, ductile iron, and white iron, have unique properties that cater to various industrial applications.
1. Gray Iron This type of cast iron features a high carbon content and exhibits excellent machinability and wear resistance. Its grey color comes from the presence of graphite flakes in its structure. Gray iron is commonly used for engine blocks, machine bases, and pipes.
2. Ductile Iron Also known as spheroidal graphite iron or nodular cast iron, ductile iron offers enhanced strength and ductility compared to gray iron. The inclusion of small spherical graphite nodules in its structure allows it to withstand higher tensile stresses. Ductile iron is widely used in manufacturing automotive components, gears, and pressure pipes.
3. White Iron White iron has a higher carbon content, resulting in a white surface when fractured. It is extremely hard and brittle, making it suitable for wear-resistant applications, such as dies, liners, and some tools.
The Sand Casting Process
The sand casting process encompasses several stages
1. Mold Creation The first step involves designing and constructing the mold. Sand mixed with a bonding agent is packed around a pattern of the object to be cast. Once the sand hardens, the pattern is removed, leaving a cavity for the molten iron.
sand casting iron
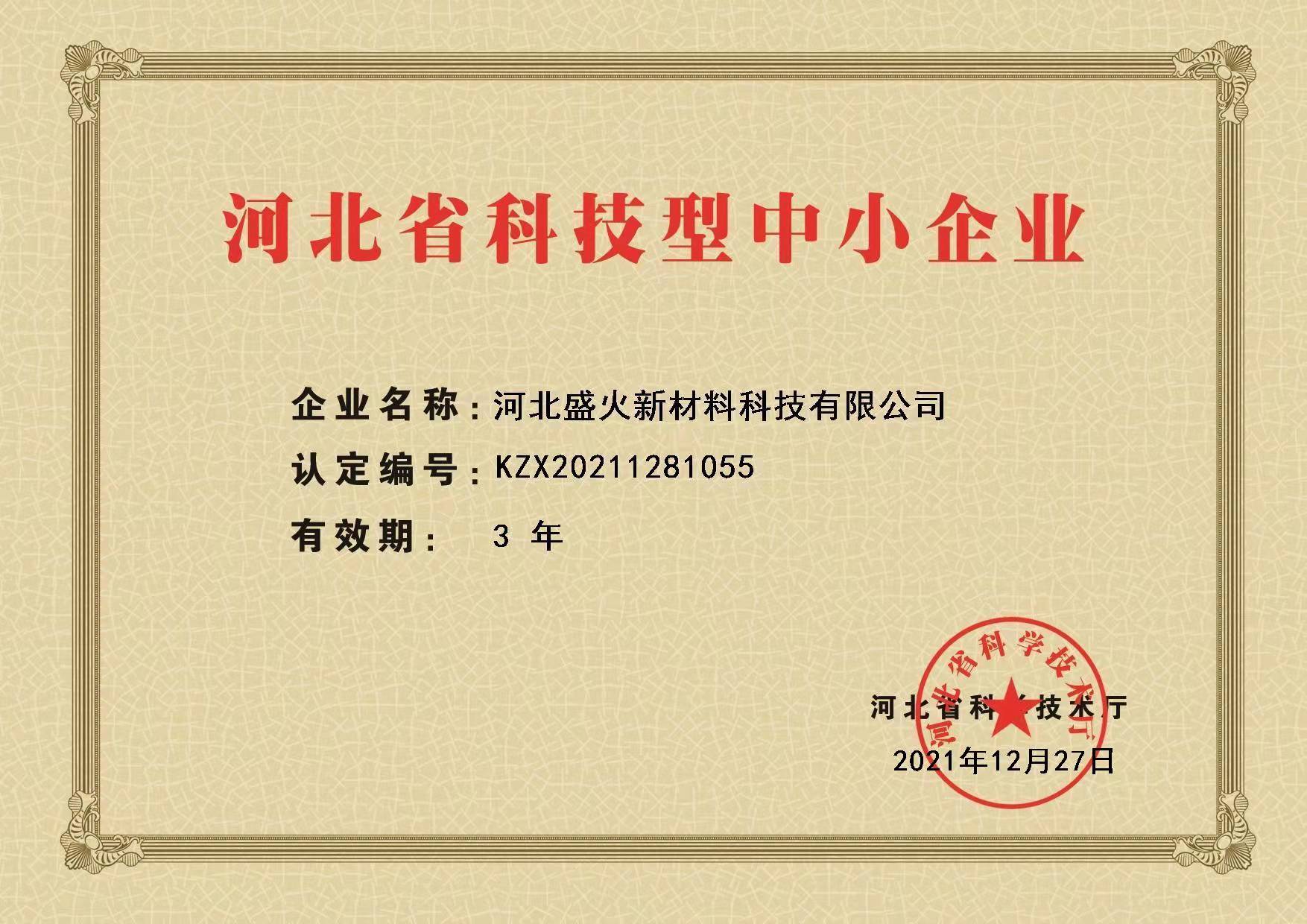
2. Melting and Pouring The next step is melting the cast iron in a furnace. The molten metal is poured into the prepared sand mold, filling the cavity and taking the shape of the desired object.
3. Cooling and Solidification After pouring, the metal is allowed to cool and solidify within the mold. This stage may take several hours, depending on the thickness and size of the casting.
4. Finishing Once cooled, the sand mold is broken away to reveal the casting. Any excess material, such as sprues or runners, is trimmed, and surface finishing processes may be employed to achieve the required specifications.
Advantages of Sand Casting Iron
The sand casting process offers numerous advantages, particularly when applied to cast iron
- Cost-Effectiveness The materials and equipment required for sand casting are relatively inexpensive, making it a cost-effective option for producing large quantities of products. - Design Flexibility Sand casting allows for the creation of complex shapes and geometries that may be challenging with other manufacturing methods.
- Durability Cast iron components exhibit exceptional wear resistance, making them suitable for heavy-duty applications.
- Heat Resistance Cast iron maintains its mechanical properties at high temperatures, making it ideal for components subjected to thermal stress, such as engine parts.
Applications
Sand casting iron is utilized in a wide range of industries, including automotive, construction, aerospace, and heavy machinery. Common applications include engine blocks, machinery bases, pipes, and decorative elements in architecture.
Conclusion
Sand casting iron continues to be a vital part of the manufacturing landscape. Its unique properties, combined with the advantages of the sand casting process, make it an enduring choice for producing effective and durable components across various applications. As manufacturers look for cost-effective and reliable methods to create complex shapes, sand casting iron will likely remain a staple in metalworking for years to come.
Post time:Samh . 05, 2024 23:05
Next:applications of sand casting