Sand Casting Components A Comprehensive Overview
Sand casting, also known as sand mold casting, is one of the oldest and simplest methods of metal casting. This versatile technique is characterized by its ability to produce complex shapes and a wide range of metal components. The process utilizes sand as the primary molding material, allowing for efficient production of metal parts in various industries, including automotive, aerospace, and machinery. In this article, we will explore the key components of sand casting and their significance in the overall casting process.
Molding Sand
The cornerstone of sand casting is the molding sand, which is a mixture of sand, clay, and water. The properties of sand, such as grain size, shape, and moisture content, play a critical role in determining the quality of the final casting. The sand must be fine enough to capture the details of the mold but coarse enough to facilitate the easy flow of molten metal. The most commonly used sand is silica sand, owing to its excellent thermal properties and availability.
Pattern
A pattern is a replica of the object to be cast, made from materials like wood, metal, or plastic. It serves as the template for creating the mold. Patterns are typically slightly larger than the final product to account for material shrinkage during cooling. There are various types of patterns, including solid, split, and shell patterns, each designed to serve specific casting requirements. Accurate pattern design is essential for achieving the desired tolerances and surface finishes in the final component.
Core
Cores are used to create internal cavities or complex shapes within cast components that cannot be achieved with the outer mold alone. They are typically made from sand mixed with a binding agent to provide strength. Cores are positioned within the mold before the molten metal is poured in. Once the metal solidifies and is removed from the mold, the core can be broken out to reveal the desired internal features. The use of cores allows designers greater flexibility in component design.
sand casting components
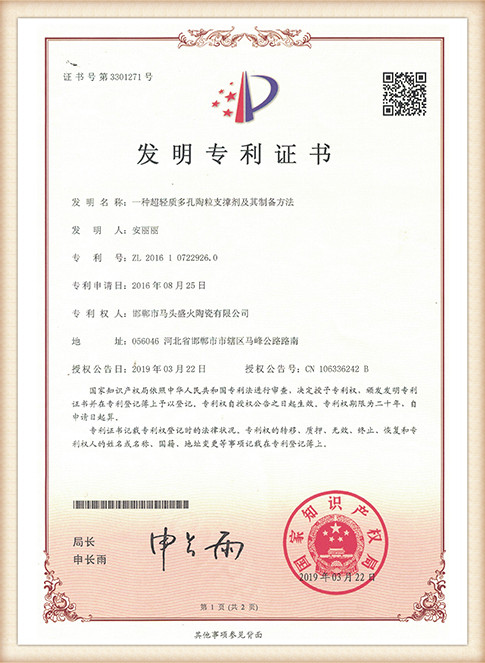
Mold
The mold is formed by packing molding sand around the pattern. Once the pattern is removed, the remaining cavity represents the shape of the casting. Molds can be classified as closed molds or open molds, depending on the design and requirements of the casting. Molds need to withstand the pressure of molten metal and resist deformation during the pouring process. Proper venting is also crucial as it allows gases to escape and prevents defects in the final product.
Pouring System
The pouring system comprises the channels through which molten metal is conveyed into the mold cavity. This system includes the pouring basin, sprue, runners, and gates. Design considerations for the pouring system are vital as they influence the flow rate, fill time, and thermal characteristics during casting. A well-designed pouring system minimizes turbulence and ensures even distribution of metal, reducing the risk of defects such as cold shuts or misruns.
Finishing Process
After solidification, the casting is removed from the mold, and the finishing process begins. This stage may include cleaning, trimming, machining, and surface treatment to achieve the required specifications. Finishing is essential for enhancing the mechanical properties and aesthetic appearance of the final component. Techniques such as shot blasting, grinding, and polishing are commonly employed to refine the surface finish.
Conclusion
Sand casting remains a popular method for manufacturing metal components due to its flexibility, low cost, and ability to yield complex geometries. Understanding the various components involved in the sand casting process is critical for optimizing production and achieving high-quality results. From molding sand to the finishing process, each element plays a vital role in determining the integrity and performance of the final product. As industries continue to evolve, advancements in technology will likely enhance sand casting methods, making them even more efficient and reliable for future applications.
Post time:Samh . 27, 2024 06:00
Next:High-Performance Ceramic Sanding Discs for Superior Surface Finish and Durability