Advantages of Sand Casting
Sand casting, one of the oldest and most widely used metal casting processes, has proven to be an invaluable method in modern manufacturing. This technique involves creating a mold from a mixture of sand and a binding agent, in which molten metal is poured to create a desired shape. Its enduring presence in various industries, from automotive to aerospace, can be attributed to several compelling advantages.
1. Cost-Effectiveness
One of the most significant benefits of sand casting is its cost-effectiveness. The primary materials used, sand and a binding agent, are relatively inexpensive compared to other materials required for casting processes like investment casting. Additionally, the sand can often be reused multiple times, further driving down costs. This affordability makes sand casting an attractive option for both small and large-scale manufacturing operations.
2. Versatility in Size and Complexity
Sand casting is remarkably versatile in terms of the size and complexity of the parts it can produce. Unlike other casting processes that may be limited to smaller components, sand casting can accommodate large and complex geometries. From intricate designs for machinery parts to large components in industrial applications, the process allows for significant freedom in design without requiring extensive tooling alterations. This flexibility is particularly useful for industries that demand bespoke solutions.
3. Excellent Surface Finish and Detail
While sand casting may not initially appear to compete with more refined casting methods, advancements in techniques and materials have improved its ability to achieve good surface finishes and detailed designs. High-quality sands mixed with appropriate binding agents can produce molds that capture fine details and provide smoother surfaces than earlier methods. With post-processing techniques such as grinding and polishing, sand-cast components can meet high aesthetic and functional standards.
4. Capacity for Producing Large Quantities
sand casting advantages
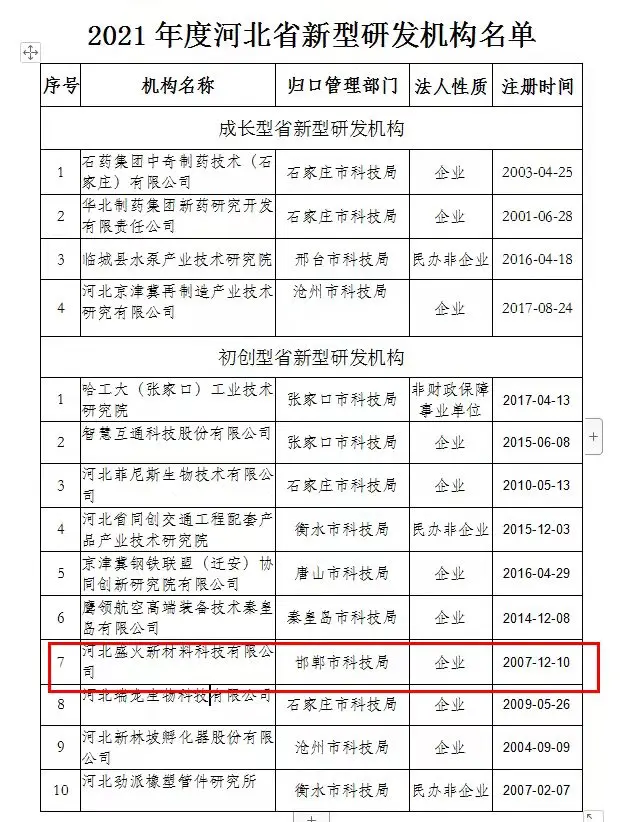
Sand casting excels in batch production, making it a preferable choice for companies needing large quantities of identical parts. Unlike other casting processes that may require significant time and investment to create individual molds, sand molds can be produced quickly and efficiently. This capability is especially useful in industries like automotive, where thousands of parts must be produced in a timely manner without sacrificing quality.
5. Environmental Considerations
As sustainability becomes increasingly important in manufacturing, sand casting offers a more environmentally friendly option than many alternatives. The materials used are predominantly natural and can be recycled. Waste sand from the casting process can often be reclaimed and reused, minimizing the environmental footprint. Additionally, advancements in green sand technology have led to the development of eco-friendly sand binders that reduce harmful emissions during production, making sand casting a choice for forward-thinking companies.
6. Compatibility with Various Metals
Sand casting is compatible with a broad range of metals and alloys, including iron, aluminum, bronze, and magnesium. This adaptability allows manufacturers to select specific materials based on the requirements of the end product, such as strength, weight, and thermal properties. The ability to cast various materials enables designers to innovate and choose the most appropriate metal for any project, enhancing the performance and durability of the final product.
7. Economic Scalability
The scalability of sand casting is another notable advantage. Manufacturers can start with smaller production runs and gradually increase output without the need for substantial changes to the existing setup. This economic scalability is ideal for companies looking to enter new markets or experiment with different designs without a significant upfront investment. It allows for testing and prototyping of new products without the commitment to full-scale production from the outset.
Conclusion
In summary, sand casting remains a vital method in the manufacturing landscape due to its numerous advantages. Its cost-effectiveness, versatility in size and complexity, ability to produce large quantities, and compatibility with various metals make it a go-to choice for many industries. Furthermore, its environmental benefits and economic scalability align it closely with contemporary manufacturing goals focused on sustainability and efficiency. As technology continues to advance, the role of sand casting is likely to evolve, but its importance in the production of high-quality components will undoubtedly endure.
Post time:Dùbh . 07, 2024 16:50
Next:3d sand printing casting