Precision Sand Casting An Overview
Precision sand casting is a widely used manufacturing process that allows for the creation of intricate metal components with high dimensional accuracy and surface quality. This method holds significant importance in various industries, including automotive, aerospace, and industrial machinery. The precision sand casting process not only offers versatility in design but also enables cost-effective production for both small and large-scale operations.
The Sand Casting Process
At its core, sand casting involves the creation of a mold from a mixture of sand and binders, into which molten metal is poured to form solid components. The primary steps of the process are as follows
1. Pattern Creation The first step is the creation of a pattern, which is usually made of metal, plastic, or wood. This pattern represents the final shape of the metal component and is crucial for ensuring dimensional accuracy. For precision sand casting, patterns are often designed with slight allowances for material shrinkage that occurs during cooling.
2. Mold Preparation Once the pattern is ready, it is used to form a mold in a mixture of sand and a binder. There are various types of sand used in casting, such as silica sand and zircon sand, each chosen based on specific application requirements. The mold is formed by packing the sand tightly around the pattern, ensuring it captures all the fine details.
3. Core Placement If the metal component requires hollow spaces or specific internal features, cores made from sand or other materials are added to the mold. These cores are crucial for achieving complex geometries that cannot be formed with just the outer mold.
4. Metal Pouring and Cooling The mold is then pre-heated, and molten metal, typically aluminum, iron, or steel, is poured into it. The choice of metal depends on the mechanical properties required for the final product. Once the metal is poured, it is left to cool and solidify, which can take several hours, depending on the size and thickness of the casting.
5. Mold Removal and Finishing After the metal has cooled, the sand mold is broken apart to reveal the casting. The casting may require several finishing processes, including grinding, machining, and surface treatment, to achieve the desired surface finish and dimensional accuracy.
precision sand casting
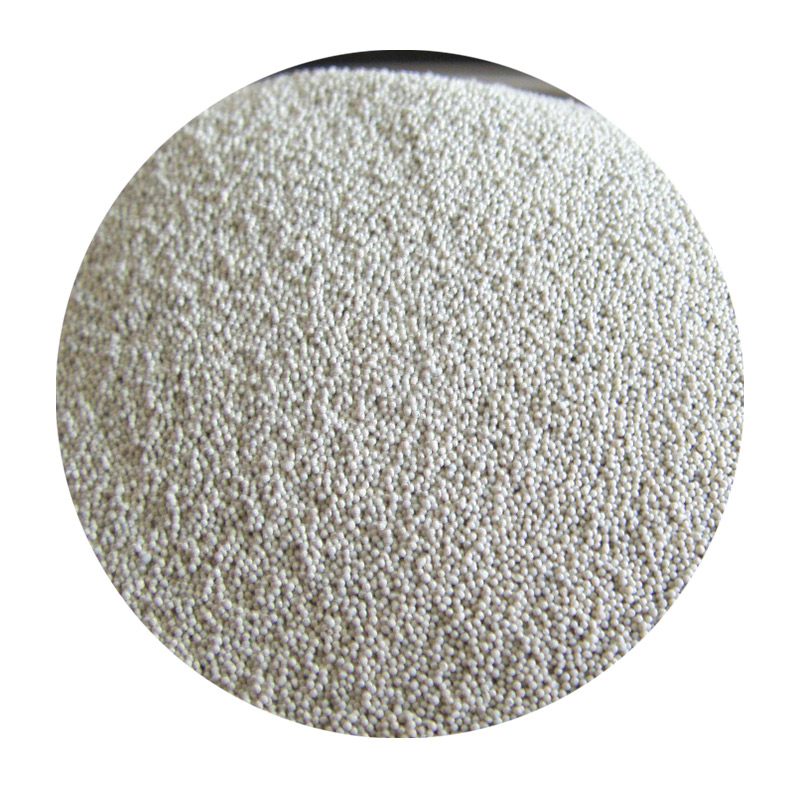
Advantages of Precision Sand Casting
One of the primary advantages of precision sand casting is its ability to produce complex shapes and intricate designs that are often difficult to achieve through other manufacturing processes
. The use of sand as a molding material allows for flexibility in design, enabling manufacturers to create components with various internal features.Moreover, this casting method is economically viable for both low and high volumes of production. The materials involved in sand casting are relatively inexpensive, and the process itself requires less investment compared to other methods such as die casting or investment casting.
Another key benefit of precision sand casting is its compatibility with a wide range of metals. This flexibility allows manufacturers to select the most suitable material for their specific application, whether they need lightweight aluminum components or heavy-duty iron parts.
Challenges and Considerations
While precision sand casting has numerous advantages, it is not without its challenges. One common issue is the potential for defects such as sand inclusion, porosity, and misalignment, which can affect the performance of the final product. To mitigate these risks, manufacturers must invest in quality control measures, including thorough inspection and testing of casts.
Additionally, the need for post-processing can increase the lead time for production, making it crucial for manufacturers to plan their processes carefully. Adopting advanced technologies, such as computer-aided design (CAD) and simulation software, can enhance both the accuracy and efficiency of the casting process.
Conclusion
Precision sand casting remains a vital manufacturing technique due to its versatility, cost-effectiveness, and ability to produce high-quality components. As industries continue to evolve, the demand for precision and innovation in manufacturing will only grow, ensuring that sand casting remains relevant in the modern manufacturing landscape. Manufacturers that harness the full potential of precision sand casting can look forward to creating components that meet the rigorous demands of today's applications.
Post time:Dùbh . 05, 2024 21:14
Next:Affordable Sand Casting Solutions for Your Manufacturing Needs and Budget Constraints