Open Sand Casting An Overview of the Technique
Open sand casting is a traditional and widely used metal casting process that has stood the test of time due to its versatility and cost-effectiveness. This method is especially valuable in manufacturing large parts and components in various industries, including automotive, aerospace, and machinery. In this article, we will explore the fundamentals of open sand casting, its advantages and disadvantages, as well as applications and recent advancements in the technique.
Fundamentals of Open Sand Casting
The open sand casting process involves several stages, starting with the preparation of the sand mold. The primary material used is silica sand, which is mixed with a binding agent, typically clay or resin, to provide the necessary stability and strength. The mixture is then compacted around a pattern, which represents the shape of the desired object. This pattern can be made of various materials, including metal, plastic, or wood.
Once the mold is formed, it is removed from the pattern, and a pouring basin is created for the molten metal. When the mold is ready, molten metal is poured into the cavity created by the pattern, filling it entirely. After allowing the metal to cool and solidify, the mold is broken apart, revealing the cast object. The final step is cleaning, where any excess sand is removed, and finishing processes, such as machining or surface treatment, may be applied to achieve the desired specifications.
Advantages of Open Sand Casting
Open sand casting presents several advantages that make it a preferred choice for many manufacturers. Firstly, the process is remarkably flexible and allows for the creation of complex shapes and intricate designs that might be challenging with other casting methods. This flexibility enables engineers and designers to innovate and produce parts that meet specific performance requirements.
Secondly, open sand casting is relatively low-cost compared to other casting techniques, such as die casting or investment casting. The materials used, primarily sand and a binding agent, are inexpensive and readily available. Additionally, the technique is suitable for small to large production runs, making it economically viable for both prototypes and mass-produced components.
Moreover, the process can handle a wide range of metals, including aluminum, iron, bronze, and various alloys. This adaptability allows manufacturers to select materials based on the performance characteristics required for each specific application.
Disadvantages of Open Sand Casting
open sand casting
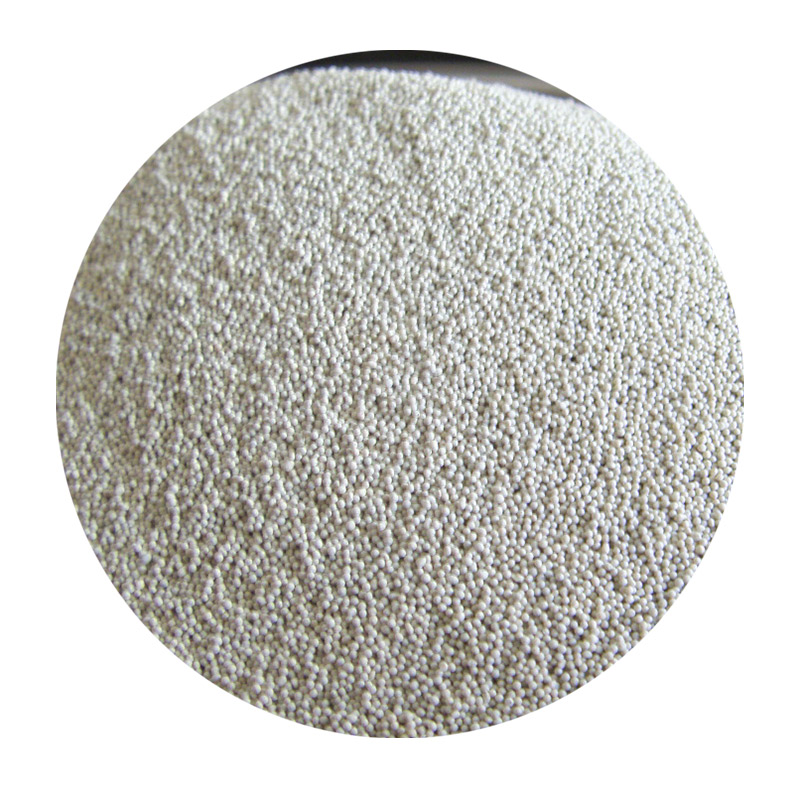
Despite its numerous benefits, open sand casting is not without drawbacks. One significant limitation is the relatively lower precision and surface finish compared to other casting methods. The sand mold can leave an imprint on the metal surface, resulting in more post-processing work to achieve the desired finish.
Furthermore, the process can introduce defects such as porosity, shrinkage, and gas inclusions, which may compromise the integrity of the final product. Manufacturers must take extra care during the design phase and implement rigorous quality control measures to mitigate these issues.
Applications of Open Sand Casting
Open sand casting is employed across a variety of sectors, particularly where large and robust components are necessary. In the automotive industry, for instance, it is used to produce engine blocks, transmission cases, and various structural components. Similarly, the aerospace sector benefits from the technique in manufacturing heavy-duty parts that withstand extreme conditions and stress.
Another application is in the creation of industrial machinery and equipment, where custom parts must be produced to fit specific operational requirements. Additionally, open sand casting is frequently used in the art and sculpture domain, allowing artists to create large metallic sculptures and designs.
Recent Advancements
In recent years, the open sand casting process has seen advancements driven by technology and innovation. The integration of computer-aided design (CAD) software and simulation tools has improved design accuracy and efficiency, allowing for better predictions of how the metal will behave during the casting process. These advancements have resulted in reducing the occurrence of defects and enhancing the overall quality of cast products.
Moreover, the rise of green sand casting—utilizing recycled materials and sustainable practices—reflects a growing emphasis on environmental responsibility in the manufacturing industry. This shift not only reduces waste but also lowers production costs.
Conclusion
Open sand casting remains a vital process in the metalworking industry, providing significant benefits in terms of flexibility, cost-effectiveness, and material versatility. While it comes with its own set of challenges, ongoing advancements and innovations continue to enhance the process and address its limitations. As industries evolve and seek efficient manufacturing solutions, open sand casting will undoubtedly continue to play a crucial role in various applications.
Post time:Samh . 06, 2024 02:38
Next:A Beginner's Guide to Creating Sand Castings for Metal Projects