Lost Foam Casting Coating A Comprehensive Overview
Lost foam casting is an advanced metal casting process that offers unique advantages over traditional methods. This technique involves creating a foam pattern that is coated with a ceramic material to withstand molten metal. The coating plays a crucial role in the success of lost foam casting, influencing the quality of the final product, the efficiency of the process, and the overall cost. In this article, we will explore the importance of lost foam casting coating, its composition, application methods, and potential challenges, highlighting its significance in modern manufacturing.
Importance of Coating in Lost Foam Casting
The primary function of the coating in lost foam casting is to create a shell that can withstand high temperatures when molten metal is poured into the mold. This shell not only protects the foam pattern but also defines the surface finish and dimensional accuracy of the final product. A well-applied coating ensures that the foam pattern evaporates at the appropriate rate, allowing for a smooth flow of molten metal while minimizing defects such as defects like inclusions, porosity, or surface irregularities.
Additionally, the coating contributes to the overall mechanical strength of the mold, allowing it to support the weight of the molten metal. This is especially important in large castings where the pressure exerted on the mold can be significant. Therefore, the right coating is essential for achieving high-quality castings with excellent mechanical properties.
Composition of Lost Foam Casting Coatings
Lost foam casting coatings typically consist of a mixture of fine refractory materials, such as silica, zirconia, or alumina, suspended in a liquid binder. The binder helps the refractory materials adhere to the foam pattern and forms a strong, thermally stable shell once cured. The choice of materials in the coating can vary depending on the specific requirements of the casting process and the type of metal being poured.
For example, when casting aluminum or magnesium alloys, the coating needs to be resistant to thermal shock and must not chemically react with the molten metal. Some formulations include additives to enhance properties such as strength, thermal conductivity, and resistance to erosion or metal penetration. As technology advances, more innovative and efficient coatings are being developed, allowing for better performance and reduced production costs.
Application Methods of Coatings
The application of coatings in lost foam casting can be achieved through several methods, each with its pros and cons
. The most common methods includelost foam casting coating
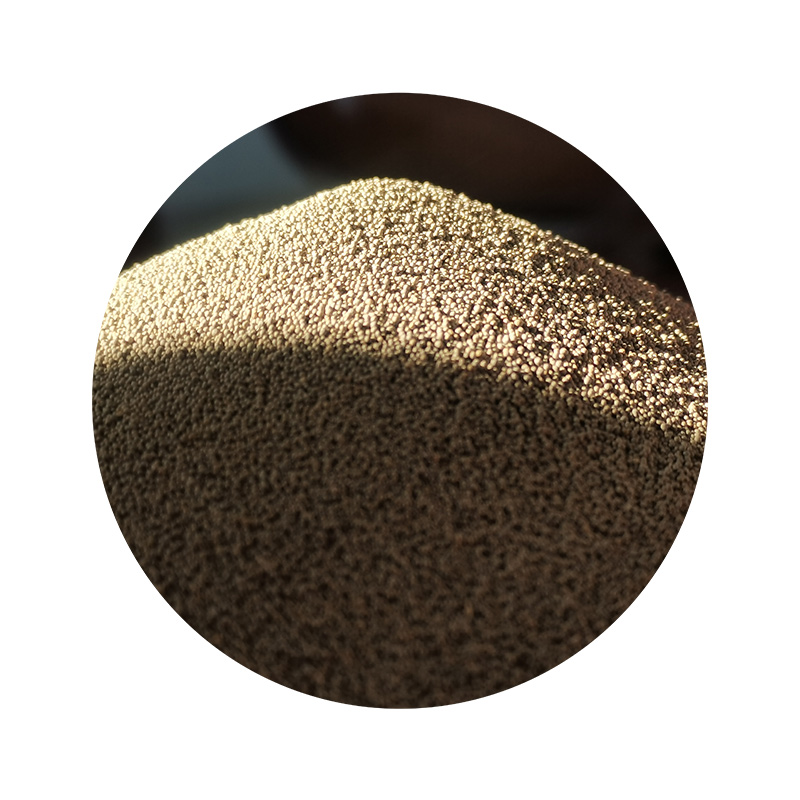
1. Dipping The foam pattern is immersed in a slurry of the coating material. This method provides even coverage and is effective for intricate patterns, but may lead to excessive coating thickness if not properly controlled.
2. Spraying High-pressure spray application allows for a lightweight coat on the foam pattern. This method is suitable for large or complex patterns and helps reduce the amount of material used but may require specialized equipment.
3. Brushing Manual brushing can be used for small quantities or intricate patterns, allowing for precise application. However, this method can be labor-intensive and may result in inconsistencies.
4. Electrostatic Application This technique uses an electric charge to attract coating particles to the foam pattern, allowing for a uniform coat with minimal overspray.
Each method of application may impact the properties of the final casting, which is why careful consideration must be given to selecting the appropriate technique based on production requirements and costs.
Challenges and Considerations
Despite its advantages, lost foam casting with coating presents certain challenges. Achieving the right coating thickness, curing time, and adhesion properties is crucial for ensuring optimal performance. Insufficient coatings may lead to defects, while overly thick coatings can create issues, such as increased weight and longer melting periods.
Furthermore, careful handling of the foam pattern after coating is necessary to prevent damage before the casting process. Continuous research and development are needed to address these challenges, especially as industries drive towards higher precision and lower production costs.
Conclusion
In summary, lost foam casting coating is an integral aspect of the lost foam casting process, crucial in determining the quality and performance of the final product. By understanding the importance of the coating, its composition, application methods, and potential challenges, manufacturers can optimize their casting processes, leading to superior products and increased competitiveness in the market. As the technology evolves, innovations in coating materials and techniques will further enhance the capabilities of lost foam casting, making it a preferred choice in various industries, from automotive to aerospace and beyond.
Post time:Dùbh . 12, 2024 21:24
Next:sand casting foundry