Lost Foam Casting An Innovative Approach in Metal Casting
Lost foam casting (LFC) is a sophisticated metal casting process that has gained prominence in various industries due to its precision and cost-effectiveness. This method involves the use of a foam pattern, typically made from polystyrene, which is coated with a ceramic shell and subsequently filled with molten metal. The foam pattern evaporates upon contact with the molten metal, leaving a cavity that takes on the shape of the desired part. This article explores the intricacies of the lost foam casting process, its advantages, applications, and future prospects.
The Lost Foam Casting Process
The lost foam casting process begins with the creation of a foam pattern that reflects the shape of the final product. This pattern is made from a lightweight material like expanded polystyrene (EPS). The foam pattern is then coated with a mixture of fine sand and a binding agent, forming a durable shell that can withstand high temperatures. Once the coating hardens, the foam is melted away by introducing it to the molten metal, resulting in a void that solidifies into the final product.
Unlike traditional sand casting, where patterns are permanently removed, the lost foam method eliminates the need for pattern removal, thereby simplifying the process and improving accuracy. The molten metal flows into the space where the foam once was, ensuring a high level of detail and dimensional accuracy in the cast parts.
Advantages of Lost Foam Casting
1. Precision and Detail One of the most significant advantages of lost foam casting is its ability to produce complex shapes and intricate designs with minimal machining. The precision achieved reduces the need for secondary operations, ultimately saving time and costs.
2. Lower Production Costs The LFC process requires fewer raw materials and produces less waste compared to traditional casting methods. The elimination of molds reduces initial investment costs and enhances overall efficiency.
3. Material Versatility Lost foam casting can accommodate a variety of metals, including aluminum, iron, and bronze. This versatility makes it suitable for producing diverse components across different sectors.
4. Improved Surface Finish The resulting castings have a smoother surface finish than those produced by traditional methods. This quality reduces the need for additional surface finishing processes, further reducing manufacturing time and costs.
lost foam casting
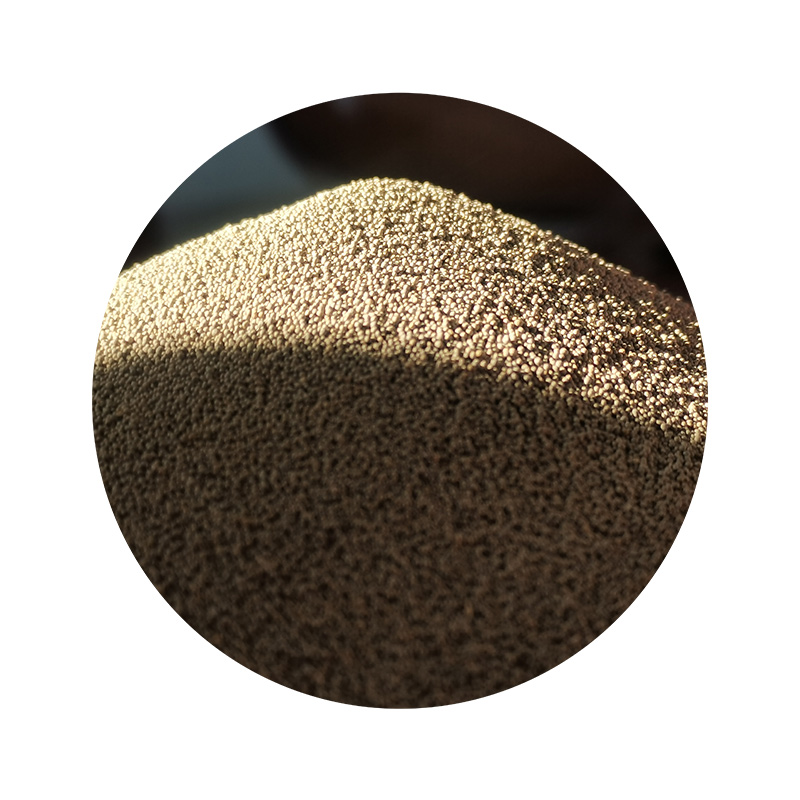
5. Environmental Benefits Since lost foam casting utilizes a foam pattern that is evaporated rather than discarded, the process generates less solid waste. The use of recyclable materials and fewer emissions align with modern sustainability goals in manufacturing.
Applications of Lost Foam Casting
Lost foam casting is widely used in various industries, including automotive, aerospace, and industrial machinery. Its ability to produce lightweight and complex parts makes it particularly appealing for components that demand high performance under stress, such as engine blocks, exhaust manifolds, and turbine housings.
In the aerospace sector, LFC is employed to create intricate components where precision is paramount. These applications benefit from the lower weight of the final products, contributing to fuel efficiency and overall performance.
Future Prospects
As manufacturing techniques continue to evolve, lost foam casting is poised for further advancements. With the integration of automated processes and sophisticated modeling software, the quality and efficiency of LFC can be significantly enhanced. Additionally, as industries increasingly focus on sustainability, the environmentally friendly aspects of lost foam casting may lead to wider adoption.
The ongoing research into materials that can withstand higher temperatures can further expand the range of metals suitable for the LFC process. This exploration could open new avenues in sectors such as renewable energy, where durable components are essential.
Conclusion
Lost foam casting represents a significant advancement in the field of metal casting, offering numerous benefits that cater to the demands of modern manufacturing. With its ability to produce precision components in a cost-effective and environmentally friendly manner, it has established itself as a valuable process across multiple industries. As technological innovations continue to develop, the potential applications and efficiencies of lost foam casting will likely expand, making it an integral part of future manufacturing processes.
Post time:Sult . 23, 2024 14:13
Next:Innovative Techniques in Resin Coated Sand Production for Enhanced Casting Quality