The Iron Sand Casting Process An Overview
The iron sand casting process is a fascinating method used in foundries to create iron components and parts for various applications
. This process leverages the unique properties of iron sand, which is rich in iron oxides, providing a sustainable and cost-effective alternative to traditional casting methods.The process begins with the collection of iron sand, often obtained from natural deposits along riverbanks or coastal areas. The sand is then purified to remove impurities that could affect the quality of the final product. Once purified, the iron sand is mixed with a binding agent to form a mold. This mixture is typically composed of silica sand, clay, and water, which combines to create a durable mold that can withstand high temperatures during the pouring of molten iron.
Next, the mold is prepared in a two-part system, consisting of a cope (the top half) and a drag (the bottom half). The pattern, which is an exact replica of the desired part, is placed in the drag. The binding mixture is compacted around the pattern to create a mold cavity. After compacting, the cope is placed on top, completing the mold.
iron sand casting process
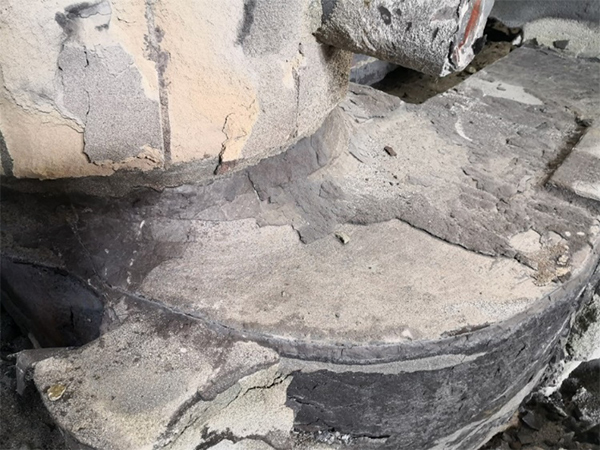
One of the significant advantages of using iron sand for casting is its thermal properties. Iron sand has excellent heat retention capabilities, allowing it to support high-temperature applications. Once the mold is prepared, molten iron—often sourced from recycled iron—is poured into the cavity created by the pattern. The temperature of the molten iron typically ranges between 1200°C to 1500°C. The use of iron sand allows for a more efficient cooling process, ensuring uniformity in the final casting.
After the iron has cooled and solidified, the mold is broken open to reveal the cast component. This disassembly is done carefully to avoid damaging the newly formed part. The casting often undergoes various finishing processes, such as trimming, grinding, or sandblasting, to achieve the desired surface finish and dimensional accuracy.
Another benefit of the iron sand casting process is its environmental impact. Utilizing natural iron sand reduces the need for mined iron ore, helping to conserve our planet’s resources. Furthermore, the recycling of iron materials not only diminishes waste but also decreases energy consumption associated with melting new materials.
In conclusion, the iron sand casting process is a practical, efficient, and environmentally friendly method for producing iron components. Its ability to utilize natural resources while achieving high-quality results makes it an attractive choice for manufacturers across various industries. With ongoing advancements, this process holds the promise of further enhancing the quality and sustainability of iron casting in the future. As industries continue to innovate, the adoption of the iron sand casting process may play a crucial role in meeting the growing demand for sustainable manufacturing practices.
Post time:Sult . 14, 2024 12:11
Next:sand in resin