How to Sand Cast A Comprehensive Guide
Sand casting is a versatile and widely used method of metal casting that involves creating a mold from a sand mixture, pouring liquid metal into that mold, and then allowing it to cool and solidify. This process is favored for its simplicity and ability to produce intricate shapes, making it an excellent choice for both amateur and professional metalworkers. In this article, we’ll explore the essential steps involved in sand casting, along with some tips for achieving the best results.
Materials Needed for Sand Casting
Before diving into the process, it’s essential to gather all necessary materials
. Here’s a list of what you’ll need1. Pattern The model of the object you wish to cast, typically made from wood or plastic. 2. Sand Special casting sand, often mixed with a binding agent such as clay. 3. Mold Box A container that holds the sand and pattern. 4. Metal The type of metal you plan to cast, such as aluminum, bronze, or iron. 5. Furnace Equipment to melt the metal. 6. Tools Tools for mixing, compacting the sand, pouring the metal, and finishing the cast product.
Step-by-Step Process of Sand Casting
1. Create the Pattern Start by designing and creating a pattern of the intended casting. Ensure that the pattern includes allowances for shrinkage and draft angles, which will help in releasing the final casting from the mold.
2. Prepare the Mold - Place the pattern into a mold box. This box can be either a single or two-part mold, depending on the complexity of the pattern. - Mix the sand with a suitable binder and water to achieve the right consistency. The mixture should be pliable enough to hold its shape while being compacted around the pattern. - Fill the mold box with the sand mixture, making sure to pack it tightly around the pattern to avoid any air pockets.
3. Remove the Pattern After the sand has been packed around the pattern, carefully remove the pattern from the mold. This step must be done gently to avoid damaging the mold. You may need to use a tool to help loosen the sand.
how to sand cast
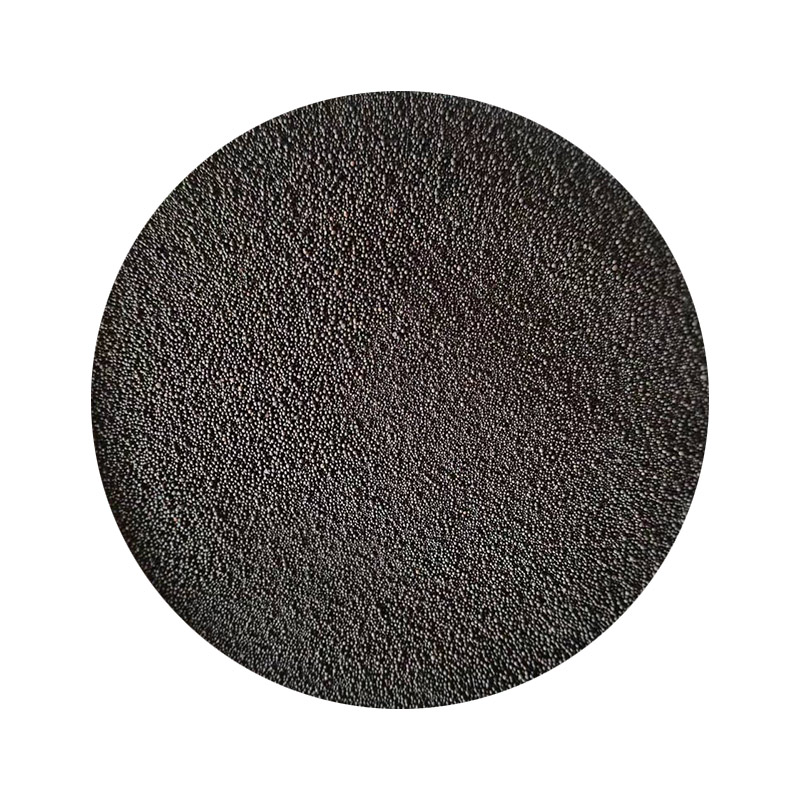
4. Create Pouring Channels To facilitate the flow of molten metal into the mold, create a sprue and runners. These are channels that guide the metal into the cavity of the mold.
5. Melt the Metal Using a furnace, heat your chosen metal until it reaches its melting point. Safety is crucial at this stage; wear appropriate protective gear including gloves, goggles, and an apron to safeguard against burns.
6. Pour the Metal Once the metal is molten, carefully pour it into the mold through the sprue. Ensure that you pour steadily to avoid splashing and spilling. Allow the metal to fill the mold completely and flow into all the cavities.
7. Cooling Let the casting cool for the appropriate amount of time. This duration depends on the type of metal and the size of the casting. It’s essential to allow it to cool completely to avoid defects.
8. Remove the Casting Once the metal has cooled, disassemble the mold carefully and remove the casting. You may need to use tools to help free it from the sand.
9. Finishing Touches Finally, clean the casting by removing any excess sand, and use tools like grinders or sanders to smooth out any rough edges. Final adjustments can also be made to meet specifications.
Conclusion
Sand casting is a rewarding process that combines creativity with craftsmanship. While it may initially seem daunting, following these steps will help you achieve success in creating your own cast metal objects. Whether you're a hobbyist or looking to produce items for a business, mastering sand casting can open up numerous possibilities for your projects. Remember to prioritize safety throughout the entire process, and enjoy the artistry of metal casting!
Post time:Samh . 07, 2024 08:59
Next:foundry sand density