Understanding the Dry Sand Casting Process
Dry sand casting is a widely employed method in the foundry industry, known for its efficiency in producing high-quality metal castings
. This process utilizes a mixture of fine sand and a binding agent, which, upon being compacted, forms a mold suitable for shaping molten metal. The following sections delve into the key aspects of the dry sand casting process, highlighting its advantages, applications, and procedures.At its core, dry sand casting involves creating molds from a sand mixture that contains a bonding agent, typically an organic resin. Unlike green sand casting, which uses moisture-laden sand, the dry sand process produces molds that are more rigid and durable. The absence of water in the mold results in minimal distortion during the casting process, making it ideal for detailed and intricate designs.
One of the significant advantages of dry sand casting is the superior surface finish it offers. The tightly packed sand grains create smooth mold surfaces that yield castings with minimal defects. Additionally, the high dimensional stability of dry sand molds enables manufacturers to achieve precise tolerances in their final products. This quality is particularly relevant in applications such as automotive and aerospace components, where precision engineering is crucial.
dry sand casting process
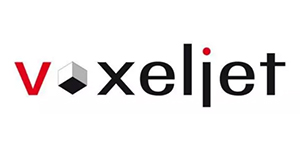
The dry sand casting process begins with the preparation of the sand mixture, which is usually heated to improve its binding properties. The binder is then mixed with the sand to create a uniform blend, followed by a compaction process where the mixture is packed into a mold pattern. This step is critical, as proper compaction ensures the mold can withstand the weight and pressure of the molten metal being poured.
Once the mold is prepared, the next step involves curing the sand mixture, which often requires the application of heat or a chemical catalyst. This curing process solidifies the mold structure, making it robust enough to handle the pouring of molten metal at high temperatures. After curing, the mold is ready for metal pouring, typically done in a controlled environment to minimize contamination and defects.
After the molten metal is poured into the mold and allowed to cool, the casting process concludes with the removal of the sand mold. The dry sand molds can be easily broken apart, facilitating the extraction of the finished casting. This ease of mold removal can significantly reduce cycle times, enhancing overall production efficiency.
In conclusion, dry sand casting is a highly effective method for producing metal parts with excellent dimensional accuracy and surface finish. Its ability to handle complex designs while maintaining quality makes it a preferred choice in various industries, particularly those demanding high precision. As technology evolves, innovations in materials and processes are likely to enhance the capabilities of dry sand casting further, paving the way for even more advanced applications in manufacturing.
Post time:Samh . 24, 2024 11:52
Next:A Comprehensive Guide to the Sand Casting Process and Techniques