Coated Sand Casting An Innovative Approach to Metal Casting
Coated sand casting is an advanced method in the field of metal casting that combines the traditional sand casting process with modern techniques to enhance the quality and efficiency of cast parts. This method leverages the benefits of a resin-coated sand mixture, which significantly improves the surface finish, dimensional accuracy, and overall performance of castings.
The Basics of Sand Casting
At its core, sand casting involves creating a mold from a mixture of sand and a binding agent. Traditionally, this process has been valued for its flexibility, low cost, and ability to produce complex shapes. However, conventional sand molds often suffer from issues such as rough surfaces and significant shrinkage, which can compromise the quality of the final product.
To address these challenges, manufacturers have turned to coated sand, wherein the sand grains are coated with a thermosetting resin. This coating process enhances the properties of the sand, making it more durable and capable of withstanding the molten metal during casting.
Improvements Offered by Coated Sand
1. Superior Surface Finish One of the primary advantages of using coated sand is the remarkable improvement in the surface finish of the cast parts. Traditional sand molds often leave a rough texture on the cast surface; however, with coated sand, the fine coating helps create a smoother finish. This aspect is particularly crucial in industries where aesthetics and precision are paramount, such as automotive and aerospace manufacturing.
coated sand casting
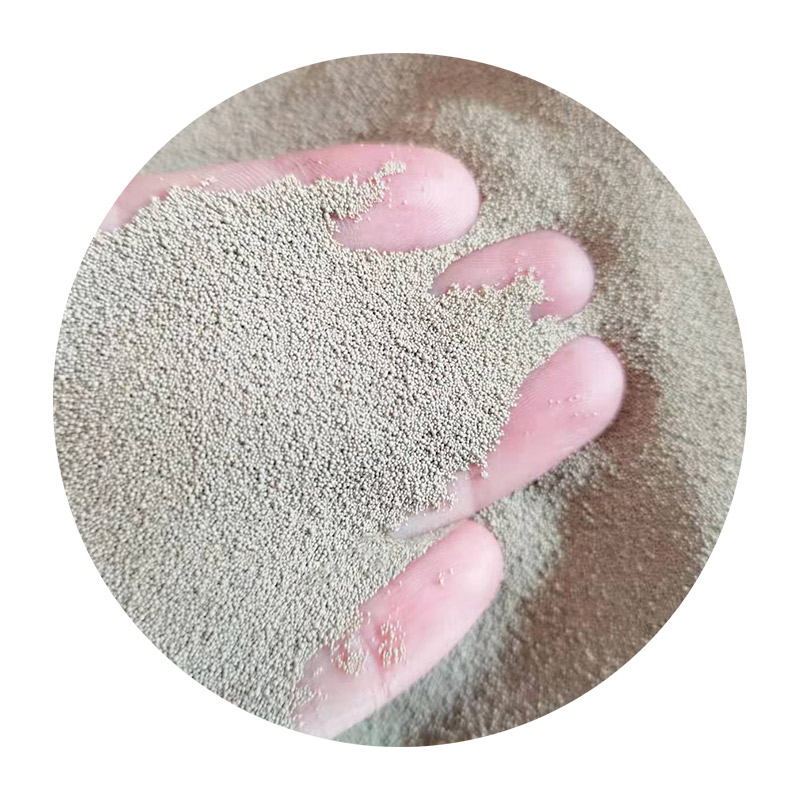
2. Dimensional Accuracy Coated sand casting results in better dimensional accuracy compared to traditional methods. The heat from the molten metal causes the resin to cure, causing the sand particles to bond together more effectively. This results in molds that can retain their shape under thermal stress, reducing shrinkage and warping during the cooling process. Consequently, parts produced with coated sand often require less machining, leading to significant cost savings.
3. Increased Strength The use of resin-coated sand enhances the mechanical strength of the mold, allowing it to withstand the stresses imposed during the pouring and solidification of hot metals. This property is especially beneficial for large castings or intricate designs that may otherwise be prone to mold failure.
4. Reduced Environmental Impact Coated sand casting also has environmental benefits. The use of resin-coated sand can reduce the amount of sand waste generated because the molds can be reused multiple times without significant degradation. Additionally, many modern resins used in coated sand applications are designed to be less harmful, improving workplace safety and reducing emissions.
Applications in Industry
The versatility of coated sand casting makes it suitable for a wide range of applications across various industries. Its ability to produce high-quality components makes it a preferred technique in automotive parts production, where precision and durability are critical. Furthermore, sectors like aerospace, marine, and even art casting benefit from the superior attributes of coated sand castings.
Conclusion
Coated sand casting represents a significant evolution in the traditional sand casting method. By leveraging advanced materials and techniques, this innovative approach addresses many of the limitations associated with conventional sand molds. The enhanced surface finish, improved dimensional accuracy, increased strength, and reduced environmental impact make coated sand casting an attractive choice for manufacturers striving for excellence in their casting pursuits. As technology continues to advance, the adoption of coated sand casting is likely to grow, further transforming the landscape of metal casting.
Post time:Samh . 12, 2024 03:44
Next:sand 3d