The Role of Ceramsite Foundry Sand in Modern Casting Techniques
In the world of metallurgy and casting, the choice of materials is crucial for producing high-quality components. One of the materials that is gaining recognition for its effectiveness is ceramsite foundry sand. This innovative sand is made from expanded clay aggregates, offering numerous benefits over traditional foundry sands. In this article, we will explore the properties of ceramsite foundry sand, its advantages in casting processes, and its growing application across various industries.
Understanding Ceramsite Foundry Sand
Ceramsite foundry sand is produced by heating clay minerals to high temperatures, which causes the clay to expand and form lightweight, spherical particles. This process, known as granulation, results in a material with superior thermal resistance, chemical stability, and a lower density compared to conventional foundry sands such as silica sand. The unique properties of ceramsite make it an ideal choice for foundry applications where performance, quality, and sustainability are key considerations.
Key Advantages of Ceramsite Foundry Sand
1. Thermal Properties One of the standout features of ceramsite foundry sand is its excellent thermal conductivity. This property enables better heat distribution during the casting process, leading to uniform temperature profiles and reducing the likelihood of defects such as warping and shrinkage.
2. Low Density Due to its lightweight nature, ceramsite reduces the overall weight of the molding material. This characteristic not only eases handling and transportation but also minimizes the strain on casting equipment, potentially extending its service life.
3. Chemical Resistance Ceramsite foundry sand exhibits a high level of chemical stability, which is crucial when working with various metal alloys. Its resistance to chemical reactions minimizes sand contamination and ensures a cleaner casting environment, ultimately improving the quality of the final product.
4. Reusability Unlike traditional foundry sands that often require extensive processing and treatment after use, ceramsite foundry sand can be easily reclaimed and reused multiple times without significant degradation in performance. This property not only lowers production costs but also contributes to more sustainable manufacturing practices.
ceramsite foundry sand
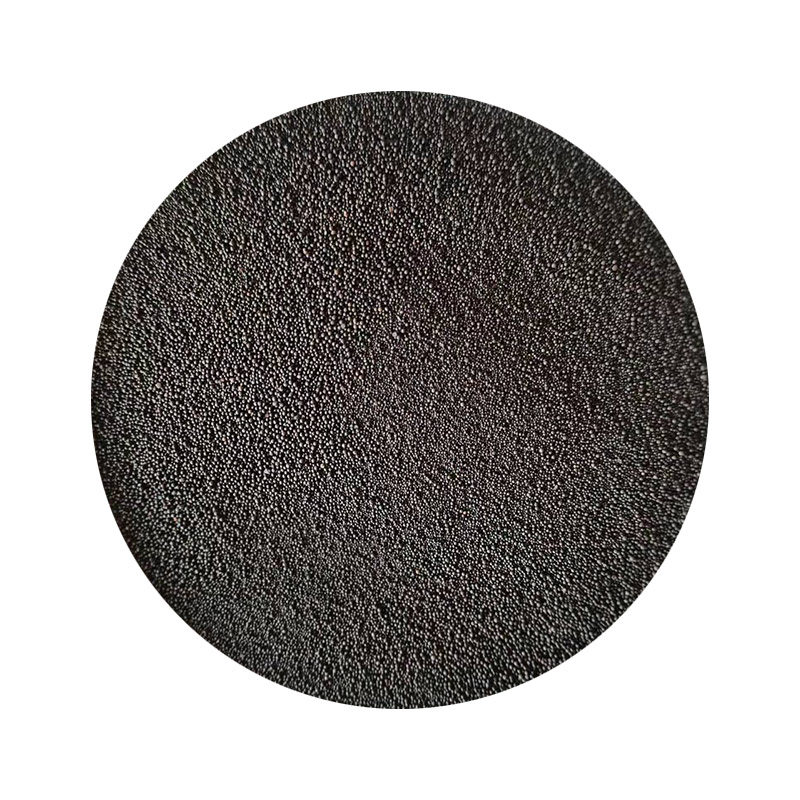
5. Improved Surface Finish The spherical shape and smooth texture of ceramsite particles contribute to a superior surface finish on cast components. This advantage is particularly significant in industries where aesthetic appeal and precision are paramount, such as automotive and aerospace manufacturing.
Applications in Various Industries
Ceramsite foundry sand is becoming increasingly popular across various sectors, including automotive, aerospace, and metalworking. In the automotive industry, for instance, it is used for casting engine blocks, cylinder heads, and intricate components that require a high degree of precision and durability. The aerospace sector benefits from ceramsite foundry sand's thermal properties, which allow for the production of lightweight yet strong parts essential for aircraft performance.
Moreover, ceramsite foundry sand is being utilized in the production of non-ferrous casting applications, such as aluminum and magnesium components. Its ability to handle high temperatures makes it suitable for these materials, which often require specific conditions during the casting process.
Environmental Considerations
As industries move towards more sustainable practices, ceramsite foundry sand offers an eco-friendly alternative to traditional casting materials. Its ability to be reused multiple times reduces waste and minimizes the environmental impact associated with disposing of used foundry sand. Additionally, the production of ceramsite from clay is a relatively low-impact process compared to the mining and processing of silica sands, making it a more sustainable choice for foundries.
Conclusion
Ceramsite foundry sand represents a significant advancement in casting technology, offering numerous benefits that enhance the quality and efficiency of metalworking processes. Its thermal properties, low density, chemical resistance, and reusability make it a valuable material for modern foundries looking to improve productivity while minimizing environmental impact. As more industries recognize the advantages of ceramsite, it is likely to become a standard choice in the foundry landscape, paving the way for higher quality castings and a sustainable future in manufacturing.
Post time:Samh . 28, 2024 01:28
Next:Inspired by supersand for creative play and imaginative adventures for all ages