The Advantages of Ceramic Sand Casting in Modern Manufacturing
Ceramic sand casting is an innovative and highly efficient casting method that is gaining popularity in various industrial applications. This technique employs a unique mixture of sand and ceramic materials to produce molds that are both strong and capable of capturing intricate details. As industries increasingly seek precision and cost-effectiveness, ceramic sand casting emerges as a formidable solution.
One of the primary advantages of ceramic sand casting is its ability to achieve exceptional surface finishes and precision. The ceramic particles in the sand enable the production of molds that can withstand high temperatures, providing a durable and stable structure during the casting process. This inherently results in fewer defects and minimizes the need for secondary machining operations, thereby enhancing overall productivity.
Additionally, ceramic sand itself offers superior thermal properties, which are crucial in controlling the cooling rates of molten metal during casting. Effective thermal management ensures that the metal solidifies uniformly, leading to improved mechanical properties in the final component. This is particularly beneficial in industries such as aerospace and automotive, where material performance is paramount.
Another notable benefit of ceramic sand casting is its versatility. This method can accommodate a wide range of metals, including aluminum, bronze, and iron, making it suitable for diverse applications. Moreover, the adaptability of ceramic sand molds allows for the production of both small and large components, catering to the varying demands of different sectors.
ceramic sand casting
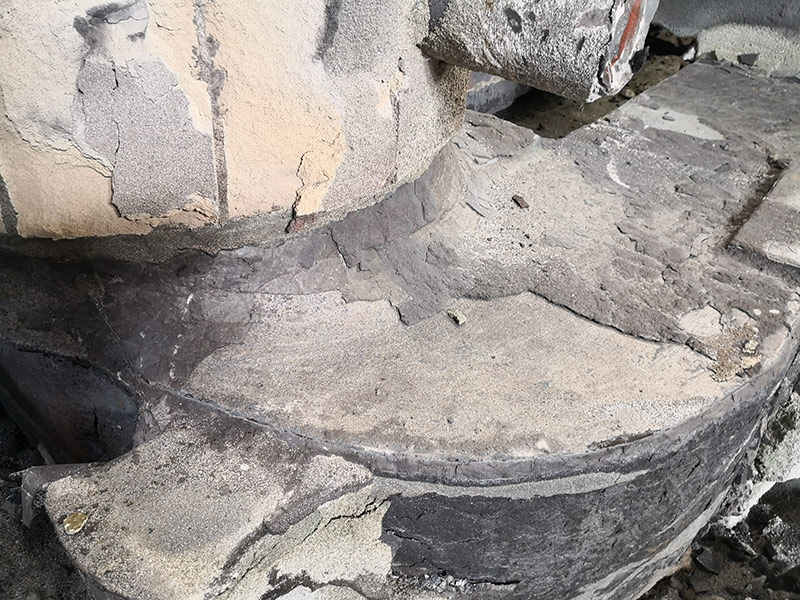
Ceramic sand casting also boasts environmental advantages compared to conventional casting methods. Traditional sand casting often involves the use of resin-bonded sands that release harmful volatiles into the atmosphere. In contrast, ceramic sand is more environmentally friendly, as it does not produce harmful emissions during the casting process. Moreover, ceramic sand can be reused multiple times, contributing to reduced material waste and lower overall production costs.
The ability to create complex geometries is another significant advantage of ceramic sand casting. The process can produce intricate shapes with fine details that would be challenging to achieve with traditional casting techniques. This level of design freedom allows engineers and designers to innovate without the limitations typically imposed by conventional molds.
However, like any manufacturing process, ceramic sand casting comes with its challenges. The initial setup costs for creating ceramic molds can be higher than traditional sand casting. Nevertheless, the long-term benefits, including reduced machining time and improved product quality, often offset these initial investments.
In conclusion, ceramic sand casting stands out as a modern manufacturing method that offers numerous benefits, including precision, versatility, environmental sustainability, and the ability to produce complex geometries. As industries continue to evolve and strive for efficiency and quality, the adoption of ceramic sand casting is likely to grow. By embracing this innovative technique, manufacturers can enhance their production capabilities and remain competitive in the ever-changing landscape of modern manufacturing.
Post time:Dàmh . 08, 2024 12:01
Next:Understanding the Costs of Sand Casting Processes for Various Industries