Advantages and Disadvantages of Sand Casting
Sand casting, one of the oldest and most widely used metal casting processes, plays an essential role in manufacturing a variety of components, from automotive parts to intricate machine components. This method involves creating a mold from a mixture of sand, clay, and water, into which molten metal is poured. While sand casting boasts several advantages, it also presents certain disadvantages that manufacturers must consider. In this article, we will explore the merits and drawbacks of sand casting to understand its overall impact on the manufacturing industry.
Advantages of Sand Casting
1. Cost-Effectiveness One of the primary advantages of sand casting is its affordability. The raw materials, primarily sand, are inexpensive and readily available. Additionally, the initial setup costs for sand casting tend to be lower compared to other casting methods such as die casting or investment casting. This makes it an attractive option for small-scale production and prototypes.
2. Versatility Sand casting can accommodate a wide range of metals and alloys, including aluminum, iron, and bronze. This flexibility allows manufacturers to produce various components for diverse applications. The process is also suitable for large parts that may be challenging to cast using other methods.
3. Large Component Production Sand casting is particularly advantageous for producing large and heavy components. Its ability to create molds of significant size without the constraints of sophisticated tooling means that manufacturers can produce oversized parts that are essential in industries such as construction and mining.
4. Complex Shapes While some casting methods are limited by the design of the mold, sand casting allows for the creation of intricate shapes and designs. The sand mold can be easily manipulated, enabling the production of complex geometries that meet specific design requirements.
5. Ease of Customization The sand casting process allows for easy modifications to the mold design. If a design needs to be altered, adjustments can be made to the sand mold without significant downtime or cost. This adaptability is particularly beneficial in research and development phases where alterations may be frequent.
advantages and disadvantages of sand casting
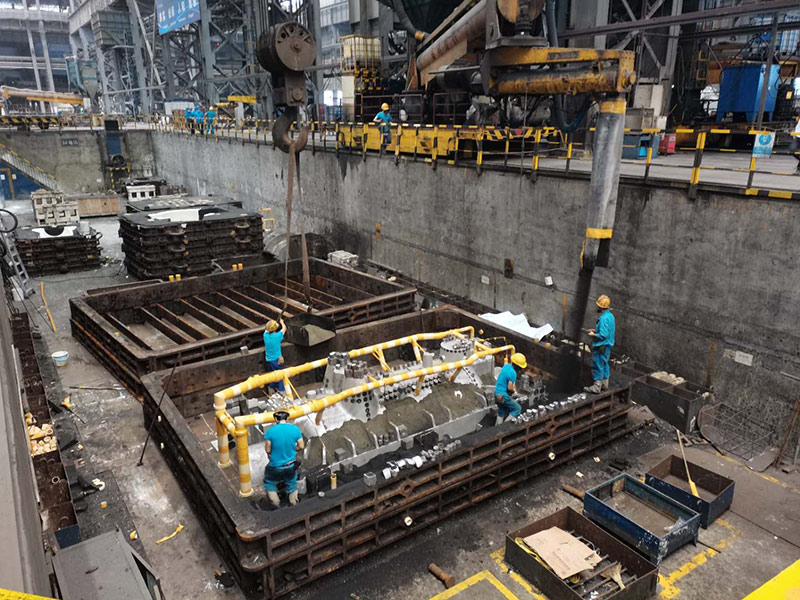
Disadvantages of Sand Casting
1. Surface Finish Quality One of the notable disadvantages of sand casting is the surface finish of the final product. Sand molds can leave a rough surface texture, which may require additional machining or finishing processes to meet stringent surface quality requirements. This can increase the overall production time and costs.
2. Dimensional Accuracy Sand casting traditionally has lower dimensional accuracy compared to other casting techniques. The nature of sand as a mold material can lead to variations in the final dimensions of the cast part. For applications where tight tolerances are critical, this can be a significant drawback.
3. Environmental Concerns The sand casting process generates waste, including scrap metal and used sand. Additionally, the production of molds involves binding agents and coatings that can have environmental impacts. While recycling methods for sand are available, they may not be sustainable in all cases, raising concerns about the overall ecological footprint of the process.
4. Labor-Intensive Although the initial setup cost is low, the sand casting process can be labor-intensive. It often requires skilled workers to create the molds and handle the metal pouring, which may add to labor costs and production time. Automation can help reduce some labor requirements, but it may not be feasible for all operations.
5. Limited Production Rate Sand casting is generally not suitable for high-volume production due to its slower cycle times compared to other methods. Each mold must be created individually, which can be time-consuming, making it less efficient for large-scale productions where speed is essential.
Conclusion
In conclusion, sand casting remains a vital process in the manufacturing industry, offering a unique blend of cost-effectiveness, versatility, and the capability to produce complex shapes. However, its disadvantages, including surface finish issues, limited dimensional accuracy, and labor intensity, cannot be overlooked. Ultimately, the decision to use sand casting should be based on the specific requirements of the project, balancing the benefits and drawbacks to determine the best manufacturing approach. As technology advances, it is likely that some of the disadvantages associated with sand casting may be mitigated, allowing this age-old technique to remain relevant in modern manufacturing.
Post time:Samh . 04, 2024 19:38
Next:sand casting history