The Integration of 3D Printing and Sand Casting A Revolutionary Approach in Manufacturing
In recent years, the manufacturing industry has witnessed significant advancements, particularly with the rise of additive manufacturing techniques such as 3D printing. Among various applications, combining 3D printing technology with traditional sand casting methods has emerged as a revolutionary approach, enhancing efficiency, precision, and the overall production process.
Sand casting, one of the oldest manufacturing processes, involves creating a mold from a sand mixture to shape molten metal. Traditionally, this process can be time-consuming and often entails high labor costs and material waste. The introduction of 3D printing into sand casting offers innovative solutions to these challenges, leading to improved product quality and reduced lead times.
One of the main advantages of integrating 3D printing with sand casting is the ability to produce complex geometries that would be difficult or impossible to achieve with conventional techniques. Designers and engineers can create intricate patterns directly using 3D modeling software, which are then printed using sand 3D printers. This capability not only expands the design possibilities but also allows for greater customization of products to meet specific customer requirements.
The process begins with the creation of a digital model using computer-aided design (CAD) software. Once the model is finalized, a 3D printer produces a mold by layering sand and a binding agent according to the specifications of the design. This method significantly reduces the time required to create molds compared to traditional techniques that rely on manual labor and multiple machining processes. Consequently, manufacturers can turn around prototypes more quickly, facilitating rapid iteration and testing.
Moreover, the precision offered by 3D printing helps minimize material waste. Traditional sand casting often produces excess material that must be machined away after casting, while 3D-printed molds are created to exact specifications. The result is a more sustainable manufacturing process that conserves resources and reduces costs, making 3D printing an appealing alternative for environmentally conscious businesses.
3d printing sand casting
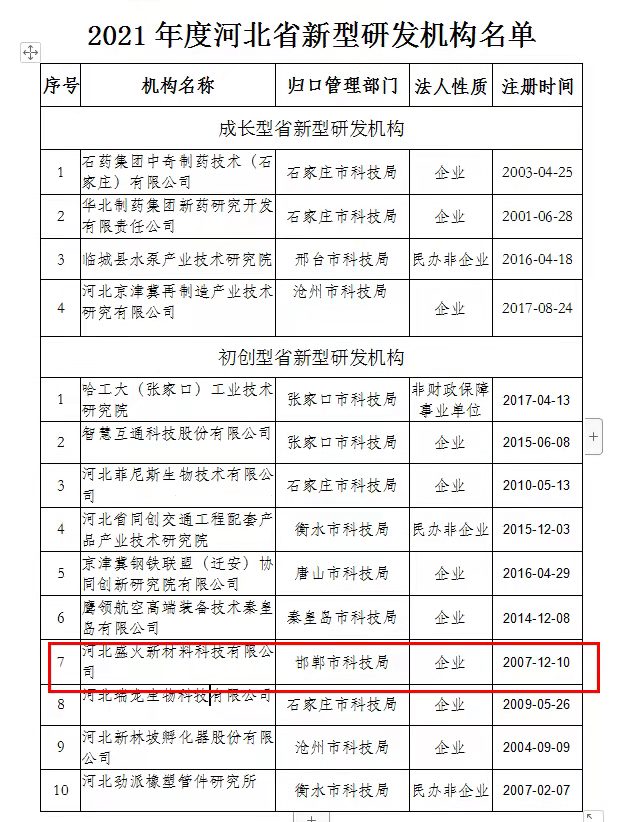
The integration of 3D printing with sand casting also improves the overall quality of the final product. The meticulous detail achievable with 3D printed molds enhances the surface finish of cast parts, reducing the need for post-processing. This seamless transition from design to production not only elevates product quality but also bolsters customer satisfaction by delivering products that meet or exceed expectations.
Furthermore, this synergy between technologies opens avenues for innovation in industries like automotive, aerospace, and art. For instance, automotive companies can produce lightweight components that are complex in shape, aiding in the reduction of fuel consumption and enhancement of vehicle performance. Similarly, the aerospace sector benefits from weight savings and improved aerodynamics achieved through intricate designs. Artists and designers can explore new creative dimensions, producing unique sculptures or functional items that showcase their artistic vision.
Despite the evident benefits, it is crucial to consider the challenges associated with this integration. The initial investment in 3D printing technology and equipment can be significant, which may deter smaller manufacturers from adopting these innovations. Moreover, there is a learning curve involved in adapting to new technologies, requiring training and education for staff to harness the full potential of 3D printing and sand casting.
Nevertheless, the continuous evolution of technology is likely to mitigate these challenges. As 3D printing becomes more accessible and cost-effective, it is expected that more manufacturers will incorporate these techniques into their production processes. The result will be a more dynamic industry, capable of rapidly responding to changing market demands while maintaining high standards of quality and sustainability.
In conclusion, the integration of 3D printing and sand casting represents a significant leap forward in manufacturing technology. By marrying the precision of additive manufacturing with the traditional strengths of sand casting, industries can achieve remarkable advancements in efficiency, sustainability, and product quality. As we continue to explore the potential of these technologies, we can anticipate a future where manufacturing is not only more innovative but also agile enough to meet the evolving needs of consumers across the globe.
Post time:Faoi . 02, 2025 15:35
Next:نوع فرایند کاستن شن