3D Printing Patterns for Sand Casting Revolutionizing Traditional Metal Casting
In recent years, the integration of 3D printing technology into traditional manufacturing processes has garnered significant attention. One of the most transformative applications of 3D printing is in the field of sand casting, a process where molten metal is poured into a mold formed from sand. The introduction of 3D printed patterns has changed the landscape of sand casting, offering numerous advantages over conventional methods.
Traditionally, making patterns for sand casting involves machining or sculpting materials such as wood, metal, or plastic. This process can be time-consuming and expensive, especially when it involves complex designs or the need for multiple iterations. In contrast, 3D printing allows for rapid prototyping and the production of intricate patterns directly from a digital model. This not only reduces lead times but also significantly cuts down costs associated with material waste and labor.
3D Printing Patterns for Sand Casting Revolutionizing Traditional Metal Casting
Moreover, 3D printing enables the creation of highly customized patterns tailored to specific applications. In industries such as aerospace and automotive, where optimizing performance is critical, businesses can produce unique designs that meet stringent specifications. This level of customization not only leads to better-performing parts but also helps in rapid iteration and testing, propelling the development cycle forward.
3d printing patterns for sand casting
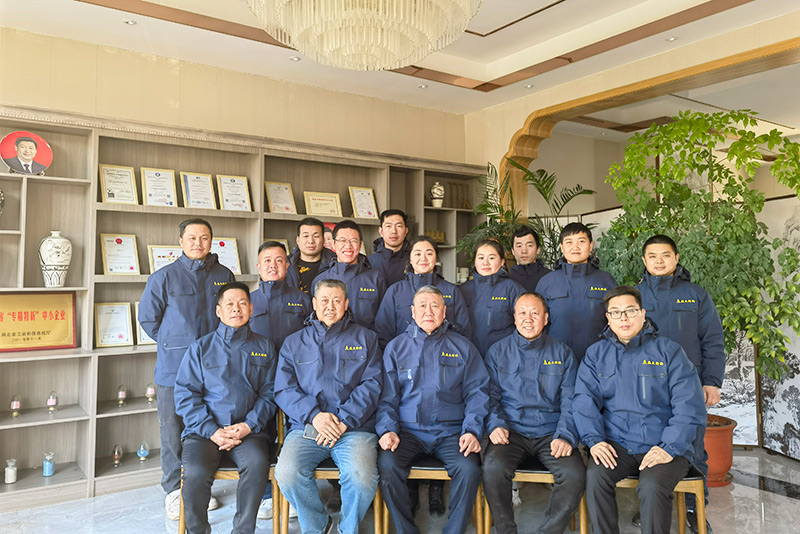
Another significant advantage of 3D printing in sand casting is the reduction in material waste. Traditional pattern-making often involves excessive cutting and machining, generating considerable scrap material. 3D printing, on the other hand, is an additive manufacturing process that builds objects layer by layer. This means that only the necessary material is used, which is particularly beneficial in today’s eco-conscious landscape where sustainability is a priority.
Additionally, the adoption of 3D printed patterns can also enhance the overall quality of the final cast product. The precision of 3D printing ensures that the patterns are produced to exact specifications, minimizing the likelihood of defects in the castings. Furthermore, the smooth surface finish achieved through 3D printing reduces the need for extensive post-processing, which previously was vital to eliminate imperfections that could affect the performance of the final product.
Despite these advantages, utilizing 3D printing for sand casting is not without its challenges. The choice of materials for 3D printing patterns can limit the casting process, as some printed materials may not withstand the high temperatures involved. Additionally, the integration of new technologies often requires a learning curve, as operators must adapt to new workflows and equipment.
In conclusion, 3D printing patterns for sand casting marks a significant advancement in manufacturing technology, providing improved design flexibility, reduced lead times, and enhanced sustainability. As industries continue to embrace this innovative approach, we can expect to see an increased adoption of 3D printing in sand casting applications, leading to higher-quality products and streamlined production processes. The future of metal casting is undoubtedly evolving, and 3D printing stands at the forefront of this revolution, ready to reshape conventional practices for years to come.
Post time:Sult . 29, 2024 01:15
Next:Understanding the Properties and Applications of Sand Casting in Iron Production