3D Printing for Sand Casting Revolutionizing the Foundry Industry
The foundry industry is undergoing a significant transformation, driven by technological advancements and the quest for efficiency. Among these innovations, 3D printing for sand casting is emerging as a groundbreaking solution, optimizing traditional methods and offering new possibilities for manufacturers.
3D Printing for Sand Casting Revolutionizing the Foundry Industry
One of the most significant advantages of 3D printing in sand casting is the reduction in lead times. Designers can quickly create complex geometries that would be challenging or impossible to achieve using traditional methods. The ability to produce molds on-demand minimizes the delays associated with pattern production and storage, significantly accelerating the overall manufacturing process. This agility allows companies to respond faster to market demands and maintain a competitive edge.
3d printing for sand casting
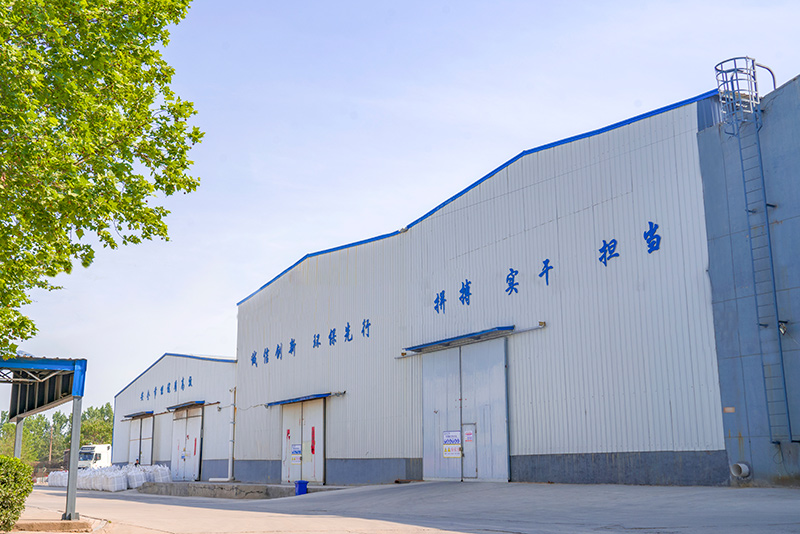
Moreover, 3D printing enhances design flexibility. Engineers can experiment with intricate shapes and innovative designs that break away from the constraints of traditional mold-making techniques. This freedom fosters creativity, enabling the development of lightweight components and optimized geometries that improve performance while reducing material usage. As a result, manufacturers can not only achieve better-quality products but also reduce waste, aligning with the industry's growing emphasis on sustainability.
Furthermore, 3D printing for sand casting supports the production of small-batch or customized orders. In the past, producing low-volume castings was often uneconomical due to the high costs associated with creating physical patterns. However, with 3D printed molds, foundries can produce unique items without incurring prohibitive expenses, allowing them to cater to niche markets or specialized applications. This is particularly valuable in industries such as automotive, aerospace, and medical devices, where tailored solutions are often required.
Despite its many advantages, the integration of 3D printing in sand casting is not without challenges. Foundries must adapt to new materials and processes, requiring a skilled workforce capable of operating advanced printing technologies. Additionally, the initial investment in 3D printing systems can be substantial, which may deter some companies from making the transition.
In conclusion, 3D printing for sand casting represents a pivotal development in modern manufacturing. By offering rapid prototyping, design flexibility, and the ability to produce customized components, it is reshaping the foundry landscape. As technology continues to evolve, it is likely that more companies will embrace 3D printing to enhance their production capabilities, ultimately leading to improved efficiency, reduced costs, and higher-quality products. The future of sand casting is indeed bright, with 3D printing at its forefront, ready to drive innovation and excellence in the industry.
Post time:Dàmh . 06, 2024 11:36
Next:sand casting foundry process