Understanding Sand Casting Services A Comprehensive Guide
Sand casting, also known as sand mold casting, is one of the oldest and most versatile manufacturing processes used in metalworking today. This technique is at the heart of countless industries, producing intricate and robust metal components used in everything from machinery to art sculptures. In this article, we will explore the sand casting service, its process, advantages, applications, and choose the right service provider for your needs.
What is Sand Casting?
Sand casting involves creating a mold using sand, which is then used to form metal parts. The process begins with creating a pattern of the desired component, typically made from metal or plastic. The pattern is then placed in a specially prepared sand mixture, where it is covered with sand to form a mold. Once the mold is complete, it is opened, and the pattern is removed, leaving behind a cavity that replicates the desired shape.
The molten metal is poured into this cavity, allowed to cool and solidify, and then the sand mold is broken away to reveal the finished casting. This method accommodates a variety of metals, including aluminum, iron, and steel, making it an ideal choice for producing various components across different sectors.
The Sand Casting Process
1. Pattern Making The first step involves creating a pattern of the component. This is a crucial stage as the accuracy of the pattern will directly affect the final part's precision and quality.
2. Mold Preparation The pattern is placed in a flask, and a mixture of sand and a binding agent is packed around it to form the mold. Once compacted, the mold is ready for pouring.
3. Core Making (if necessary) For complex shapes, cores made of sand can be added to the mold. These cores create internal passages or cavities within the cast metal.
4. Pouring The metal is melted and poured into the pre-prepared mold cavity. This step must be executed with care to avoid defects such as air pockets or incomplete filling.
5. Cooling and Solidification The molten metal is allowed to cool and solidify. The cooling time can vary based on the metal type and the part's size.
6. Mold Removal After the metal has cooled, the sand mold is broken away, revealing the cast part. This step can be labor-intensive, especially for larger components.
sand casting service
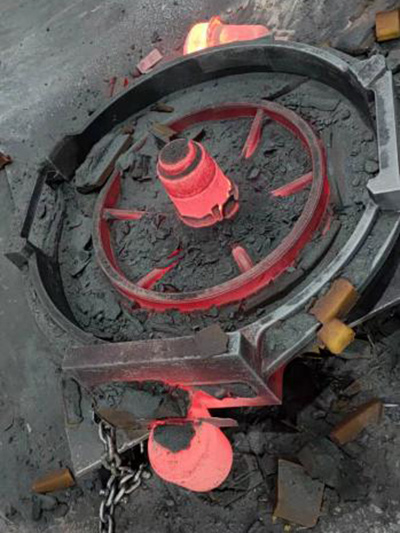
Advantages of Sand Casting
One of the standout advantages of sand casting is its cost-effectiveness, particularly for low to medium volumes of production. Unlike other casting methods, sand casting does not require specialized or expensive equipment, making it accessible for many manufacturers. Another significant benefit is the flexibility it offers. Sand casting can produce parts of varying sizes and complexities, which is essential for custom projects.
Additionally, sand casting is suitable for a broad range of materials, allowing manufacturers to produce components tailored to specific strength, weight, and corrosion resistance requirements.
Applications of Sand Casting
Sand casting finds applications across various domains, including
- Automotive Engine blocks, cylinder heads, and transmission cases are often manufactured through sand casting due to the high strength required. - Aerospace Components like turbine blades and landing gear are produced using this method, emphasizing the need for precision and material integrity. - Construction Architectural features, structural components, and machinery parts are frequently cast in sand to meet specific design requirements. - Art and Sculpture Many artists and sculptors utilize sand casting to produce intricate designs and sculptures, leveraging the technique’s versatility.
Choosing the Right Sand Casting Service
When selecting a sand casting service, consider factors such as experience, industry specialization, production capacity, and quality control measures. A reputable service provider will guide you through the entire process, from initial design to final production, ensuring that the finished products meet your specifications and industry standards.
Conclusion
Sand casting remains a cornerstone of metalworking due to its unique advantages and versatility. As industries evolve and demand for customized components increases, the relevance of sand casting continues to grow. When engaging with a sand casting service, understanding the process and its benefits will empower you to make informed decisions that lead to high-quality outcomes for your projects.
Post time:Nov . 05, 2024 06:05
Next:application of sand casting process