The Importance of Quality Metal Casting Sand in Foundries
Metal casting is one of the most significant industrial methods used for producing complex parts and components. The process relies heavily on various raw materials, among which casting sand plays a critical role. High-quality metal casting sand is vital for forming molds that withstand the heat and pressure of molten metal. This article explores the different types of metal casting sand available for sale, their properties, and the factors that contribute to their quality.
Types of Casting Sand
Casting sand comes in various types, each suited for specific applications in the foundry industry. The most common types include silica sand, olivine sand, and zircon sand
1. Silica Sand This is the most widely used casting sand due to its availability and cost-effectiveness. Silica sand derives its properties from quartz, making it resilient under high temperatures. It's especially useful for producing molds that require fine details and intricate designs.
2. Olivine Sand Known for its high melting point and thermal stability, olivine sand is a premium choice for casting high-temperature alloys. Its resistance to thermal shock makes it ideal for critical applications where precision is paramount.
3. Zircon Sand Zircon sand offers exceptional dimensional stability and minimal expansion under heat. It is typically used for high-performance applications and in molds where surface finish is crucial. Though more expensive than silica and olivine sands, its unique properties often justify the cost.
Properties of Quality Casting Sand
The quality of casting sand directly affects the outcomes of the casting process, making it essential that manufacturers understand what to look for in high-quality materials
- Grain Size Uniform grain size is essential for producing consistent molds. Molding sands with a mix of grain sizes can help achieve the desired surface finish. Fine grains contribute to fine details, while coarser grains provide strength.
metal casting sand for sale
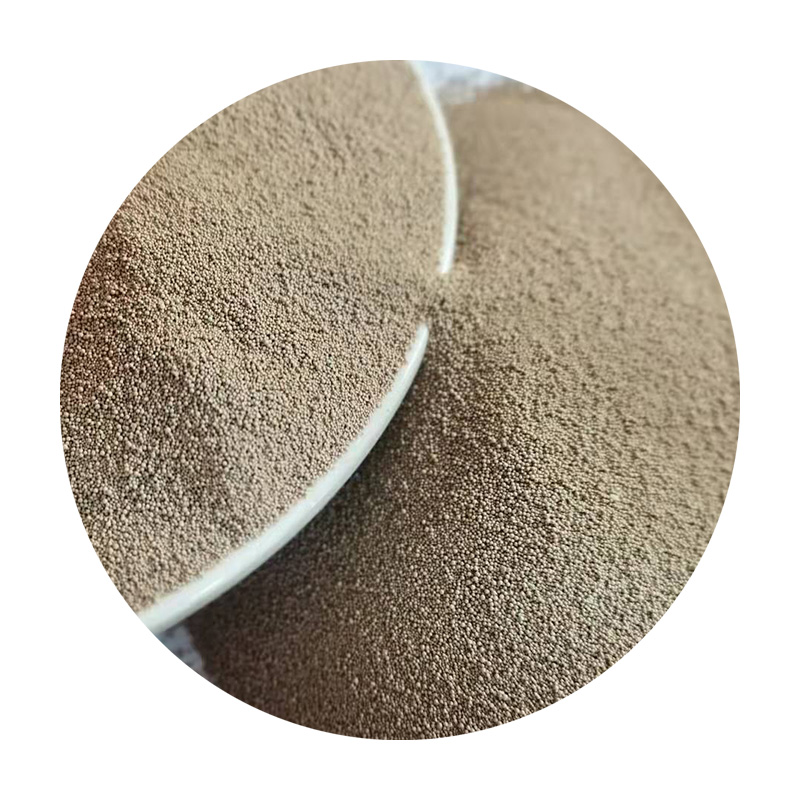
- Permeability Good permeability allows gases to escape during the casting process, reducing the risk of defects. Sands with optimal permeability ensure a smoother casting process and high-quality finished products.
- Shape The shape of sand grains influences how well they pack together. Angular grains tend to create stronger molds, while round grains are easier to handle but may not provide as much strength.
- Thermal Stability The ability of sand to withstand high temperatures without decomposing is critical, especially in the casting of ferrous and non-ferrous alloys. Quality sands maintain their properties even at elevated temperatures.
The Role of Quality Control
When purchasing metal casting sand, it's essential to ensure stringent quality control measures are in place. Trusted suppliers often provide detailed specifications and test results, indicating the properties of the sand and how they meet industry standards. Regular testing through methods like sieve analysis, permeability testing, and thermal analysis can ensure that the casting materials are in optimal condition for effective use in the foundry.
Environmental Considerations
With the rise of sustainability in the manufacturing sector, the environmental impact of casting materials cannot be overlooked. Many companies are now seeking eco-friendly options for casting sands. Recycleable and biodegradable options are emerging, offering foundries a way to minimize their environmental footprint while maintaining high-quality standards.
Conclusion
Metal casting sand is an indispensable part of the casting industry, influencing the quality and performance of finished products. As foundries seek to improve production efficiency and product quality, investing in high-quality casting sand becomes a key consideration. Whether it's silica, olivine, or zircon sand, the right choice will depend on the specific requirements of the casting process. As demand for quality casting materials continues to grow, sourcing from reputable suppliers will ensure that foundries can produce parts that meet the highest standards of excellence and innovation.
Post time:Nov . 04, 2024 23:30
Next:advantage of sand casting