Lost Foam Casting Revolutionizing Foundry Practices
Lost foam casting (LFC) is an innovative manufacturing process that has gained significant traction in the foundry industry over the past few decades. This technique combines traditional casting methods with modern technology to create complex metal parts with enhanced precision and reduced production costs. In this article, we will delve into the fundamentals of lost foam casting, its advantages, applications, and the future outlook of this remarkable process.
The Fundamentals of Lost Foam Casting
The lost foam casting process involves creating a foam pattern that is coated with a refractory material to form a shell. This foam pattern, typically made from polystyrene, is then placed in a casting mold. Once the mold is set, molten metal is poured into it. The extreme temperature of the molten metal causes the foam to vaporize, leaving behind a cavity in the exact shape of the desired part. This method eliminates the need for traditional core making and can produce near-net-shape components.
Advantages of Lost Foam Casting
One of the most significant advantages of lost foam casting is its ability to produce complex geometries that would be difficult or impossible to achieve with conventional casting methods. The foam patterns can be designed without the constraints of draft angles, allowing for more intricate designs and reduced machining requirements. Additionally, LFC typically results in lower scrap rates, as it reduces the need for machining operations.
Another notable benefit is the reduction in production time. The lost foam process streamlines several stages of traditional casting, such as pattern making and handling, which can lead to quicker turnaround times. This efficiency translates into cost savings, making LFC an attractive option for many manufacturing operations.
lost foam casting foundry
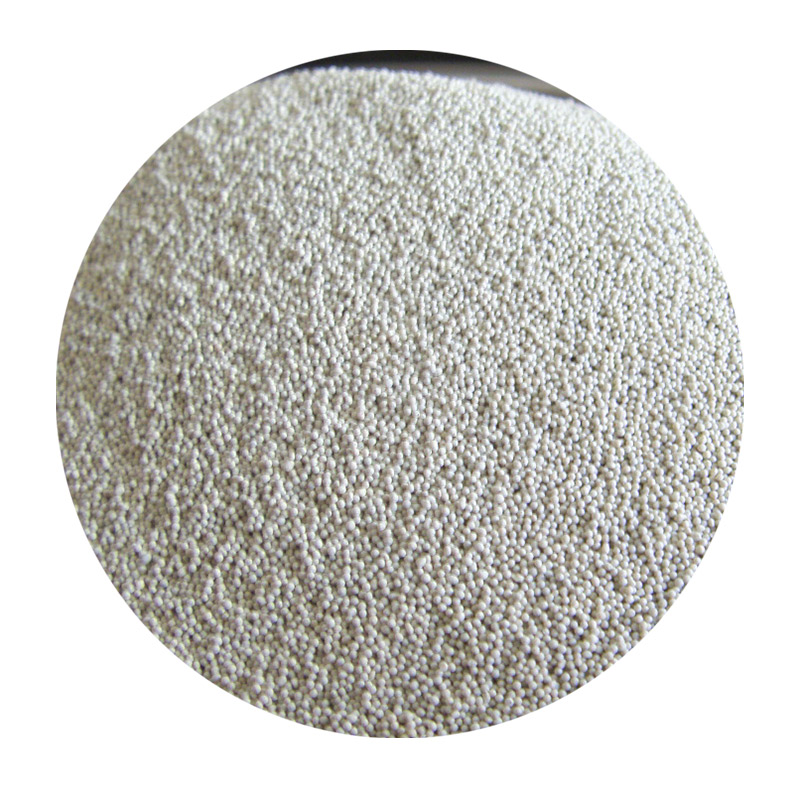
Applications of Lost Foam Casting
Lost foam casting is employed across various industries, including automotive, aerospace, and manufacturing. In the automotive sector, LFC is used to produce engine blocks, cylinder heads, and other critical components that require high precision. The aerospace industry also benefits from LFC's ability to create lightweight and complex parts that are essential for performance and fuel efficiency.
Moreover, LFC is gaining popularity in the production of intricate art pieces and sculptures, where traditional molding methods may fall short in capturing fine details. The versatility of lost foam casting makes it an ideal choice for both large-scale production and custom applications.
Future Outlook
As industries continue to prioritize efficiency, sustainability, and reduction in material waste, the future of lost foam casting looks promising. Research and development efforts are focused on enhancing the process through advancements in materials and technologies. These innovations aim to improve the durability of foam patterns and expand the range of metals that can be effectively cast using this technique.
In conclusion, lost foam casting stands out as a transformative process within the foundry industry, offering distinct advantages in terms of design flexibility, production efficiency, and cost-effectiveness. As manufacturers increasingly seek to adopt sustainable and efficient practices, lost foam casting is poised to play a vital role in shaping the future of metal casting and manufacturing as a whole.
Post time:Sep . 04, 2024 03:19
Next:how much does sand casting cost