The Impact of Foundry Sand Contamination on Metal Casting Processes
Foundry sand, primarily composed of silica, plays a crucial role in metal casting processes. Its primary function is to form molds and cores that shape liquid metal into desired products. However, the quality of foundry sand is paramount, as contamination can significantly impact both the casting process and the final product quality. Understanding the sources, effects, and mitigation strategies for foundry sand contamination is essential for foundry operations.
Contamination of foundry sand can arise from various sources during the sand recycling process. Impurities can enter the sand from residual metal, binder materials, or even from the environment. For example, the introduction of organic materials, such as oils or sand stabilizers used in previous castings, can lead to inconsistent mold properties. Additionally, dust, dirt, and other foreign particles can accumulate in the sand during handling and storage, further degrading its quality.
The consequences of contaminated foundry sand can be severe. Firstly, impurities can lead to defects in the final metal product, such as inclusions or surface roughness. These defects not only compromise the structural integrity of the cast items but can also result in increased rejection rates and costly rework. Moreover, contaminated sand can affect the thermal properties of the molds, impacting the cooling rates of the molten metal and leading to dimensional inaccuracies in the finished products.
foundry sand contamination
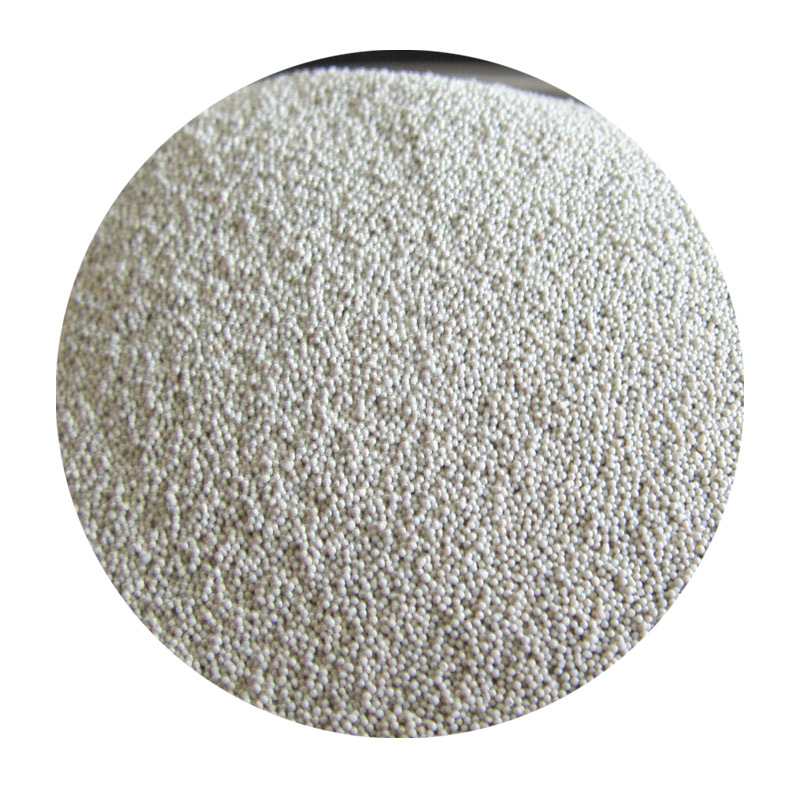
Another critical aspect is the environmental impact. Foundries that do not manage foundry sand contamination effectively risk contributing to pollution and waste. The disposal of contaminated sand can lead to environmental hazards if it leaches harmful substances into the soil or groundwater. Therefore, addressing foundry sand contamination is not only essential for quality control but also for sustainable foundry operations.
Mitigation strategies play a crucial role in minimizing sand contamination. One effective approach is implementing rigorous sand testing protocols before reuse. Regular quality assessments can identify contamination levels and determine the necessity for reclamation or disposal. Furthermore, employing advanced sand reclamation technologies, such as thermal or chemical reclamation, can help remove impurities and restore the sand's original properties.
Training and educating foundry workers on proper handling and storage practices can also reduce the risk of contamination. By ensuring that the sand is stored in clean, covered areas and that all equipment is regularly cleaned, foundries can maintain higher standards of sand quality.
In conclusion, foundry sand contamination poses a significant challenge within the metal casting industry. Its effects can lead to reduced product quality, increased operational costs, and environmental risks. By focusing on prevention, rigorous testing, and effective reclamation strategies, foundries can combat contamination issues, ultimately leading to improved efficiency and sustainability in their casting processes. Emphasizing quality control and environmental responsibility will ensure that foundries remain competitive in an increasingly demanding market.
Post time:Sep . 07, 2024 15:19
Next:Sand Casting Stainless Steel - Precision Manufacturing Solutions