Different Types of Foundry Sand
Foundry sand is a crucial material in the metal casting industry, playing an integral role in ensuring quality and precision in metal parts manufacturing. The choice of sand used in foundries significantly impacts the properties of the final cast product, including surface finish, dimensional accuracy, and mechanical strength. In this article, we will explore the various types of foundry sand, their properties, and applications.
1. Silica Sand
Silica sand, or quartz sand, is the most commonly used foundry sand type. It is made up primarily of silicon dioxide (SiO2) and is known for its excellent thermal properties. Silica sand can withstand high temperatures, making it ideal for the casting process. Its fine particles allow for a smooth surface finish on cast metals, which is crucial in applications requiring precise dimensions. In addition to these attributes, silica sand is readily available and cost-effective, contributing to its popularity in the foundry industry.
2. Olivine Sand
Olivine sand is another significant foundry sand, composed primarily of magnesium iron silicate. It possesses higher melting points than silica sand, making it suitable for casting high-temperature alloys. One of olivine sand's most remarkable features is its resistance to thermal shock and its lower expansion during heating, leading to improved dimensional stability in the casting process. Furthermore, olivine sand is chemically inert, reducing the likelihood of metallurgical defects, which enhances the quality of the final product.
Resin-coated sand is a mixture of sand (often silica) coated with a thermosetting resin. This type of foundry sand boasts superior strength and durability, making it a popular choice for high-precision applications. The resin coating allows for exceptional mold surface finish and enhances the ability to retain details during the casting process. When heated, the resin cures, forming a solid mold that can withstand the casting process's stress. Resin-coated sand is often used for producing complex shapes and thin-walled castings in industries such as automotive and aerospace.
different types of foundry sand
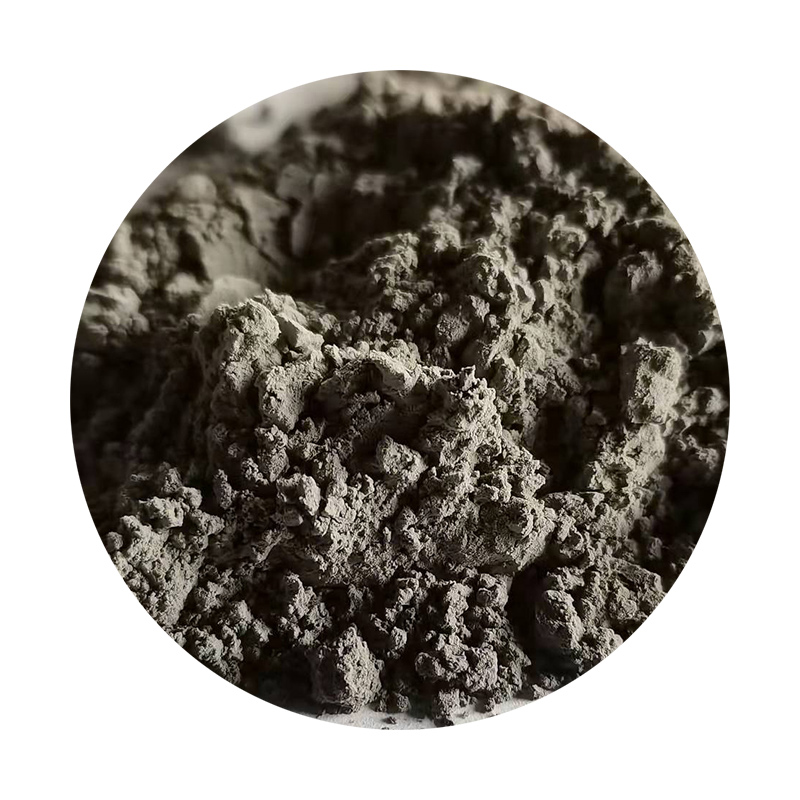
4. Green Sand
Green sand is a mixture of sand, clay (bentonite), water, and various additives. This type of sand is called green not because of its color but due to the moisture content present during molding. Green sand is widely used due to its readily available materials and low cost. It provides excellent moldability and compaction properties, allowing for high-quality castings. However, the presence of moisture can cause potential defects in the casting, making proper control of the moisture content essential.
5. Shell Molding Sand
Shell molding sand utilizes a mixture of fine sand and thermosetting resin, which is applied to heated metal patterns, creating a thin shell mold. This method allows for higher tolerances and improved surface finishes. Shell molding sand is suitable for high-volume production runs and is often used for larger castings in industries like automotive parts manufacturing. The resultant molds are durable and provide enhanced dimensional accuracy, making them ideal for precise applications.
6. Zircon Sand
Zircon sand, composed of zirconium silicate, is known for its high melting point and low thermal expansion. Its unique properties make it suitable for casting high-performance alloys and complex shapes. Zircon sand exhibits excellent resistance to thermal shock and is chemically stable, reducing the risk of defects during the casting process. Although more expensive than other types of foundry sand, zircon sand is used in specialized applications where superior properties are required, such as in aviation and medical components.
Conclusion
The selection of foundry sand is a crucial component in the metal casting process, influencing the quality and precision of the final product. Each type of foundry sand offers distinct advantages based on its composition and physical properties. From common silica sand to specialized materials like zircon and olivine, the diverse options available cater to a wide range of applications across various industries. Understanding the characteristics and benefits of each type of foundry sand enables manufacturers to optimize their casting processes and improve overall product quality. As technology continues to advance, ongoing research and development will likely lead to new compositions and applications, further enhancing the foundry industry's capabilities.
Post time:Dec . 13, 2024 16:54
Next:Innovative Sand Printing Techniques for Enhanced Castings in Manufacturing Processes