Sand for Metal Casting Essential Insights
Sand casting, one of the oldest forms of metal casting, has been a fundamental technique utilized across various industries for centuries. The choice of sand for this process significantly impacts the quality of the finished product. Understanding the properties and characteristics of casting sand is essential for achieving optimal results in metal casting applications.
Types of Sand Used in Metal Casting
The primary type of sand used in metal casting is silica sand, due to its high melting point and availability. Silica sand is composed mainly of silicon dioxide (SiO2) and exhibits excellent thermal stability, making it ideal for casting processes. However, other types of sand can also be used, such as olivine sand, zircon sand, and chromite sand, each offering unique properties that may be beneficial in specific casting situations.
1. Silica Sand This is the most commonly used sand for metal casting. It has good thermal properties and is well-known for its ability to form solid molds. The grain size, shape, and distribution of silica sand can influence the mold's strength and surface finish.
2. Olivine Sand Composed of magnesium iron silicate, olivine sand is prized for its high melting point and low thermal expansion. It is a less common choice but can be effective in applications where high temperatures are prevalent.
3. Zircon Sand Zircon sand has excellent thermal stability and low thermal expansion. It is often used in high-temperature applications and provides a smooth surface finish, making it suitable for intricate designs.
4. Chromite Sand With its high density and thermal conductivity, chromite sand is primarily used in the casting of steel and iron. It is effective in minimizing sand expansion and reduces casting defects.
Properties of Casting Sand
The effectiveness of sand in metal casting is determined by several key properties
sand for metal casting
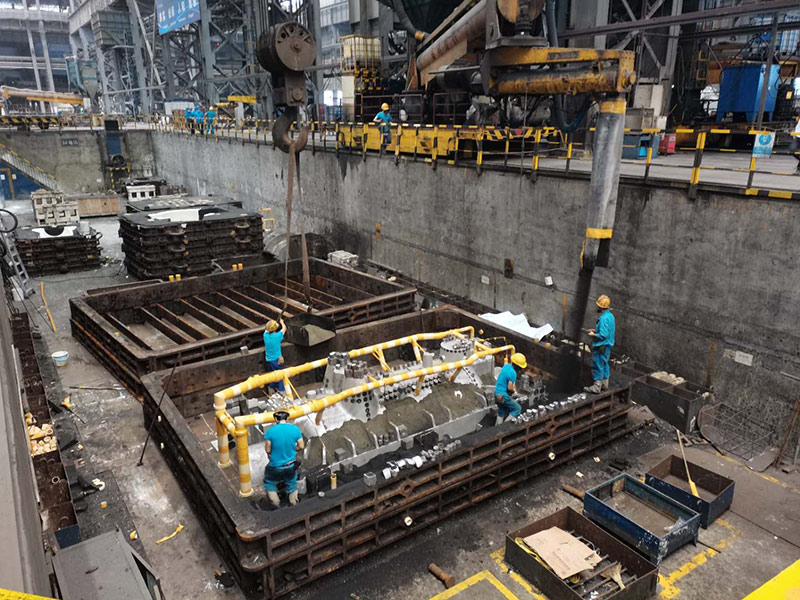
- Grain Size The size of the sand grains affects the permeability of the mold. Coarser sands allow gases to escape more easily, reducing the chance of defects. However, finer sands can produce superior surface finishes.
- Shape and Grain Distribution The shape of the sand grains affects the packing density and flowability. Round grains compact better, while angular grains provide superior strength.
- Moisture Content Water is often added to sand to enhance its plasticity and bonding capabilities. However, the right moisture content is vital; too much moisture can lead to defects, while too little can reduce the mold's strength.
- Binder Materials In many cases, sand needs to be mixed with a binder to enhance its strength and stability. Common binders include clay, resin, and other chemical additives, which help the sand retain its shape during the pouring of metal.
The Role of Sand in Casting Quality
The quality of the sand directly influences the quality of the final casting. Properly selected and treated sand can lead to more precise molds, reducing the risk of defects such as scabs, blowholes, or sand inclusions. Furthermore, high-quality sand can improve the overall surface finish of cast parts, minimizing the need for extensive post-processing.
Environmental Considerations
As the global focus on sustainability and environmentally friendly practices increases, the metal casting industry is seeking alternatives to traditional sand casting processes. Recyclable sand and binders that have less environmental impact are being explored. Moreover, advancements in 3D printing technologies are beginning to change how patterns and molds are created, potentially reducing the amount of sand needed.
Conclusion
In summary, sand is a critical component in the metal casting process, with various types and properties influencing casting quality. Understanding the specific requirements of the casting process and the characteristics of different sands is essential for achieving optimal results. As technology advances and the industry evolves towards more sustainable practices, the role of sand in metal casting will continue to be integral, shaping the future of manufacturing. Through careful selection and management of casting sand, manufacturers can enhance product quality, efficiency, and overall production effectiveness.
Post time:Déc . 16, 2024 09:29
Next:Innovative Applications of Cerabeads Sand in Modern Industries and Environmental Solutions