Advantages of Sand Casting Process
Sand casting, one of the oldest and most widely used metal casting techniques, offers a myriad of advantages that make it a popular choice in the manufacturing industry. This process involves creating a mold from a mixture of sand, clay, and water, which is then used to shape molten metal into the desired form. The versatility, cost-effectiveness, and ease of use associated with sand casting make it a preferred method for both small-scale and large-scale production.
One of the primary advantages of sand casting is its versatility in shaping various types of metals. This process can accommodate a wide range of alloys, including aluminum, iron, bronze, and zinc. This flexibility allows manufacturers to choose the most suitable material for their specific applications, enabling the production of intricate shapes and designs that might be challenging or impossible to achieve with other casting methods.
Advantages of Sand Casting Process
Additionally, sand casting is capable of producing large and complex parts with relative ease. The casting process can accommodate objects of considerable size, making it suitable for industrial applications such as engine blocks, pump casings, and marine components. The sand mold allows for the incorporation of intricate features, such as undercuts and thin walls, without compromising the integrity of the cast. This capability offers manufacturers an edge when seeking unique designs or custom specifications.
advantages of sand casting process
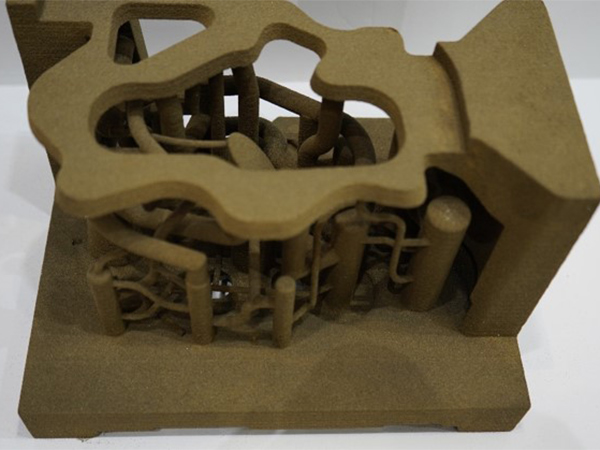
Moreover, sand casting has a relatively quick turnaround time, which is essential in today's competitive market environment. Since the sand molds can be produced rapidly, manufacturers can complete the casting process and deliver products to clients in a shorter timeframe. This quick pace not only meets urgent production schedules but also helps companies stay agile and responsive to customer demands.
Another noteworthy advantage of sand casting is its environmental adaptability. The materials used in the sand casting process, primarily sand and clay, are abundant and inexpensive. Additionally, the sand can often be reused multiple times, making it a sustainable option for manufacturers. Implementing efficient sand recycling processes can further minimize waste, aligning with today's shift towards sustainability in manufacturing practices.
Furthermore, the sand casting process is highly customizable, allowing for adjustments based on the specific requirements of each project. Manufacturers can modify the sand properties, mold designs, and pouring techniques to achieve the desired outcomes. This customization capability supports artistic creativity, enabling the production of not just functional parts but also complex artistic pieces, sculptures, and decorative elements.
Lastly, sand casting is relatively easy to learn and master, which means there is a smaller skill barrier for workers. This accessibility promotes a broader workforce that can be trained to produce high-quality castings without requiring extensive education in advanced manufacturing techniques. Consequently, manufacturers can achieve higher productivity levels and reduced labor costs.
In summary, the sand casting process provides numerous advantages, including versatility in materials, low tooling costs, the ability to produce large and complex parts, quick turnaround times, environmental sustainability, customization possibilities, and ease of training. These benefits make sand casting a viable and attractive option for manufacturers looking to produce high-quality castings while maintaining cost-effectiveness in a rapidly evolving industry. As technology continues to advance, the significance of sand casting is likely to grow, cementing its place in modern manufacturing.
Post time:Oct . 11, 2024 08:35
Next:resin with sand