Exploring the Materials Used in Sand Casting
Sand casting, one of the oldest and most versatile manufacturing processes, involves creating metal components by pouring molten metal into a mold made from sand. The effectiveness and quality of this casting technique are significantly influenced by the materials used, both for the mold and the metal itself.
1. Molding Sand
The primary material in sand casting is molding sand. This sand is specially formulated to withstand high temperatures and provide sufficient support for the molten metal. The most commonly used type of molding sand is silica sand, primarily due to its high melting point and availability. Silica sand consists mainly of silicon dioxide, which offers excellent thermal properties and stability.
To enhance the performance of the molding sand, various additives are included
- Clay Bentonite clay is added to the sand mix as a bonding agent. It gives the sand its strength and helps it retain moisture, which is crucial for holding the shape of the mold. - Water Moisture is essential in sand casting as it activates the clay, allowing it to bond the sand particles together. The typical water content is around 2-5%, depending on the specific requirements of the casting process. - Other Additives Some molds may also include additional materials like coal dust to improve the mold’s collapsibility and sand’s ability to release from the final cast.
In cases where complex internal shapes are required, cores made from the same molding sand are often used. These cores are created using a mixture known as core sand, which may have a higher clay content and is often baked to achieve added strength. Cores allow for the production of internal passages and cavities in the final product.
what materials are used for sand casting
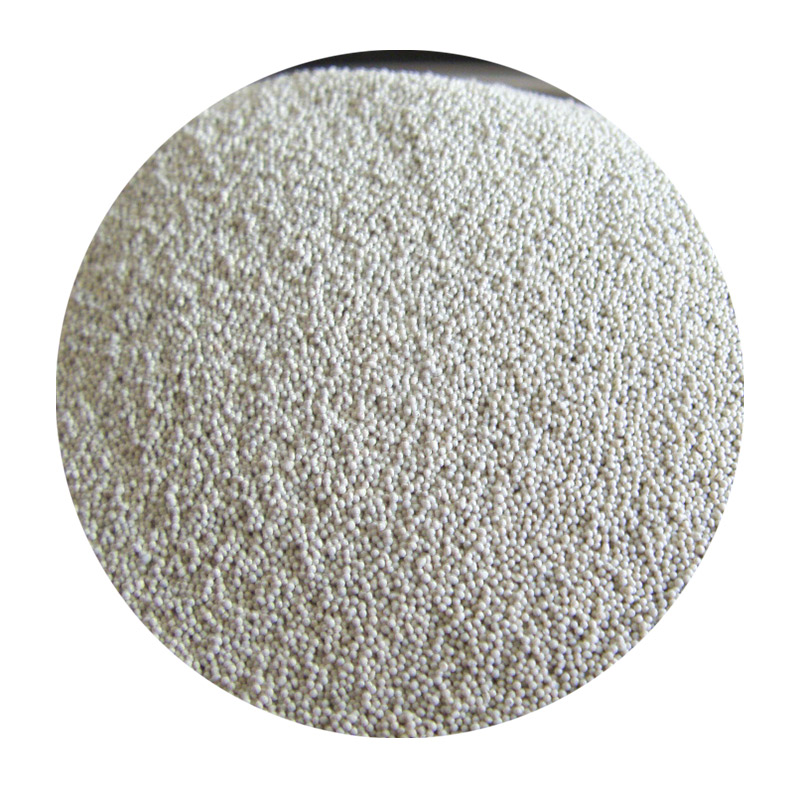
3. Metal Alloys
The choice of metal alloy significantly influences the properties of the final casting. Common metals used in sand casting include
- Aluminum Alloys Lightweight and excellent for corrosion resistance, aluminum alloys are widely used in automotive and aerospace applications. - Iron Alloys Various grades of cast iron, such as gray iron and ductile iron, are popular due to their excellent casting characteristics and mechanical properties. - Steel Alloys Carbon steel and stainless steel are commonly employed for their strength and versatility in various industrial applications.
4. Additional Materials
In addition to the primary materials, other components may be used to enhance the casting process. Parting agents are often applied to the mold surfaces to facilitate the easy release of the cast part. These agents can be powders, oils, or other materials designed to create a barrier between the mold and the casting.
Conclusion
The materials used in sand casting play a crucial role in determining both the quality and efficiency of the casting process. From molding sand and additives to metal alloys and core materials, each element must be carefully selected based on the specific requirements of the casting application. As industries continue to evolve, innovations in sand casting materials will likely enhance the capabilities and applications of this traditional yet indispensable manufacturing method.
Post time:loka . 16, 2024 04:23
Next:Understanding the Role of Sand in Investment Casting Processes and Techniques