Types of Sand Casting
Sand casting is one of the oldest and most widely used metal casting processes. It involves creating a mold from a sand mixture, where molten metal is poured to take the shape of the desired product. This technique is appreciated for its versatility and adaptability, making it suitable for various applications, from small-scale crafts to large industrial parts. Among the various methods of sand casting, several distinct types have emerged, each with its unique characteristics, advantages, and applications.
1. Green Sand Casting
Green sand casting is the most common type of sand casting process. It utilizes a mixture of sand, clay, and water, referred to as green sand because it is not baked or dried. The sand's moisture content allows it to maintain its shape and provide sufficient adhesion. This method is highly cost-effective and is suitable for producing various metal castings. It is particularly useful in producing intricate shapes and sizes, making it a favorite in industries such as automotive and general manufacturing. However, green sand molds require additional processing and finishing due to their porous nature.
2
. Dry Sand CastingAs the name suggests, dry sand casting uses sand that is dried in an oven prior to mold preparation. This process leads to a more durable and stable mold, allowing for excellent surface finish and dimensional accuracy. Dry sand casting is often employed for high-quality castings where intricate designs are required. Although it costs more than green sand casting, the increased mold strength and better surface quality can justify the expense in applications like aerospace components and complex machinery parts.
3. Sodium Silicate Sand Casting
types of sand casting
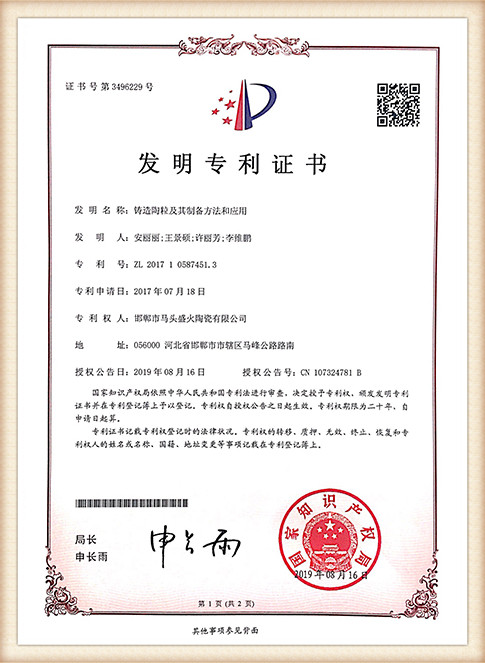
In sodium silicate sand casting, sodium silicate (water glass) is used as a binder in place of clay. This type of sand casting allows for rapid mold production, as the molds are cured with carbon dioxide, leading to a hard and strong structure. This method offers improved dimensional stability and a finer surface finish compared to green sand casting. Sodium silicate sand casting is suitable for production runs where high accuracy and surface quality are critical, often utilized in industrial machines and equipment.
4. Shell Molding
Shell molding is a variant of sand casting that involves creating a thin shell of sand and resin around a pattern. This method yields high-quality castings with excellent dimensional accuracy and surface finish. Shell molds can be made quickly and reused multiple times, making them a more efficient option for larger production runs. Although this process involves higher tooling and material costs, the benefits in finish and precision make it a go-to option in high-performance applications, such as in the automotive and aerospace sectors.
5. Lost Foam Casting
Lost foam casting is a unique method that involves creating a foam pattern coated in a thin layer of sand. The foam pattern evaporates when molten metal is poured into the mold, leaving behind a cavity that replicates the original design. This process allows for complex shapes without the need for a traditional mold, reducing machining and finishing requirements. Lost foam casting is increasingly popular in producing automotive parts and other components where intricate designs are essential.
In conclusion, sand casting encompasses a variety of techniques that cater to a wide range of industries and applications. Each type possesses distinct advantages and challenges, allowing manufacturers to choose the most suitable method based on their specific requirements. Whether for mass production or specialized, high-precision parts, sand casting remains an integral part of the metalworking landscape.
Post time:elo . 31, 2024 19:25
Next:colata in sabbia aperta