Understanding Sand Cast Iron Composition, Process, and Applications
Sand cast iron, an integral material in various industrial applications, is known for its unique properties and versatility. This type of iron is produced through sand casting, a process that involves pouring molten metal into a sand mold to achieve the desired shape and properties. This article will explore the composition, advantages, manufacturing process, and applications of sand cast iron.
Composition of Sand Cast Iron
Sand cast iron primarily consists of iron, carbon, and silicon, with varying amounts of other elements such as manganese, phosphorus, and sulfur. The carbon content typically ranges between 2% and 4%, contributing to the iron's hardness and strength. Silicon is also significant as it enhances fluidity during the melting process and helps in forming a protective oxide layer, which reduces oxidation.
There are different types of cast iron, including gray iron, ductile iron, and white iron, each with its unique properties based on the microstructure and chemical composition. Gray iron, characterized by its high machinability and excellent wear resistance, is the most commonly produced form of sand cast iron. The graphite flakes in gray iron help to absorb vibrations, making it an ideal choice for creating engine blocks, machine bodies, and frames.
The Sand Casting Process
The sand casting process involves several key steps, all of which contribute to the final product’s quality and properties. The first step is pattern making, where a model of the desired object is created, usually from wood, metal, or plastic. This pattern is then used to form a mold in the sand. The mold is created by mixing sand with a binder, such as clay or resin, which helps the sand maintain its shape.
Once the mold is prepared, it is filled with molten iron, which is heated to a temperature of about 1,200 to 1,400 degrees Celsius. The molten iron is poured into the mold where it cools and solidifies, taking the shape of the interior cavity. After sufficient cooling, the sand mold is broken away to reveal the cast iron part. Final finishing processes, such as grinding and machining, are typically performed to meet specific tolerances and surface finish requirements.
sand cast iron
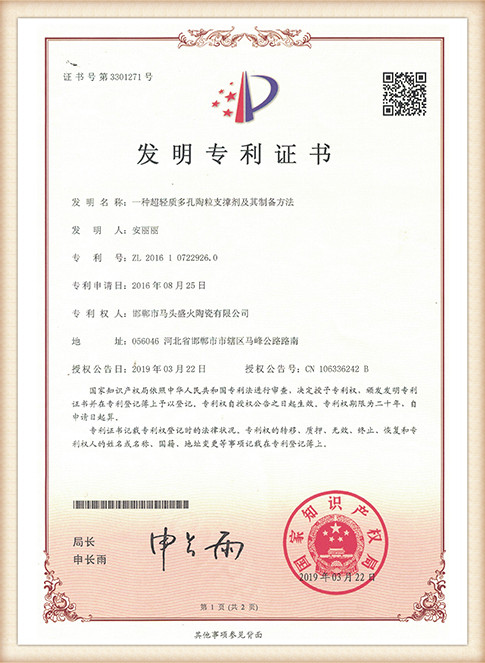
Advantages of Sand Cast Iron
One of the primary benefits of sand cast iron is its excellent castability, allowing complex shapes and designs to be easily achieved. The sand casting process accommodates large-scale production, making it a cost-effective option for manufacturers. Moreover, sand cast iron possesses superior wear resistance, machinability, and vibration-damping abilities, making it suitable for mechanical applications.
Another advantage is the ability to recycle. The sand used in the casting process can be reused multiple times, reducing manufacturing waste and contributing to a more sustainable production process. Additionally, the strength-to-weight ratio of sand cast iron makes it an attractive option for high-load applications while keeping overall material costs manageable.
Applications of Sand Cast Iron
The versatility of sand cast iron means that it finds applications across various industries. In automotive manufacturing, cast iron components are commonly used in engine blocks, cylinder heads, and exhaust manifolds. The robust nature of sand cast iron ensures durability and longevity in these critical engine components.
In the construction and infrastructure sectors, sand cast iron is utilized for making pipes, manhole covers, and structural components. Its resistance to corrosion and wear makes it a reliable choice for underground and outdoor applications. Other industries such as agriculture, machinery, and tools also benefit from sand cast iron's properties, using it for equipment parts, tools, and agricultural machinery.
Conclusion
Sand cast iron is a highly versatile material with a wide range of applications in various industries due to its excellent properties such as castability, strength, and durability. Understanding its composition and the intricacies of the sand casting process can help industries leverage its benefits more effectively. As technology advances, the future of sand cast iron looks promising, continuing to be a preferred material for engineers and manufacturers alike.
Post time:marras . 12, 2024 10:57
Next:fill 3d print with sand