Materials Used for Sand Casting
Sand casting is one of the oldest and most versatile methods of metal casting. It involves creating a mold from sand and then pouring molten metal into this mold to achieve the desired shape of a metal object. The success and efficiency of sand casting depend significantly on the materials employed in both the mold-making and the casting process. This article explores the key materials used in sand casting and their respective roles.
1. Sand
The primary material used in sand casting is, unsurprisingly, sand. The most commonly used type is silica sand, which is composed mainly of quartz. Its high melting point and excellent flowability make it ideal for high-temperature metal casting. The grain size and shape of the sand are crucial; finer sands provide a smoother surface finish on the cast part, while coarser grains are more robust and better at holding the shape of the mold.
Additionally, not all sand is created equal. Different types of sand are used depending on the specific requirements of the casting process. For instance, green sand, which is a mixture of silica sand, clay, and water, is widely used because of its effective binding properties and ability to retain moisture. On the other hand, silica sand mixed with resin forms a strong mold and is used in more advanced sand casting processes, such as no-bake or shell molding.
2. Bindings
Binders are critical in ensuring that the sand maintains its shape when packed into the mold. Clay is the most traditional binder used in sand casting, particularly in green sand molds. Bentonite clay is commonly employed due to its excellent binding properties and ability to retain moisture, which is essential for mold stability.
In more modern applications, chemical binders such as phenolic-urethane or furan resins are often utilized. These binders enable the creation of stronger and more precise molds, which can withstand higher temperatures and more complex shapes. The choice of binder often depends on the specific requirements of the metal being cast and the intricacies of the desired final product.
3. Metal Alloys
materials used for sand casting
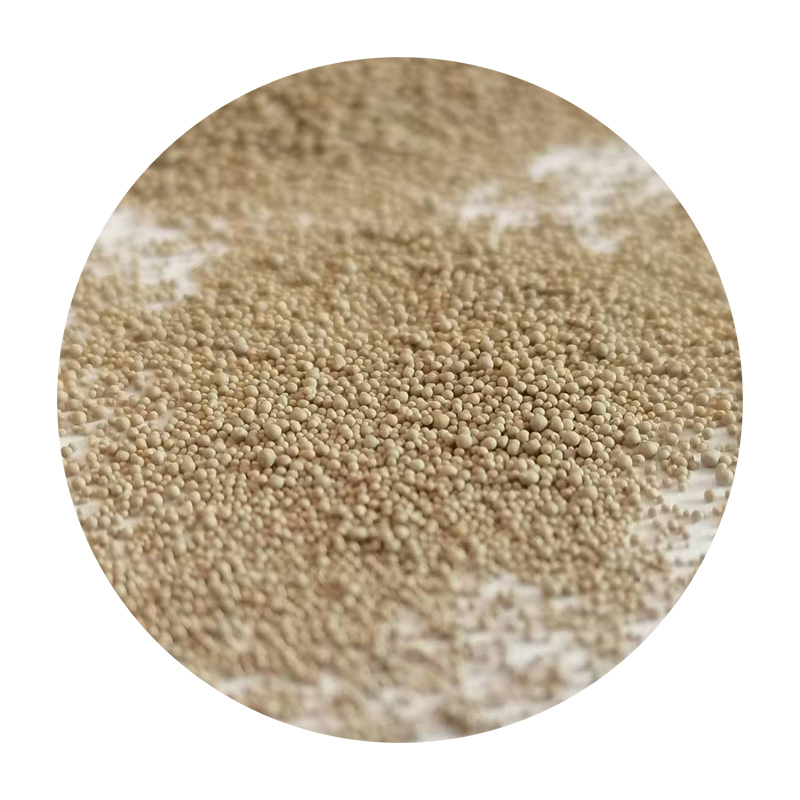
The metal material poured into sand molds can vary widely depending on the application. Commonly used metal alloys in sand casting include aluminum, iron, bronze, and brass. Each metal has its own properties that affect the casting process and the final product.
For instance, aluminum alloys are favored for their lightweight and corrosion-resistant properties, making them popular in automotive and aerospace industries. Cast iron, on the other hand, is known for its durability and wear resistance, often utilized in heavy machinery and automotive components.
4. Additives
Various additives are sometimes incorporated into the sand mixture to enhance its properties. These can include materials like coal dust, which helps improve casting surface quality, and various additives that enhance the thermal properties of the sand. Some manufacturers also use lubricants to reduce friction between the sand and the molten metal, facilitating easier molding and releasing of the finished product.
5. Core Materials
When certain geometries require internal cavities, cores made from sand are used. Core materials can include sand mixed with resin or other binders to provide strength and stability. Cores are crucial for achieving complex shapes and delivering the precise internal features desired in a cast part.
Conclusion
In summary, sand casting is a sophisticated process that relies significantly on its materials. Sand, binders, metal alloys, and additives all play critical roles in determining the efficiency, quality, and precision of the castings produced. As technology advances, the selection of materials continues to evolve, enabling more refined and complex manufacturing capabilities. Understanding the properties and functions of these materials is essential for anyone involved in the casting industry, ensuring optimal results in the production of metal components. Sand casting remains a favorite method due to its adaptability and ability to produce a wide range of shapes and sizes.
Post time:syys . 28, 2024 00:05
Next:The Historical Invention Timeline of Sand Casting Techniques