The Importance of Making Foundry Sand A Comprehensive Overview
Foundry sand is a crucial component in the metal casting industry, where it plays a vital role in producing intricate metal parts for various applications, ranging from automotive to aerospace. The process of making foundry sand involves several steps that ensure the final product meets the demanding specifications required for efficient casting processes. Understanding the composition, manufacturing, and applications of foundry sand can provide valuable insights into its significance in modern manufacturing.
Composition and Properties
Foundry sand is primarily composed of silica sand, which is favored for its unique properties such as high fusion point, stability, and thermal conductivity. The grains are typically rounded, allowing for better flowability and compaction, which facilitates superior mold formations. In addition to silica, foundry sand can contain other materials, including clay and various additives that enhance its binding properties. The ideal foundry sand must possess the right balance of permeability, strength, and reusability, making it essential for casting intricate shapes without defects.
Manufacturing Process
The manufacturing of foundry sand involves several key stages
1. Extraction Silica sand is sourced from natural deposits, often found in riverbeds, lakes, and dunes. The quality of the sand is critical; impurities can affect the casting process and the quality of the final product.
2. Processing Once extracted, the sand undergoes a series of cleaning and processing steps. This may involve washing to remove impurities and ensure uniform grain size. Screening is also essential to separate fine particles from coarser grains, ultimately leading to the creation of a consistent sand product.
3. Additive Mixing Depending on the specific casting requirements, additives such as clay are mixed with the sand to enhance its properties. For instance, bentonite clay is commonly used to improve mold strength and compaction.
making foundry sand
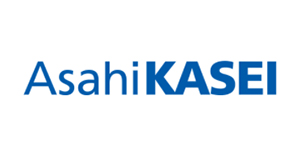
4. Testing Quality control is vital in the foundry sand manufacturing process. The sand is subjected to various tests that measure its moisture content, grain size distribution, and permeability. Ensuring these properties meet industry standards is crucial for successful metal casting.
5. Reclamation After a casting job is completed, foundry sand can often be reclaimed and reused. The reclamation process involves removing impurities from the spent sand, ensuring that it can be reintroduced into the production cycle without compromising quality. This not only reduces waste but also lowers operational costs for foundries.
Applications
The uses of foundry sand are vast and varied. In the automotive industry, foundry sand is used to produce engine blocks, cylinder heads, and other critical components. The aerospace sector also relies heavily on foundry sand for casting complex engine parts, showcasing its importance in high-performance applications.
Moreover, foundry sand's ability to capture fine details makes it ideal for artistic applications, such as sculptures and decorative pieces. The versatility of foundry sand allows it to meet the needs of diverse industries, making it a foundational material in modern manufacturing.
Environmental Considerations
As industries strive for sustainability, the foundry sand sector is also taking steps toward environmentally friendly practices. Emphasizing the reclamation and reuse of sand not only conserves natural resources but also reduces the environmental footprint of foundry operations. Furthermore, ongoing research into alternative materials and processes seeks to minimize the environmental impact associated with foundry sand production and use.
Conclusion
In summary, foundry sand is a vital material in the metal casting industry, supporting numerous sectors through its unique properties and versatile applications. The meticulous process of making foundry sand, from extraction to reclamation, underscores its significance in manufacturing. As the industry evolves, the focus on sustainability and quality will ensure that foundry sand continues to be a cornerstone of innovative metal casting practices for years to come.
Post time:marras . 12, 2024 05:09
Next:resin coated silica sand