Lost Foam Casting Coating An Overview
Lost foam casting is an innovative casting process that has gained popularity in various manufacturing industries due to its ability to produce complex shapes and achieve high precision. This method relies on the use of foam patterns that are coated and subsequently melted away during the casting process. A critical aspect of this technique is the coating applied to the foam patterns, which plays a vital role in the overall success of the lost foam casting process.
The Importance of Coating in Lost Foam Casting
The coating serves multiple purposes in lost foam casting. First and foremost, it provides a robust barrier that protects the foam pattern from molten metal, ensuring that the final product maintains its desired shape and dimensional accuracy. The coating also assists in creating a smooth surface finish on the cast object, which is essential in industries where aesthetics and precision are critical, such as in automotive or aerospace manufacturing.
Types of Coatings
Several types of coatings are used in lost foam casting, each chosen based on the specific requirements of the application. Common materials for coatings include
1. Sands and Binders Traditionally, a mixture of fine sand and a binding agent is used to create a durable coating around the foam pattern. This method is favored for its simplicity and effectiveness.
2. Inorganic Coatings These coatings are made from materials such as ceramics or silicates. They offer excellent thermal resistance and are particularly beneficial when casting alloys with high melting points.
3. Organic Coatings Often based on phenolic resins, organic coatings provide good adhesion and can deliver a fine finish. However, they may not withstand high temperatures as effectively as their inorganic counterparts.
4. Composite Coatings These are advanced coatings that combine both organic and inorganic materials to optimize the performance characteristics, including thermal stability and surface finish quality.
Application Process
The application of the coating onto the foam pattern is a crucial step in the lost foam casting process. The coating can be applied through several methods
lost foam casting coating
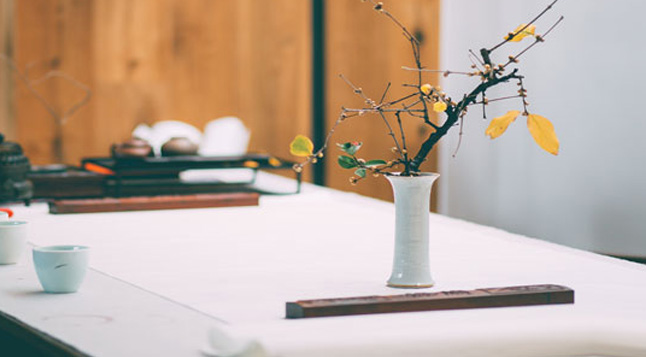
- Spraying An efficient way to achieve an even coating, this method allows for quick application over complex shapes. - Dipping Involves immersing the foam pattern into a coating mixture, ensuring complete coverage. This method is particularly useful for larger patterns.
- Brushing For intricate patterns, manual application via brush ensures that hard-to-reach areas are adequately coated.
Regardless of the method used, it is essential to ensure that the coating is applied evenly to prevent defects such as uneven surfaces or incomplete melting of the foam during casting.
Drying and Hardening
After the application, the coating must be properly dried and hardened to withstand the rigors of molten metal pouring. This can involve air drying or using an oven, depending on the type of coating material and the desired properties. The integrity of the coating post-drying is paramount; any cracks or defects can compromise the casting process, leading to potential failures.
Advantages of Using Coatings in Lost Foam Casting
The use of coatings in lost foam casting offers several advantages
- Enhanced Surface Finish Coatings contribute to smoother surfaces, reducing the need for extensive post-casting machining.
- Improved Dimensional Tolerance A well-applied coating can help maintain the dimensional accuracy that is often required in engineering applications.
- Broader Material Compatibility The versatility of different coating materials allows for casting a wide range of metals, including high-temperature alloys.
Conclusion
In the realm of manufacturing, lost foam casting stands out as a process that combines efficiency with versatility. The coating applied to foam patterns is a fundamental component that influences the quality and properties of the final cast product. With advancements in coating materials and application techniques, the lost foam casting process continues to evolve, meeting the demands of modern industry and enabling the production of intricate and high-quality parts. The future of lost foam casting looks promising, with ongoing research and development likely to yield even more innovative solutions.
Post time:marras . 08, 2024 10:30
Next:The Evolution of Sand Casting Techniques Through History and Their Modern Applications