Hard Sand Casting An Overview of the Process and Benefits
Hard sand casting, also known as green sand casting, is a widely used manufacturing process in which metal parts are created by pouring molten metal into a sand mold. This technique has been utilized for centuries and continues to be a cornerstone in the production of complex metal components. The appeal of hard sand casting lies in its ability to produce intricate shapes with excellent dimensional accuracy and surface finish.
The process begins with the preparation of the sand mixture, which typically consists of silica sand, clay, water, and various additives. The term hard sand refers to a specific type of sand that, when mixed with clay, forms a strong mold capable of withstanding the pressures of molten metal. The clay acts as a binding agent, allowing the sand particles to stick together, creating a stable structure. The water content is carefully controlled to ensure the mold is firm yet still easy to work with.
Once the sand mixture is prepared, the next step involves creating the mold. This can be done using patterns made of metal, wood, or other materials. The pattern is pressed into the sand mixture to create a cavity in the shape of the desired part. After the pattern is removed, the two halves of the mold are assembled, and any additional features needed for the casting process, such as runners and risers, are added. These components help guide the molten metal into the mold and allow for the escape of gases during pouring.
hard sand casting
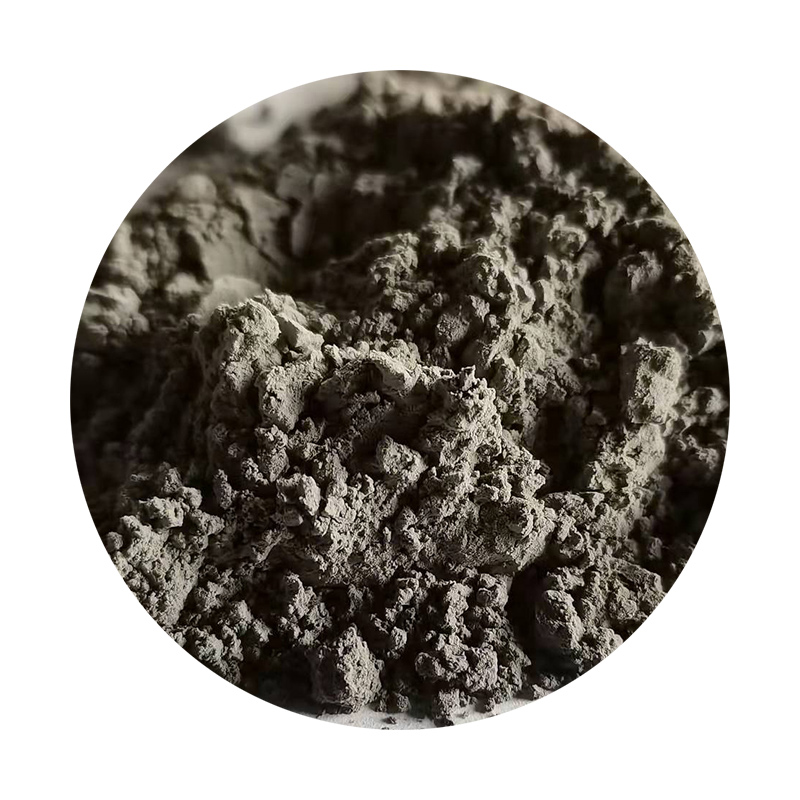
The actual casting process begins with heating the metal in a furnace until it reaches its molten state. Common metals used in hard sand casting include aluminum, iron, and bronze. Once the metal is fully molten, it is poured into the mold cavity, where it fills the space and takes on the shape of the pattern. The cooling process begins, and as the metal solidifies, it forms the final part. After sufficient cooling time, the mold is broken away, revealing the casted piece.
One of the primary advantages of hard sand casting is its cost-effectiveness, especially for large production runs. The materials used are relatively inexpensive, and the flexibility of the process allows for the production of various shapes and sizes without significant modifications. Additionally, hard sand casting can accommodate large parts that may be difficult or impossible to create using other methods.
Another benefit of this casting technique is its ability to produce components with excellent mechanical properties. The resulting parts often exhibit high strength and durability, making them suitable for various applications, from automotive to aerospace industries. Furthermore, because the process can be adapted for both ferrous and non-ferrous metals, it opens the door to a diverse range of products.
In conclusion, hard sand casting remains an essential manufacturing process, valued for its adaptability, efficiency, and cost-effectiveness. As technology advances, new techniques and materials continue to enhance the capabilities of hard sand casting, ensuring its relevance in modern manufacturing for years to come. Whether for high-volume production or intricate custom components, hard sand casting is a reliable choice for metal fabrication.
Post time:marras . 25, 2024 13:43
Next:lost-foam casting