Understanding Hard Sand Casting A Comprehensive Overview
Hard sand casting, also known as no-bake sand casting, is a metal casting process that uses a mixture of sand, resin, and a hardening agent to produce molds and cores. This technique is a vital component of modern manufacturing, particularly in industries such as automotive, aerospace, and heavy machinery, where precision and durability are paramount. The unique properties and advantages of hard sand casting make it a popular choice among manufacturers seeking high-quality components.
The Casting Process
The hard sand casting process begins with the preparation of a sand mixture. The primary component is silica sand, which provides the fundamental shape and thermal properties required for casting. This sand is then mixed with a resin binder, which can be activated by heat or a chemical catalyst to form a strong bond once cured. The resulting material allows for the production of intricate and precise molds that can withstand the pressures of molten metal.
Once the sand mixture is prepared, it is packed into a mold box around a pattern, which is often made of metal or plastic and represents the final shape of the part to be cast. The key advantage of this method is the ability to create complex geometries without the need for extensive tooling. After the mold is formed, the next step involves curing the sand, which reinforces its structure. This can be achieved through various processes, including heat treatment or chemical hardening.
After the mold is cured, it is opened, and any cores that were needed for internal structures are placed inside. The mold is then closed, and molten metal is poured into the cavity. Once the metal cools and solidifies, the mold is broken away to reveal the finished casting. This process allows for an impressive degree of detail and finishing in the final product, paving the way for further machining as required.
Benefits of Hard Sand Casting
One of the primary advantages of hard sand casting is its flexibility. The process allows for customization and rapid production, making it ideal for short-run manufacturing and prototyping. It is particularly useful for producing large components that would be challenging to create with other methods, such as die casting or investment casting.
hard sand casting
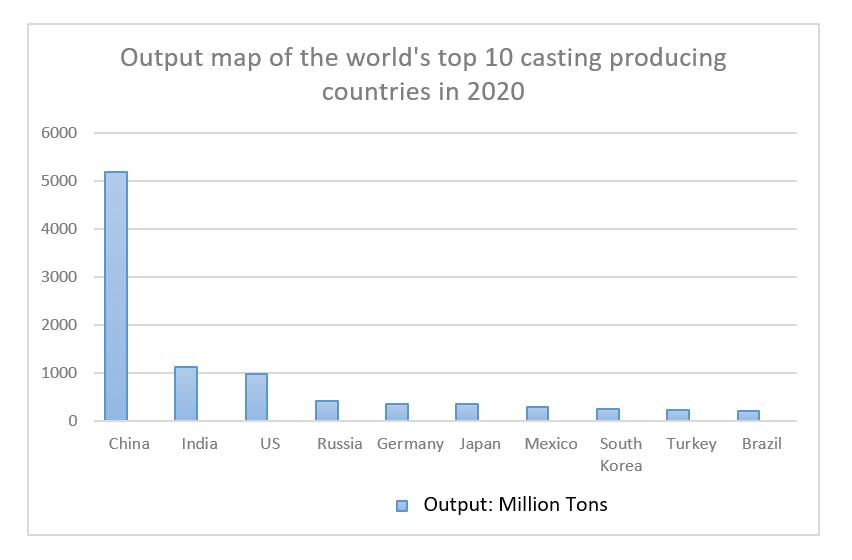
Additionally, the hard sand casting process can accommodate a wide variety of metals, including aluminum, brass, bronze, and various steel alloys. This versatility enables manufacturers to choose the material that best suits their application while ensuring robust mechanical properties.
Cost-effectiveness is another significant advantage of hard sand casting. The process generally requires less expensive tooling compared to other casting methods. This cost reduction is particularly advantageous for small to medium-sized enterprises looking to minimize their initial investment while still producing high-quality castings.
Applications in Industry
The applications of hard sand casting are extensive and span multiple sectors. In the automotive industry, it is commonly used to create engine blocks, transmission cases, and other critical components that require high strength and durability. Aerospace manufacturers utilize hard sand casting for intricate parts such as turbine housings and brackets, where precision is essential given the demanding conditions these components must endure.
Moreover, industries involved in heavy machinery and construction rely on hard sand casting to produce parts such as gears, housings, and structural components. The ability to produce large and complex shapes efficiently allows these industries to maintain operational excellence and meet rigorous safety standards.
Conclusion
Hard sand casting remains a cornerstone of modern manufacturing, thanks to its unique advantages and wide-ranging applications. By leveraging a combination of silica sand and resin binders, manufacturers have the flexibility to create high-quality components with intricate designs, making it an invaluable technique in today's competitive industrial landscape. As technology continues to advance, the hard sand casting process will likely evolve further, leading to even greater efficiencies and capabilities in metal casting. Whether for large-scale production or specialized components, hard sand casting is poised to play a pivotal role in the future of manufacturing.
Post time:marras . 14, 2024 22:11
Next:3d printing patterns for sand casting