Understanding Foundry Sand Properties
Foundry sand plays a crucial role in the metal casting process, providing the necessary mold for shaping metal and ensuring the production of high-quality castings. This article explores the properties of foundry sand, its types, and its significance in the foundry industry.
Types of Foundry Sand
The most commonly used type of foundry sand is silica sand, primarily due to its availability, cost-effectiveness, and desirable properties. Other types of foundry sands include olivine sand, zircon sand, and resin-coated sand. Each type has unique characteristics that make it suitable for specific applications.
- Silica Sand Silica sand is the most prevalent foundry sand, composed mostly of quartz grains. Its high melting point, excellent thermal stability, and good flowability make it an ideal choice for various casting processes.
- Olivine Sand Composed of magnesium iron silicate, olivine sand offers high thermal stability, low thermal expansion, and excellent green strength, making it suitable for high-temperature applications. Its resistance to chemical reactions with molten metals also makes it a preferred choice in certain casting situations.
- Zircon Sand Known for its high resistance to thermal expansion and abrasion, zircon sand is often used in casting applications requiring precision. Its unique properties help in producing intricate and complex patterns, making it ideal for investment casting.
- Resin-Coated Sand This type of sand is coated with a thermosetting resin and is known for its excellent strength and resistance to thermal shock. Resin-coated sand allows for complex shapes and finer details in castings, making it favored in the production of high-precision components.
Key Properties of Foundry Sand
foundry sand properties
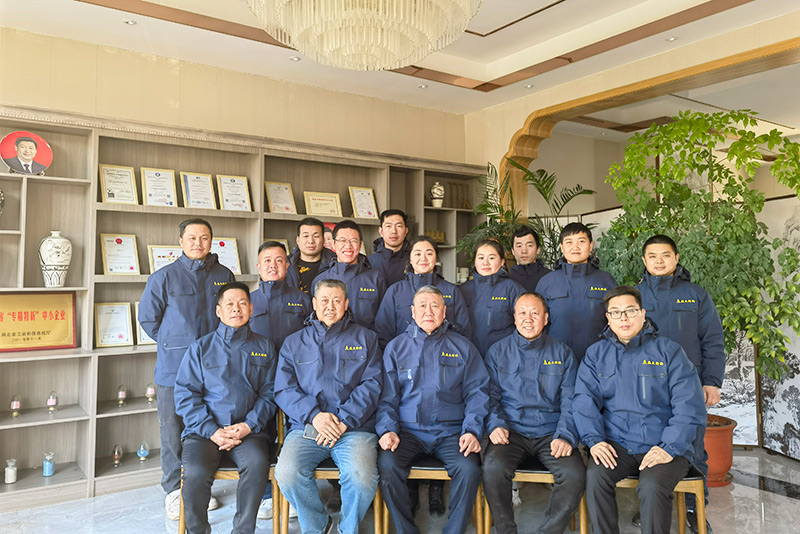
The effectiveness of foundry sand in the casting process relies on several key properties
1. Grain Shape and Size The shape and size of sand grains significantly influence the mold's permeability and strength. Generally, well-graded sands with a mix of different grain sizes provide optimal packing density, resulting in better mold integrity.
2. Thermal Conductivity Foundry sand must have good thermal conductivity to dissipate heat efficiently from the molten metal. This property helps to minimize casting defects such as warping and ensures a smoother cooling process.
3. Permeability The ability of the sand mold to allow gases to escape is critical. High permeability prevents gas entrapment during the pouring of molten metal, reducing the chances of defects such as blowholes and poor surface finish.
4. Chemical Stability Foundry sand must be chemically stable and resistant to reactions with molten metals. Any reaction can produce gases or slag that adversely affect the quality of the casting.
5. Reusability The ability to reclaim and reuse foundry sand is an environmentally friendly aspect of modern foundry practices. Sand reclamation technologies enable the reuse of sand while maintaining its physical properties, thus reducing waste and operational costs.
Importance in the Foundry Industry
The selection of appropriate foundry sand is vital for achieving optimal casting results. High-quality sand contributes to better mold strength, improved surface finish, and reduced rates of defects, leading to enhanced productivity and lower operational costs. Additionally, as the foundry industry moves towards sustainable practices, the development of sustainable foundry sands is gaining traction, focusing on recycling and reducing the environmental impact.
In conclusion, foundry sand properties are integral to the metal casting process. Understanding the various types of sand, their characteristics, and their implications for casting performance is crucial for foundry operators and manufacturers. As technology advances, further innovations in foundry sand processes and materials are likely to emerge, fostering improvement in casting quality and overall production efficiency.
Post time:loka . 11, 2024 09:36
Next:resin coated sand manufacturers