Understanding Foundry Sand Composition
Foundry sand plays a critical role in the metal casting industry, serving as a mold material that allows for the precise shaping of metal components. The composition of foundry sand is essential not only in determining the physical properties of the molds but also in influencing the overall quality of the cast products. This article aims to delve into the typical composition of foundry sand, its types, and its significance.
Types of Foundry Sand
The primary types of foundry sand used in metal casting include silica sand, olivine sand, and clay-based sands. Each type has unique properties, making them suitable for different casting applications.
1. Silica Sand The most common type, silica sand is composed mostly of silicon dioxide (SiO2). Silica grains are typically hard, chemically inert, and provide excellent thermal stability. It is widely used for both ferrous and non-ferrous casting processes. However, workers must handle silica sand with care due to the risk of silica dust inhalation, which can lead to respiratory issues.
2. Olivine Sand This type of sand is composed of magnesium iron silicate and is known for its superior thermal stability and resistance to metal penetration. Olivine sand reduces the number of defects in castings and is environmental-friendly as it does not produce harmful fumes when heated. Though more expensive than silica sand, its performance in high-temperature applications justifies the cost.
3. Clay-Based Sands (Green Sand) Clay sands contain clay as a bonding agent, which gives them moldability and strength. Typically, this mixture includes silica sand, clay, and moisture. The combination allows for good detail reproduction in castings. Green sand is recyclable, which adds to its economic appeal.
Key Components of Foundry Sand
The performance of foundry sand significantly hinges on its various compositional components
- Silicon Dioxide (SiO2) This is the primary ingredient in most foundry sands, and its purity level can greatly affect the mold's thermal and mechanical properties. High-purity silica sands improve casting quality by reducing the occurrence of defects such as sand burn-on and gas porosity.
foundry sand composition
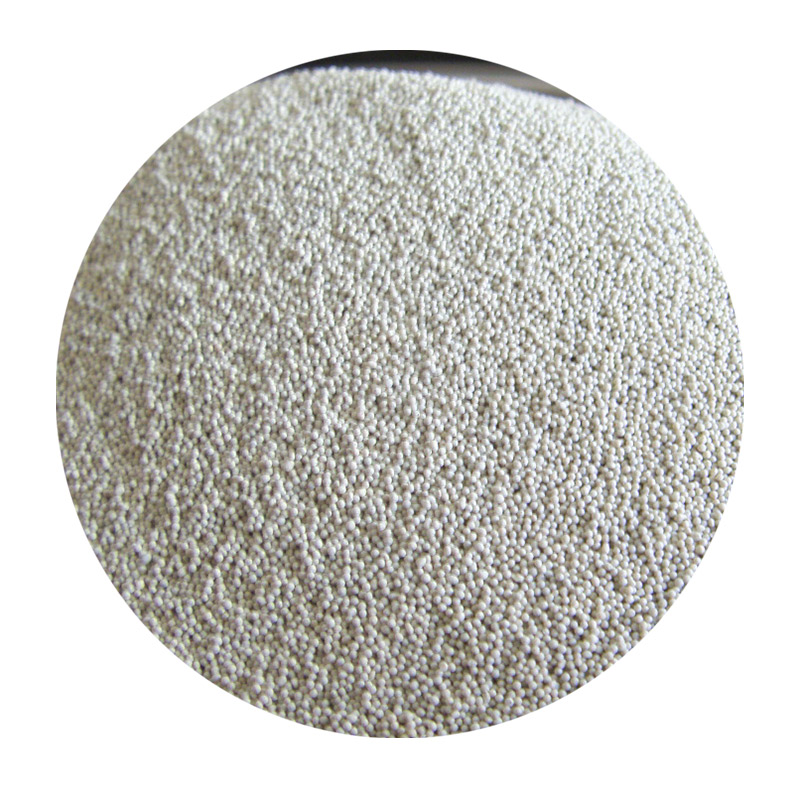
- Clay Content When utilized in green sand molding, the type and amount of clay play a pivotal role. Clay materials enhance the mold’s strength and improve its ability to hold its shape under the pressure of molten metal. Common clay types include bentonite, which possesses excellent binding properties.
- Additives Various additives can be integrated into foundry sands to enhance certain properties. For example, sodium silicate is often used as a binder to provide additional strength. Other additives may include coal dust, which helps to minimize gas defects during the casting process.
Importance of Foundry Sand Composition
The composition of foundry sand directly influences multiple factors essential to the metal casting process, including
- Mold Strength The right balance of clay and sand supports the mold's integrity, allowing it to withstand the forces exerted by molten metal.
- Thermal Conductivity The materials in foundry sand impact how heat is transferred within the mold, which is crucial for preventing thermal shocks that could lead to cracking.
- Recyclability An ideal foundry sand composition not only fulfills casting requirements but also allows for easy recycling, which reduces waste and conserves resources.
Conclusion
The composition of foundry sand is a vital aspect of the metal casting industry that contributes to the production of high-quality cast components. By understanding the types of foundry sand and their essential components, foundry operators can make informed decisions that enhance mold quality and overall process efficiency. Whether choosing silica, olivine, or clay-based sands, the goal remains the same to achieve optimal castings with the least amount of defects, thereby ensuring successful and sustainable manufacturing outcomes.
Post time:marras . 07, 2024 06:00
Next:Understanding the Role of Sand in the Sand Casting Process and Its Benefits