Custom Sand Casting A Comprehensive Guide
Custom sand casting is a versatile and widely used manufacturing process that involves creating metal components by pouring molten metal into a mold made of sand. This method has been extensively utilized across various industries due to its cost-effectiveness, flexibility, and ability to produce complex shapes. In this article, we will explore the intricacies of custom sand casting, its advantages, applications, and the steps involved in the process.
Understanding the Process
The custom sand casting process begins with creating a mold. This is typically done using a pattern, which is a replica of the desired final product. Patterns can be made from various materials, such as wood, metal, or plastic, depending on the application and production volume. The pattern is placed in a sand mixture, which contains fine sand, a binding agent, and water, to form a mold around it. Once the mold is created, the pattern is removed, leaving a hollow cavity that matches the shape of the desired component.
Next, molten metal is poured into the mold cavity. The type of metal used can vary, including aluminum, iron, bronze, or steel, depending on the required properties of the final product. Once the metal cools and solidifies, the sand mold is broken away, revealing the cast component. This can then undergo various finishing processes, such as grinding or machining, to achieve the required dimensions and surface finish.
Advantages of Custom Sand Casting
1. Cost-Effectiveness Custom sand casting is particularly advantageous for small to medium production runs, as it allows for lower setup costs compared to other metalworking processes. The materials used for the mold are relatively inexpensive, making it an attractive option for many manufacturers.
2. Complex Shapes One of the standout features of sand casting is its ability to produce intricate shapes and designs that may be difficult or even impossible to achieve with other methods. This flexibility is especially beneficial for custom parts that require unique specifications.
custom sand casting
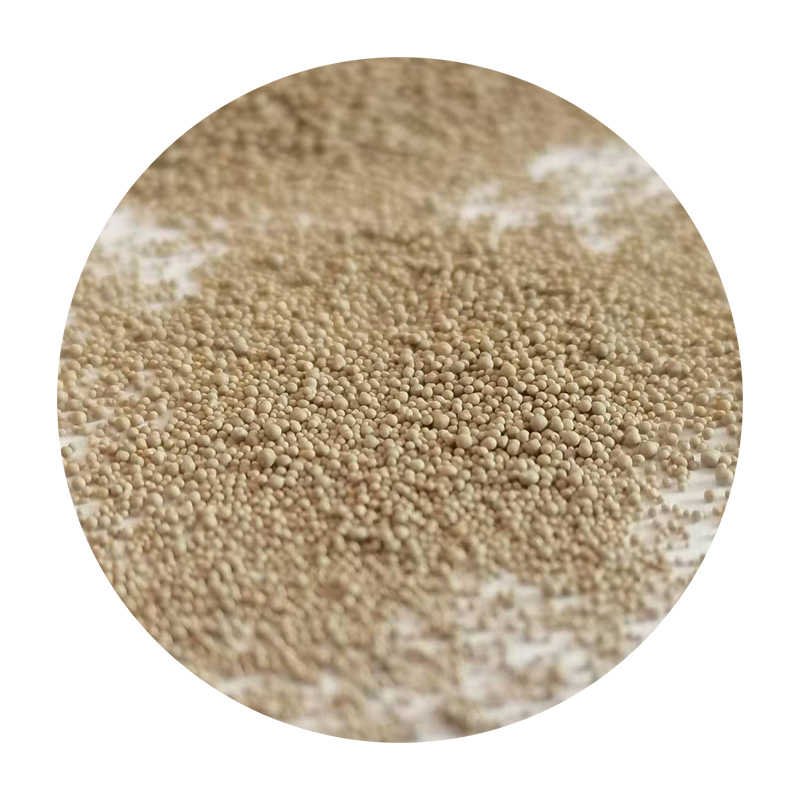
3. Material Variety Sand casting can accommodate a wide range of metals, allowing engineers and designers to choose the best material for their specific application. This capability enhances the performance and durability of the final product.
4. Scalability Whether you need a single prototype or thousands of units, sand casting can be easily scaled to meet production demands. This adaptability makes it suitable for both small workshops and large industrial operations.
Applications of Custom Sand Casting
Custom sand casting is widely used in numerous fields, including automotive, aerospace, marine, and construction industries. Common applications include
- Engine blocks and cylinder heads in automotive manufacturing. - Complex components for aerospace engines and structures. - Parts for marine vessels, such as propellers and fittings. - Heavy-duty components used in construction equipment, like gears and housings.
Conclusion
In conclusion, custom sand casting is a pivotal manufacturing process that combines cost-effectiveness, flexibility, and the ability to produce complex shapes. Its extensive applications across various industries demonstrate its significance in modern manufacturing. As technology advances, the sand casting process continues to evolve, with innovations such as 3D printing aiding in pattern creation and mold making. This evolution promises to enhance the efficiency and capabilities of custom sand casting, ensuring its relevance for years to come. Whether you are a manufacturer looking to produce custom parts or an engineer exploring design possibilities, understanding the nuances of custom sand casting will undoubtedly serve you well in your endeavors.
Post time:syys . 25, 2024 03:57
Next:Benefits of Sand Casting for Efficient Metal Manufacturing Techniques