Components of Sand Casting
Sand casting, also known as sand mold casting, is a versatile and widely used manufacturing process in which molten metal is poured into a mold made of sand to create a desired shape or component. This process has been utilized for centuries and continues to be a popular choice due to its ability to produce complex geometries, cost-effectiveness, and suitability for mass production. The success of sand casting largely depends on its components, each playing a vital role in ensuring the quality and efficiency of the casting process.
1. Molding Sand
The primary component of sand casting is molding sand, which is a mixture of silica sand, clay, water, and other additives. Silica sand forms the bulk of the mold because of its high melting point and excellent heat resistance. The clay serves as a binder, providing cohesiveness to the sand grains, which helps in retaining the mold shape. Water is added to activate the clay, enhancing the mold's strength and workability. Different types of molding sands, such as green sand, resin sand, and silica sand, are used depending on the required properties of the mold and the specific application.
2. Pattern
A pattern is a replica of the final product that is used to create the sand mold. Patterns can be made from various materials, including wood, metal, or plastic, and are usually slightly larger than the final component to account for shrinkage that occurs during cooling. Patterns are designed with specific features, such as cores, which are additional pieces inserted into the mold to create internal cavities or shapes in the final casting. The accuracy and finish of the pattern critically affect the quality of the mold and, consequently, the final casting.
3. Mold Cores
Mold cores are additional components made from sand or other materials that are inserted into the mold to create internal features of the casting. They play a crucial role in forming complex geometries, such as passages and holes, that cannot be achieved through the use of a pattern alone. Cores are typically produced separately and then placed into the mold before the molten metal is poured. The use of cores enables the production of intricate designs and improves the functionality of the final product.
components of sand casting
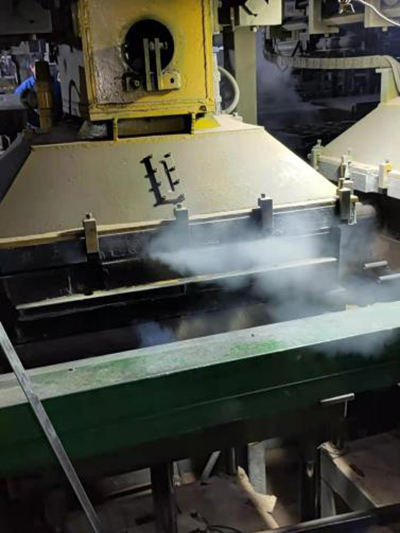
To ensure that the molten metal fills the mold completely and compensates for any shrinkage during cooling, a well-designed feeding system is essential. The feeding system consists of runner gates and risers, which are channels that direct the molten metal into the mold cavity. Risers act as reservoirs of molten metal, allowing them to feed the casting as it solidifies and prevents defects such as voids and shrinkage cavities. An effective feeding system is crucial for producing high-quality castings with minimal defects.
5. Metal Alloys
The choice of metal alloy significantly impacts the properties of the final casting. Common alloys used in sand casting include aluminum, cast iron, bronze, and magnesium, each possessing unique characteristics that make them suitable for different applications. The alloy's melting temperature, fluidity, and solidification rate are essential factors to consider, as they influence the casting process and the resulting material properties.
6. Casting Equipment
Finally, the equipment used in the sand casting process also plays a critical role. This includes furnaces for melting the metal, molds for shaping, and tools for handling the castings after they have cooled. Automated systems have been developed to enhance the efficiency and precision of the casting process, reducing labor costs and improving overall productivity.
Conclusion
In summary, the components of sand casting, including molding sand, patterns, mold cores, the feeding system, metal alloys, and casting equipment, collectively contribute to the success of the casting process. Each element must be carefully considered and optimized to ensure high-quality and efficient production. With its adaptability and effectiveness, sand casting remains a fundamental method in the manufacturing industry, enabling the creation of a wide range of components used in various applications.
Post time:loka . 18, 2024 11:58
Next:Understanding the Role of Sand in the Metal Casting Process for Optimal Results