The Role of Ceramic Foundry Sand in Modern Casting Processes
In the ever-evolving world of foundry technology, ceramic foundry sand has emerged as a crucial material for enhancing the casting process. As the demand for high-quality cast products continues to rise, industries are increasingly turning to advanced materials like ceramic foundry sand to optimize their operations. This article explores the benefits, applications, and properties of ceramic foundry sand, highlighting its significance in the casting industry.
Ceramic foundry sand, primarily composed of high-purity alumina (Al2O3), is distinguished by its superior thermal stability, low thermal expansion, and excellent flowability. These properties make it an ideal medium for producing intricate patterns with fine details, which is essential in modern manufacturing. Unlike traditional silica sand, ceramic foundry sand offers reduced risk of sand erosion and less deformation during the casting process, leading to improved dimensional accuracy of the final products.
One of the most significant advantages of ceramic foundry sand is its ability to withstand high temperatures
. Industries that require casting components exposed to extreme thermal conditions, such as aerospace and automotive, benefit immensely from using this material. Its thermal resistance ensures that molds maintain their shape and integrity, reducing the likelihood of defects in the final casting.ceramic foundry sand
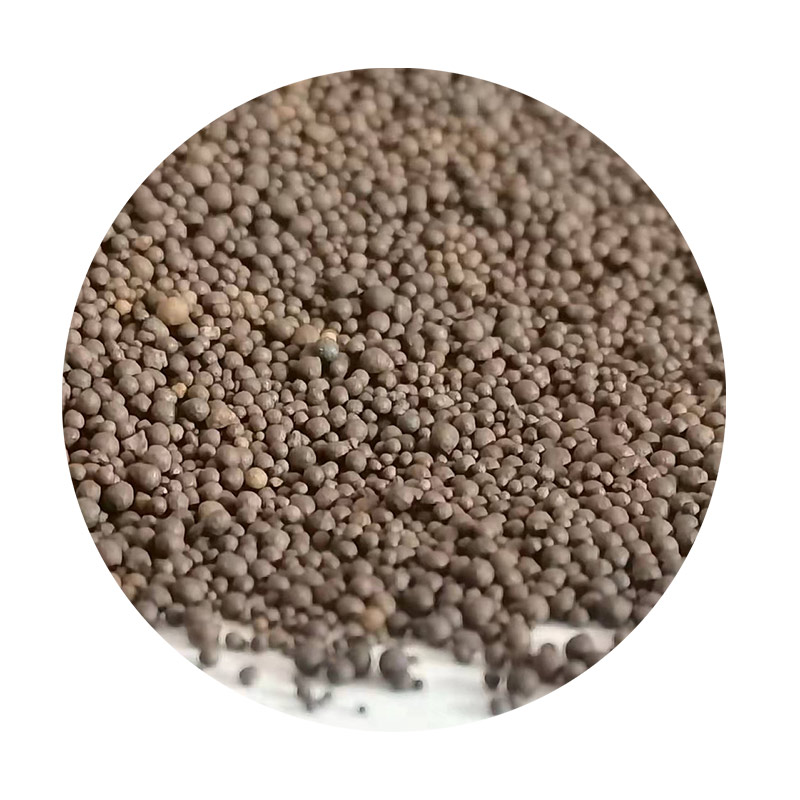
Additionally, ceramic foundry sand exhibits lower permeability compared to traditional sands. This characteristic plays a critical role in minimizing gas porosity in castings, which can compromise the strength and durability of the final product. By using ceramic foundry sand, manufacturers can achieve higher quality castings with fewer defects, resulting in lower rejection rates and increased efficiency.
Moreover, the environmental impact of foundry operations has gained significant attention in recent years. Ceramic foundry sand is often considered a more sustainable alternative. Its recyclable nature allows foundries to reuse spent sand for multiple cycles, reducing waste and the need for new materials. This not only cuts costs but also aligns foundry operations with sustainable practices, a growing demand among consumers and regulatory bodies alike.
The versatility of ceramic foundry sand extends to various casting methods, including investment casting, shell molding, and lost foam casting. Each of these processes benefits from the unique properties of ceramic sand, promoting better surface finishes and finer details in the final products. Whether it’s the production of turbine blades, engine components, or intricate artistic pieces, the application of ceramic foundry sand is transforming the landscape of metal casting.
In conclusion, the adoption of ceramic foundry sand marks a significant advancement in casting technology. Its superior properties enhance the quality and efficiency of casting processes, while also addressing environmental concerns. As industries continue to seek innovative solutions to meet increasing demands, ceramic foundry sand is poised to play an integral role in shaping the future of manufacturing. With ongoing research and development, it is likely that we will see even more applications and improvements in this essential material in the years to come.
Post time:syys . 22, 2024 12:49
Next:3d printer sand casting