The Benefits and Process of Cast Iron Sand Casting
Cast iron sand casting is a highly efficient and cost-effective manufacturing process that has been utilized for centuries to produce metal parts. This technique involves the use of a mixture of sand and a binding agent to create a mold into which molten cast iron is poured. The combination of sand and iron creates durable components with excellent mechanical properties, making them suitable for a wide variety of applications, from automotive parts to industrial machinery.
One of the primary advantages of cast iron sand casting is its versatility
. The process can accommodate complex shapes and large parts, enabling manufacturers to create intricate designs that would be challenging or costly to produce with other methods. Additionally, sand casting can be used to produce both ferrous and non-ferrous materials, expanding its applicability across various industries.The process begins with the creation of a mold. A pattern, often made of metal or plastic, is constructed to the desired shape of the final product. This pattern is then placed in a sand mixture, which is typically a combination of silica sand and a binder, such as clay or resin. Once the sand is compacted around the pattern, the mold is carefully removed, leaving a cavity that mirrors the pattern's shape. This mold can be used multiple times, which enhances its cost-effectiveness.
cast iron sand casting
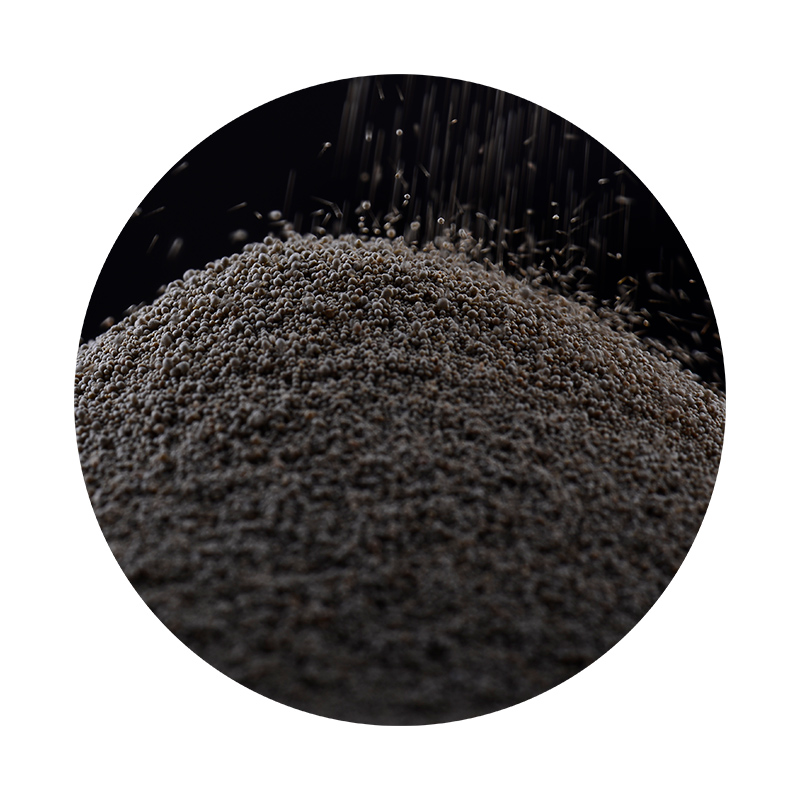
After the mold is prepared, molten cast iron is poured into the cavity. The temperature of the molten iron can exceed 1400 degrees Celsius, ensuring that it fills every detail of the mold. Once the casting has cooled and solidified, the mold is broken away to reveal the newly formed part. Subsequent processes, such as machining and surface finishing, may be employed to achieve the desired final dimensions and surface quality.
Cast iron castings exhibit excellent wear resistance and high tensile strength, making them ideal for high-stress applications. Moreover, the material's ability to absorb vibrations makes it a preferred choice for manufacturing engine blocks, pump housings, and other components where stability is crucial.
In addition to its mechanical advantages, cast iron sand casting is also more environmentally friendly compared to other casting methods. Many foundries are investing in green sand technologies, which utilize reclaimed sand and reduce waste. This shift not only minimizes the environmental impact but also lowers production costs, making the process even more attractive to manufacturers.
In conclusion, cast iron sand casting is a robust and adaptable manufacturing technique that provides numerous benefits, including cost-efficiency, versatility, and excellent mechanical properties. As industries continue to seek sustainable and economical solutions, this age-old method remains a foundational pillar in the world of metal casting. Its enduring relevance is a testament to its effectiveness in producing high-quality components that meet the demands of modern engineering.
Post time:syys . 25, 2024 01:38
Next:why sand casting is preferred