Casting Sand for Sale A Comprehensive Overview
Casting sand, also known as foundry sand, is a crucial ingredient in metal casting processes. The quality and type of sand used can significantly impact the efficiency and outcome of casting operations. As industries continue to evolve and seek high-quality materials, the demand for casting sand has notably increased. This article will explore the significance of casting sand, its types, sources, and the factors to consider when purchasing it.
What is Casting Sand?
Casting sand is a blend of silica (SiO2) grains that is used in the casting process to create molds and cores. It plays a crucial role in shaping liquid metals into desired forms. The primary function of casting sand is to hold the shape of the mold while being able to withstand the heat and pressure of the molten metal. The most common type of casting sand is green sand, composed of silica sand, clay, and water. Other types include resin bond sand, water glass sand, and oil sand, each suited for specific casting applications.
Importance of Casting Sand in Industries
Casting sand is vital in various industries, including automotive, aerospace, and manufacturing. The ability to produce intricate designs and components with high precision makes it an indispensable material in these sectors. Industries prefer casting sand because it provides excellent surface finish, dimensional accuracy, and thermal stability. Moreover, the reusable nature of foundry sand makes it a cost-effective choice, reducing waste and overall production costs.
Types of Casting Sand
casting sand for sale
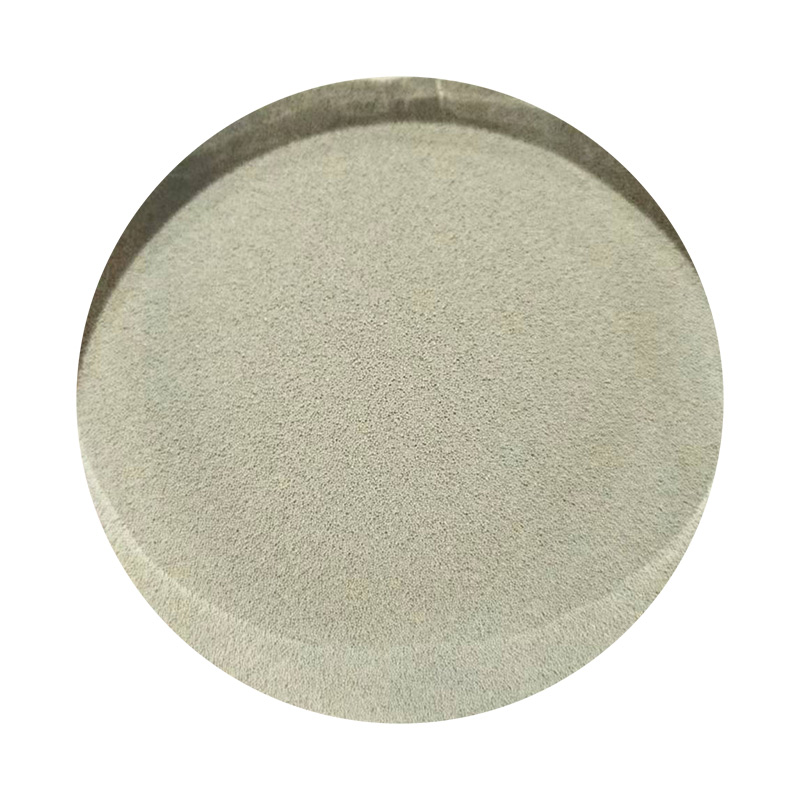
1. Green Sand This is the most commonly used sand in the casting industry. Green sand consists of silica sand mixed with bentonite clay and water. It has excellent mold strength and is particularly suitable for ferrous and non-ferrous castings. 2. Resin Bond Sand This sand is coated with resin, which, when heated, solidifies and creates a durable mold. It is ideal for high-precision castings that require a smooth finish. 3. Shell Molding Sand This type involves coating a pattern with a resin mixture and curing it with heat. Shell molding sands are used when a higher dimensional accuracy and finer surface finish are required. 4. Lost Foam Sand This is used in the lost foam casting process, where a foam pattern is coated with sand and then vaporized away in the pouring process, leaving the mold for the metal.
How to Choose the Right Casting Sand
When selecting casting sand, several factors should be taken into account
1. Grain Size The size of the sand particles affects the mold’s ability to capture fine detail. Finer sands produce smoother surfaces but can also increase the likelihood of defects. 2. Clay Content The clay content influences the mold strength and the ability to hold shape under the molten metal’s weight. 3. Cohesion and Adhesion Good casting sand should have the ability to stick to itself to form strong molds without cracking.
4. Recyclability Environmentally sustainable practices have encouraged the recycling and reusage of foundry sand, making it essential to consider the recyclability of the chosen sand.
Conclusion
As industries look to enhance their casting processes, the demand for high-quality casting sand continues to grow. Understanding the types of casting sand available, their unique properties, and how they influence the casting process is crucial for manufacturers. Whether you are in the automotive or aerospace sector, sourcing the right casting sand can make a significant difference in production efficiency, product quality, and sustainability. With numerous suppliers and varieties available, ensuring that you choose the correct type of casting sand will undoubtedly lead you to success in your casting endeavors.
Post time:tammi . 01, 2025 13:09
Next:सोने Sands विक्रीसाठी उपलब्ध