The Evolution and Impact of 3D Sand Printing in Casting Processes
In recent years, the manufacturing industry has witnessed transformative advancements, one of the most significant being the adoption of 3D printing technology. Among the various applications of 3D printing, 3D sand printing has emerged as a groundbreaking technique, particularly in casting processes, which has altered traditional methods and opened new avenues for efficiency, customization, and environmental sustainability.
Understanding 3D Sand Printing
3D sand printing utilizes additive manufacturing technology to create complex molds and cores directly from digital models. The process involves using a binder that solidifies sand particles, layer by layer, to form the desired shape. This innovative approach contrasts sharply with traditional sand casting methods, whereby molds are typically created through labor-intensive and time-consuming processes. By streamlining mold production, 3D sand printing allows for rapid prototyping and a high degree of precision, enabling manufacturers to produce components with intricate geometries that were previously difficult, if not impossible, to achieve.
Advantages of 3D Sand Printing in Casting
1. Design Flexibility The most compelling advantage of 3D sand printing is its capability to produce intricate and complex designs. Manufacturers can create geometries that optimize performance, reduce weight, and improve cooling capabilities. This flexibility empowers engineers to explore innovative designs without being constrained by traditional mold-making limitations.
2. Reduced Lead Times Traditional sand casting often involves long lead times due to mold preparation and tooling. In contrast, 3D sand printing can significantly shorten these times, allowing manufacturers to move swiftly from design to production. This rapid turnaround is particularly beneficial in industries that require quick responses to market demands.
3. Cost Efficiency While the initial investment in 3D sand printing technology may be high, the long-term cost savings can be substantial. The reduction in material waste, lower labor costs associated with mold production, and less need for extensive machining of finished parts contribute to overall cost efficiency. Furthermore, the ability to create molds on-demand means that manufacturers can reduce their inventory costs.
3d sand printing casting
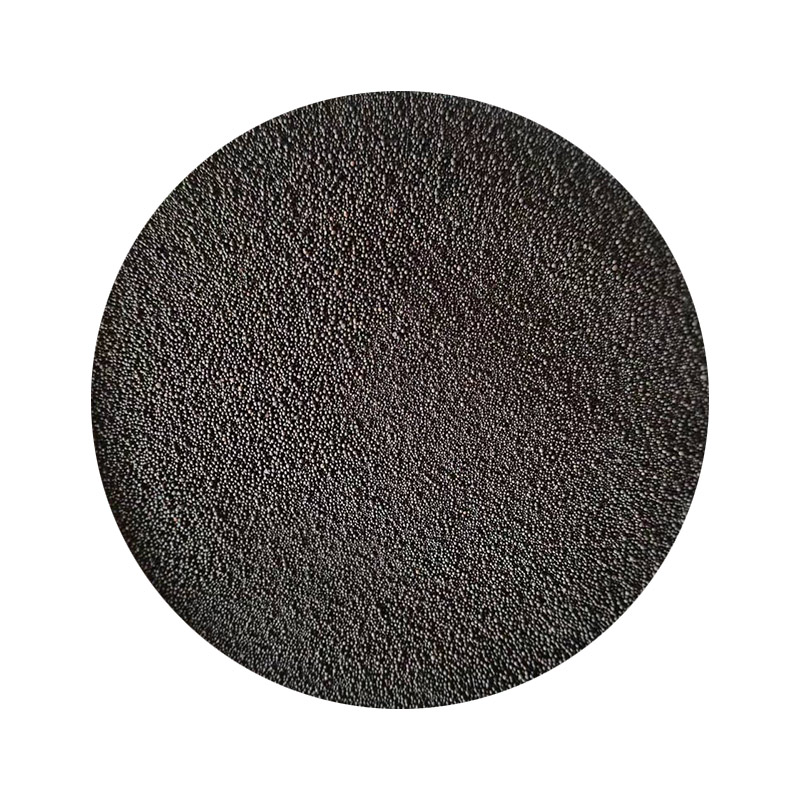
4. Environmental Sustainability The manufacturing sector is increasingly focused on sustainability, and 3D sand printing provides an eco-friendly alternative to traditional methods. This technology generates significantly less waste compared to traditional casting methods, and the use of recycled sand in the printing process further minimizes environmental impact. Additionally, because parts can be produced as needed, this reduces the carbon footprint associated with transportation and excess inventory.
5. Customization The ability to quickly adapt designs for specific applications is invaluable in industries such as aerospace, automotive, and healthcare. 3D sand printing allows for tailored solutions that meet precise customer requirements, creating a competitive edge in the market.
Challenges and Future Outlook
Despite its many advantages, 3D sand printing is not without challenges. The technology still faces hurdles such as the need for skilled personnel to operate and maintain advanced printers, acceptance within traditional industries, and the initial investment costs. Additionally, as with any emerging technology, regulatory standards and quality assurance mechanisms must evolve to ensure produced components meet both safety and performance specifications.
Looking forward, the landscape for 3D sand printing in casting is promising. As technological advancements continue to improve printing precision and speed, and as the cost of equipment decreases, we can expect wider adoption across various sectors. Collaborative efforts between researchers, industry experts, and manufacturers are likely to drive innovation, leading to the development of new materials and processes that further enhance the capabilities of 3D sand printing.
Conclusion
3D sand printing is revolutionizing the casting process, offering improved design flexibility, reduced lead times, cost efficiencies, and sustainable practices. As this technology matures, it will undoubtedly reshape the future of manufacturing, driving increased innovation and enabling industries to meet ever-evolving market demands. The transformation brought forth by 3D sand printing is a testament to the power of technology in shaping a more efficient and sustainable manufacturing landscape.
Post time:loka . 09, 2024 15:17
Next:Custom Sand Casting Solutions for Your Manufacturing Needs with Quality Assurance Services