Why Sand Casting is Used An In-Depth Exploration
Sand casting is one of the oldest and most versatile metal casting processes, widely adopted in the manufacturing industry. This method involves creating molds from sand, into which molten metal is poured to form parts. While there are various casting techniques available, sand casting remains popular for several reasons, making it a critical process in producing complex metal components.
1. Cost-Effectiveness
One of the most significant advantages of sand casting is its cost-effectiveness. The raw materials used in this process—primarily sand, clay, and metal—are abundant and inexpensive. Unlike other casting methods that may require specialized materials or complex tooling, sand casting uses readily available resources. This affordability makes it an attractive option for both small-scale projects and large production runs, allowing manufacturers to maintain lower overhead costs.
2. Flexibility and Versatility
Sand casting is remarkably versatile, capable of producing a wide range of shapes and sizes. This adaptability allows manufacturers to create intricate designs that would be difficult or impossible to achieve with other casting methods. Whether producing small items or large components, sand casting can accommodate various requirements. This flexibility makes it suitable for industries as diverse as aerospace, automotive, and art foundry.
3. Capacity for Large Parts
Another reason sand casting is favored is its capacity to produce large and heavy components. Many other casting processes, such as investment casting, have limitations on the size of the parts that can be manufactured. However, sand casting can create parts weighing several tons, making it ideal for producing large machinery components, engine blocks, and other hefty items that require durability and strength.
4. Complex Shapes and Features
The nature of sand molds allows for the production of complex geometries with intricate features. The sand mold can capture fine details from the pattern, ensuring that complex features like undercuts, hollows, or cores can be achieved with ease. This capability reduces the need for additional machining operations, saving time and costs in the production process.
why is sand casting used
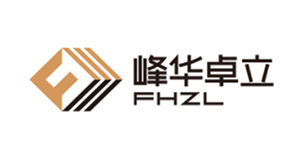
5. Rapid Prototyping
In today’s fast-paced manufacturing environment, the ability to quickly produce prototypes is crucial. Sand casting facilitates rapid prototyping, allowing designers and engineers to create and test their concepts more efficiently. The speed at which sand molds can be produced means that modifications to designs can be implemented swiftly, leading to faster product development cycles.
6. Ease of Production
The sand casting process is relatively simple compared to other manufacturing methods. The equipment required—such as sand mixers, mold boxes, and furnaces—is straightforward and does not necessitate extensive training or specialized knowledge. This simplicity means companies can quickly set up production lines and adjust to changing manufacturing needs without excessive downtime or investment in new technologies.
7. Recyclability of Materials
An added benefit of sand casting is the recyclability of the sand used in the process. The sand can be reused numerous times, which not only helps reduce material costs but also minimizes waste. After the casting process, spent sand can be reclaimed and treated, making it suitable for future mold making. This sustainability aspect aligns well with modern manufacturing’s emphasis on environmentally responsible practices.
8. Applications Across Industries
Sand casting finds its applications across a broad spectrum of industries. It is widely used in automotive and aerospace for producing engine components, transmission cases, and other parts that require durability and precision. Moreover, it is also employed in creating artistic sculptures and historical reproductions, showcasing its versatility.
Conclusion
In conclusion, the use of sand casting remains prevalent due to its numerous advantages. Its cost-effectiveness, versatility, capacity for large parts, ability to produce complex shapes, rapid prototyping capabilities, production ease, recyclability of materials, and applications across various industries make it a go-to method for manufacturers. As technology continues to evolve, sand casting is likely to adapt and remain a vital process in the world of manufacturing, catering to the ever-changing needs of different sectors.
Post time:نوامبر . 15, 2024 17:14
Next:steel sand casting suppliers