The Art of Wet Sanding Ceramics A Comprehensive Guide
Wet sanding ceramics is an essential technique in the ceramic crafting process that elevates the quality of the final product. This method not only smooths the surface but also enhances the aesthetics of ceramic pieces, offering a more refined finish. Whether you are a seasoned potter or a beginner, understanding the wet sanding process can significantly improve your craftsmanship.
Understanding Wet Sanding
Wet sanding involves using water as a lubricant when sanding surfaces. This technique minimizes dust and reduces the risk of damaging the ceramic piece while opting for a smoother finish. The water helps carry away ceramic dust, which can otherwise clog sandpaper, ensuring that the abrasive material maintains its effectiveness throughout the process.
When to Wet Sand Ceramics
Typically, wet sanding is performed during the finishing stages of a ceramic piece. After bisque firing, when the pottery is still porous but has hardened enough to sand, this is the optimal time to apply wet sanding. It’s crucial to note that wet sanding is most effective on greenware or bisque-fired ceramics. Attempting to wet sand glazed or fully fired pottery can lead to scratches or damage to the surface, which often requires additional restoration.
Materials Needed
To effectively wet sand ceramics, you will need a few essential tools and materials
- Sandpaper Choose wet/dry sandpaper with varying grits. Start with a lower grit (around 220) for shaping and progress to a higher grit (up to 2000) for polishing. - Water source A spray bottle or a shallow dish to keep the surface wet throughout the sanding process. - Sponge To clean the surface and keep it wet. - A sturdy work surface Ensure you have a well-lit and stable area to work on.
The Wet Sanding Process
wet sanding ceramics
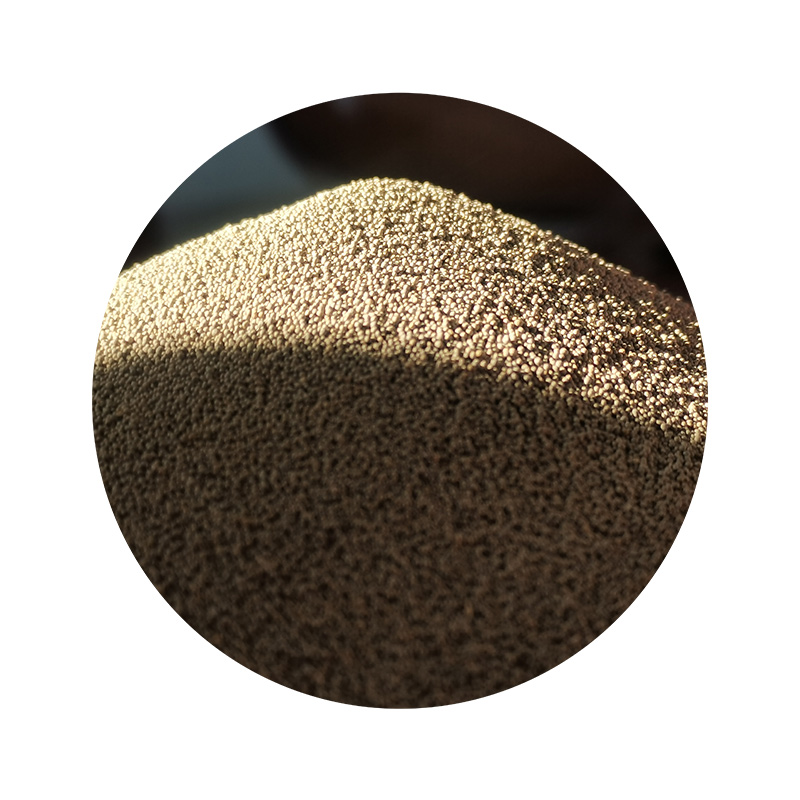
1. Preparation Begin by ensuring your ceramic piece is clean and free of debris. Set up a work area where you can comfortably sand while keeping water contained.
2. Initial Sanding Start with the lower grit sandpaper to remove major imperfections. Dip the sandpaper in water and begin sanding the surface in a circular motion. The water will help keep the dust down and prevent the sandpaper from clogging.
3. Smoothing the Surface As you progress, switch to finer grit sandpaper. Continue to apply water regularly to maintain lubrication. Take your time and be mindful of even pressure; this consistency will lead to a smoother finish.
4. Final Polishing Once you achieve the desired smoothness, switch to the finest grit sandpaper. This stage is crucial for adding a polished sheen to your ceramic piece. Delicately sand the surface using light pressure, lingering longer on areas requiring extra attention.
5. Cleaning Up After sanding, wash the ceramic piece thoroughly to remove any residual particles. You can use a soft sponge and warm soapy water for this step. Ensure it dries completely before proceeding to glaze or final firing.
Tips and Considerations
- Patience is Key Wet sanding takes time. Rushing through can lead to uneven surfaces or scratches. - Practice on Test Pieces If you’re new to this technique, practice on scrap pieces before working on your main project. - Protect Your Hands Although ceramics can be fun to work with, the edges may be sharp. Consider wearing gloves for protection.
Conclusion
Wet sanding is a foundational technique that can dramatically enhance the quality of ceramic work. With practice and patience, artists can achieve a level of smoothness and finish that elevates their creations. By embracing wet sanding, potters not only improve the functionality of their pieces but also their visual appeal, giving each work a touch of professionalism and artistry.
Post time:اکتبر . 10, 2024 18:48
Next:Exploring the Process and Benefits of Sand Casting in Metal Foundries