Types of Sand Casting Process
Sand casting is one of the oldest and most versatile forms of foundry processes used to create metal parts and products. Despite the advancements in modern manufacturing techniques, sand casting remains widely used due to its simplicity, cost-effectiveness, and ability to produce complex shapes. The sand casting process primarily involves creating a mold from sand and then pouring molten metal into the mold cavity, allowing it to cool and solidify into the final product. There are various types of sand casting processes, each suited to specific requirements and applications.
Types of Sand Casting Process
2. Dry Sand Casting Dry sand casting differs from green sand casting in that the mold is dried before the molten metal is poured in. This is achieved by heating the sand mixture, which removes moisture and hardens the mold. The dry sand mold provides better dimensional accuracy and surface finish compared to green sand molds. This process is often used for castings that require higher precision and durability, such as engine blocks and turbine components.
types of sand casting process
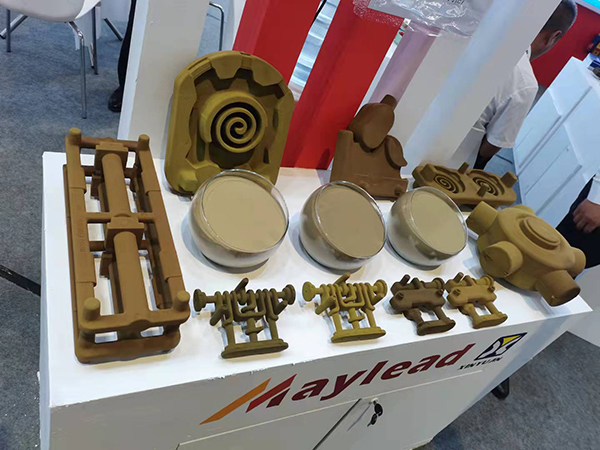
3. Sodium Silicate Sand Casting In sodium silicate sand casting, a mixture of silica sand and sodium silicate binder is used to create molds. The binder is activated by carbon dioxide gas, resulting in a strong and rigid mold. This process produces high-quality castings with excellent surface finishes, making it ideal for intricate designs and high-fidelity reproductions. Sodium silicate sand casting is commonly employed in the production of artistic sculptures and precision engineering parts.
4. Shell Molding Shell molding is a high-precision sand casting method that uses a resin-bonded sand to create thin-shell molds. A pattern is heated, and sand mixed with a thermosetting resin is applied to the pattern, forming a shell. The shell is then cured and assembled to form a mold. This process allows for the production of castings with excellent dimensional accuracy, surface finish, and strength. Shell molding is frequently used in the manufacturing of complex shapes and high-volume production runs.
5. Lost Foam Casting Lost foam casting, also known as evaporative pattern casting, involves creating a foam pattern of the desired casting shape. The foam pattern is coated with a sand mixture and then heated, causing the foam to vaporize and leave a cavity in the sand. Molten metal is poured into this cavity, replicating the foam pattern perfectly. This method is advantageous because it eliminates the need for traditional mold-making processes, allowing for fast and economical production of intricate designs.
In conclusion, the sand casting process encompasses various methods, each tailored to meet specific production needs and quality standards. From green sand casting to lost foam casting, the versatility and adaptability of sand casting techniques make them an integral part of modern manufacturing. As industries continue to evolve, sand casting will likely remain a key process for producing metal components across a wide range of applications.
Post time:اکتبر . 12, 2024 14:34
Next:Techniques for Achieving Smooth Finishes on 3D Printed Objects Through Wet Sanding