Understanding the Steel Sand Casting Process
Steel sand casting is a widely used manufacturing process that allows the production of complex and precise components. It combines the robust properties of steel with the versatility offered by sand molds, creating parts that meet stringent specifications in various industries like automotive, aerospace, and heavy machinery.
The Basics of Sand Casting
Sand casting begins with the creation of a pattern, which is a replica of the desired part. This pattern is typically made from more durable materials like metal or plastic to withstand the repeated stresses of the molding process. The pattern is then placed in sand, which is a key component of the mold. The sand used in this process is usually mixed with a binding agent that helps it hold its shape, along with water to enhance moisture content.
Once the pattern is in place, the sand mixture is compressed around it to form the two halves of the mold. After the mold is prepared, the pattern is removed, leaving a cavity that will be filled with molten steel. One of the advantages of sand casting is its capability to create intricate shapes and details, making it an ideal choice for complex designs.
Melting and Pouring Steel
The steel used for casting is typically heated in a furnace until it reaches its molten state. The furnaces can vary depending on the volume of production and specific requirements of the steel alloy being used. Induction furnaces and electric arc furnaces are common choices in industrial settings.
Once molten, the steel is carefully poured into the cavity of the sand mold. This step demands precision, as the temperature and viscosity of the molten steel can significantly affect the quality of the final product. Proper pouring techniques are critical to avoid defects such as air pockets or inconsistent thickness.
steel sand casting process
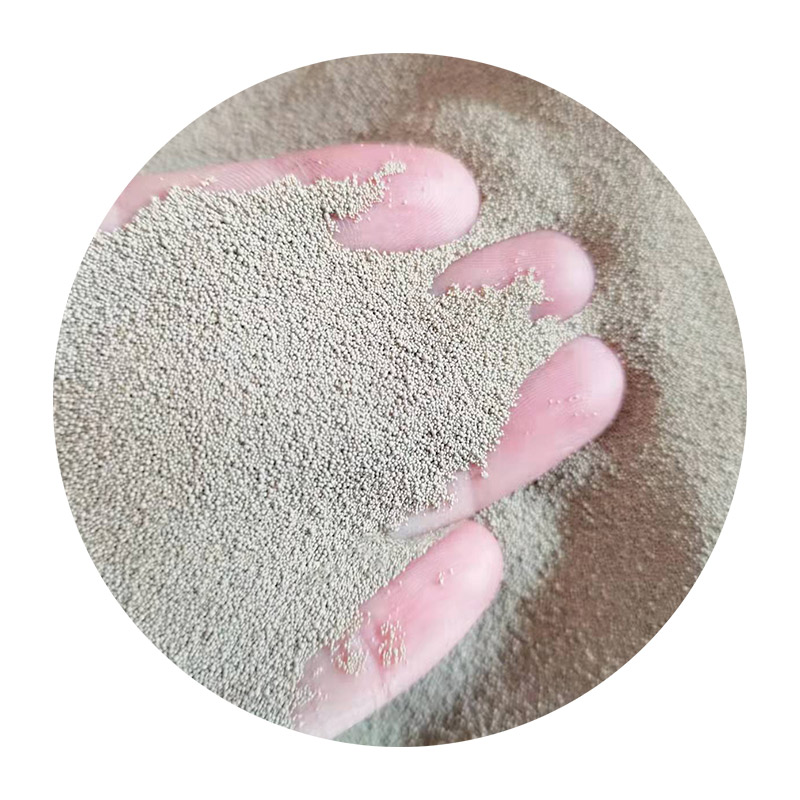
Solidification and Cooling
After pouring, the molten steel begins to cool and solidify within the mold. This phase can vary in duration depending on the dimensions and thickness of the cast piece. Once the steel has fully solidified, the mold is broken apart, and the casting is removed. The sand can often be reused after being cleaned and reconditioned, contributing to the environmental sustainability of the process.
Finishing Operations
Upon removal from the mold, the cast steel component often requires finishing operations to achieve the desired specifications. This can include processes like machining, grinding, and surface treatment. Machining is particularly significant, as it allows for the precise shaping and smoothing of surfaces that may have rough edges or imperfections after casting.
Applications of Steel Sand Casting
Steel sand casting is employed across numerous industries due to its ability to produce a wide range of component sizes and complexities. In the automotive industry, for instance, it is used to manufacture engine blocks, crankshafts, and suspension components. In the aerospace sector, durable and lightweight parts are created, contributing to the efficiency of aircraft. Additionally, heavy machinery components that facilitate construction and mining activities are often produced using this method.
Conclusion
In summary, the steel sand casting process is an essential manufacturing technique that balances efficiency, versatility, and cost-effectiveness. By understanding its fundamental steps—from pattern creation to the finishing of parts—engineers and manufacturers can leverage this process to produce high-quality steel components that meet the rigorous demands of modern applications. Whether in automotive, aerospace, or other fields, the importance of steel sand casting continues to be evident in the creation of reliable and intricate parts.
Post time:دسامبر . 07, 2024 12:11
Next:importance of sand casting