The Art and Science of Sand Castings
Sand casting, one of the oldest and most widely used metal casting processes, has played a pivotal role in manufacturing a plethora of metal parts and products for centuries. This versatile and cost-effective technique is particularly popular due to its adaptability and relatively low production costs. In this article, we will explore the essentials of sand casting, its applications, advantages, and some of the challenges it faces in modern manufacturing.
At its core, sand casting involves the creation of a mold from a mixture of sand and a bonding agent, most commonly clay. The process begins with the preparation of the sand mold. The appropriate type of sand, often silica-based, is mixed with a binding agent to create a mold that can withstand the molten metal’s temperature. The mold consists of two halves – the cope (top half) and the drag (bottom half) – and requires precise design to ensure proper alignment and consistency.
The next step involves creating the necessary patterns. These patterns are replicas of the final product and are typically made of wood, metal, or plastic. Recognizing that the final casting will shrink as it cools, manufacturers often create patterns slightly larger than the intended end product.
Once the mold and pattern are prepared, the molten metal is poured into the mold cavity. As the metal cools and solidifies, it takes the shape of the mold. After a cooling period, the sand mold is broken apart to extract the casting. This simplicity in process makes sand casting highly appealing for producing complex shapes and large components that would otherwise be challenging to achieve with other manufacturing methods.
Applications of Sand Castings
Sand castings are utilized in various industries. The automotive sector is a significant benefactor, producing components such as engine blocks, cylinder heads, and transmission cases. Additionally, the aerospace industry often relies on sand casting for parts subject to high stress and heat. Beyond these sectors, sand casting finds applications in manufacturing agricultural equipment, construction machinery, and even art pieces, showcasing its broad reach across different fields.
sand castings
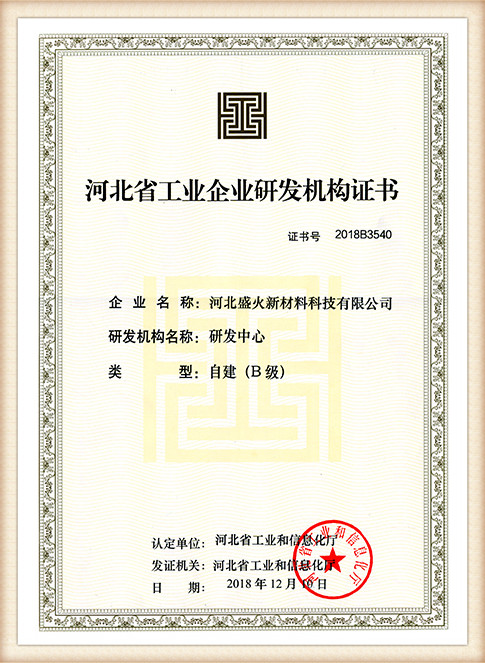
Advantages of Sand Casting
One of the most significant advantages of sand casting is its cost-effectiveness. The materials used are relatively inexpensive, and the process itself requires less initial investment compared to permanent mold or die-casting methods. Moreover, sand casting can accommodate a vast array of metal alloys, making it suitable for various applications.
Another notable feature is the flexibility of the process. Sand molds can be easily adjusted to create different sizes and shapes, allowing manufacturers to produce low to high volumes of products with relative ease. Additionally, sand casting is particularly advantageous for creating complex geometries and internal cavities, which are often challenging to achieve with other techniques.
Challenges and Future Prospects
Despite its numerous advantages, sand casting is not without challenges. The quality of the final product can be impacted by the type of sand used, the skill of the operators, and environmental factors. Defects such as blowholes, sand inclusions, and dimensional inaccuracies can occur, leading to the need for costly rework or rejection of the parts.
As industry demands evolve, the sand casting process must adapt to new technological advancements. Automation and the integration of computer-aided design (CAD) and manufacturing (CAM) are becoming increasingly prevalent, allowing for improved accuracy and efficiency. Additionally, new binding agents and sand types are being developed to enhance the sustainability and quality of the casting process.
In conclusion, sand casting remains a vital and relevant manufacturing process within various industries. Its combination of versatility, cost-effectiveness, and ability to produce complex shapes ensures its continued significance in the metalworking landscape. As advancements in technology and materials emerge, the future of sand casting appears promising, reinforcing its position as a fundamental process in modern manufacturing.
Post time:دسامبر . 04, 2024 18:17
Next:sand casting technology