Understanding Sand Casting Processes
Sand casting, also known as sand mold casting, is one of the most widely used metal casting processes. This technique involves the creation of a mold from a mixture of sand and a bonding agent, typically clay, which is then used to shape molten metal into desired forms. Sand casting is praised for its versatility, low cost, and ability to produce complex shapes. In this article, we will explore the sand casting process, its advantages, limitations, and applications.
The Sand Casting Process
The sand casting process can be broken down into several key steps
1. Pattern Creation The first step involves designing and creating a pattern, which is a model of the final product. Patterns are typically made from materials such as wood, metal, or plastic. Careful consideration is given to allow for shrinkage and draft angles, which facilitate the removal of the casting from the mold.
2. Mold Preparation The next step is preparing the mold. The pattern is pressed into a mixture of sand and a binding agent to form two halves of the mold (cope and drag). The sand mixture is compacted around the pattern to ensure it holds the shape. After the pattern is removed, the two halves of the mold are joined together.
3. Pouring Metal The mold is then heated and the molten metal is poured into it through a gate. The molten metal fills the cavity created by the pattern, taking its shape as it cools and solidifies.
4. Cooling and Solidification Once the metal has cooled sufficiently, it solidifies into the desired shape. The cooling time depends on the thickness and volume of the casting.
5. Mold Removal After adequate cooling, the sand mold is broken apart to retrieve the casting. Any residual sand is cleaned off, often using air blasts or shaking.
6. Finishing Finally, the casting may undergo various post-processing steps, such as machining, grinding, or surface treatment, to meet specific tolerances and surface finish requirements.
Advantages of Sand Casting
Sand casting has several benefits that make it a preferred choice for many manufacturing applications
sand casting processes
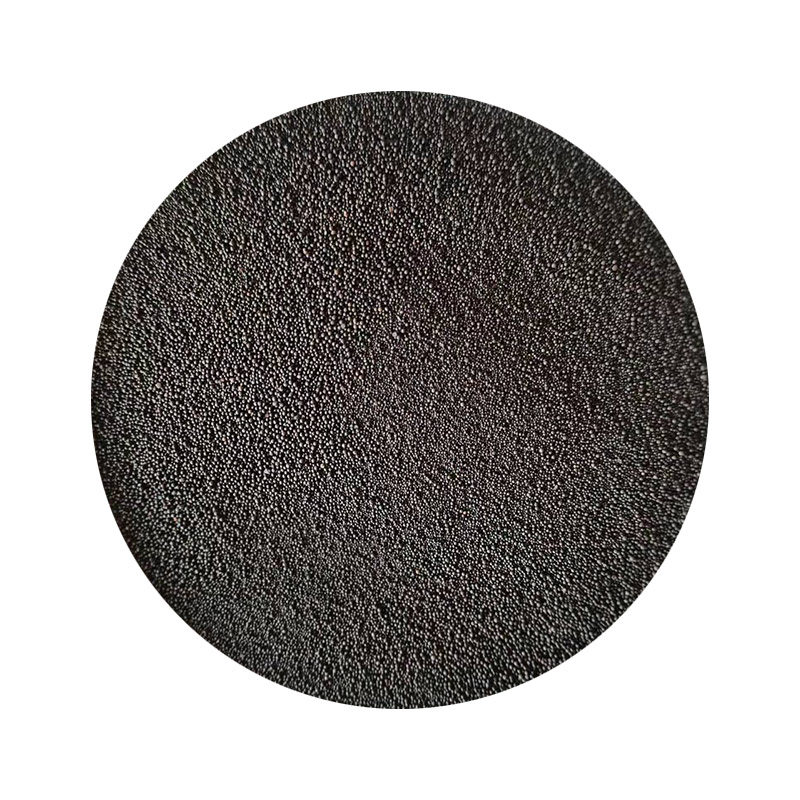
- Cost-Effectiveness The materials used in sand casting are relatively inexpensive, and the process does not require complex equipment or tooling changes, making it cost-effective for both large and small production runs.
- Flexibility Sand casting can accommodate a wide range of metal alloys, including aluminum, iron, steel, and magnesium. This flexibility makes it suitable for various industries, including automotive, aerospace, and art metalwork.
- Complex Geometries The method can produce intricate shapes and large castings, which can be challenging or impossible to achieve with other casting processes
.- Recyclability Sand used in the casting process can be recycled and reused in future molds, contributing to a more sustainable manufacturing environment.
Limitations of Sand Casting
Despite its advantages, sand casting also has some limitations
- Surface Finish Castings produced via sand casting often require additional finishing processes to improve surface quality since the sand can leave a rough texture on the final product.
- Dimensional Accuracy The tolerances achievable with sand casting are generally not as tight as those obtained from more sophisticated techniques such as die casting or precision casting.
- Labor-Intensive The manual nature of the sand casting process can increase labor costs, particularly for small production runs.
Applications of Sand Casting
Today, sand casting is widely used across various industries. It is ideal for producing engine blocks, cylinder heads, and frames for automobiles, as well as components for construction equipment, pumps, and valves. Additionally, it has found a place in artistic applications due to its ability to create detailed designs.
In conclusion, sand casting remains a vital manufacturing process due to its versatility and cost-effectiveness. Understanding the nuances of this method is essential for engineers and designers looking to leverage its benefits in their production needs.
Post time:نوامبر . 09, 2024 03:05
Next:Exploring the Innovations in Sand Printing for Precision Casting Techniques