The Art of Sand Casting A Timeless Technique
Sand casting, one of the oldest and most versatile metal casting processes, has been a foundational technique in manufacturing for centuries. This method not only embodies the artistry and craftsmanship of metalworking but also showcases innovation in engineering and production. The importance of sand casting transcends mere functionality; it represents a blend of tradition, skill, and creativity that can be traced back to ancient civilizations.
The Basics of Sand Casting
At its core, sand casting involves creating a mold from sand to form a desired shape. Initially, a pattern, typically made from materials like wood or metal, is embedded in a mixture of sand and a bonding agent. Once the pattern is secured, the mold is formed around it. After removing the pattern, the cavity is filled with molten metal. Once the metal cools and solidifies, the mold is broken away to reveal the final product. This process can be used to cast a wide range of materials, including iron, aluminum, and bronze.
The main ingredients of the sand used in this process are silica sand, which provides the necessary structure, and a variety of binders that ensure the sand holds its shape. The sand casting process is remarkably adaptable; it can be used to create small items like jewelry or large components for machinery and automobiles. Its flexibility makes it a preferred choice for many industries.
Historical Significance
Sand casting can be traced back as far as 6,000 years ago. Archaeological findings show that ancient Egyptians used sand casting to create intricate jewelry and tools. Similarly, the Chinese were known to cast bronze using sand molds. The technique flourished during the Industrial Revolution, when the demand for metal parts surged, leading to advancements in casting practices and technologies.
Throughout history, sand casting has not only served practical purposes but has also been a medium for artistic expression. Many artisans have utilized sand casting to forge unique sculptures, decorative items, and personalized gifts. The ability to create complex shapes and intricate designs has made sand casting an essential technique for both functional and aesthetic applications.
sand caste
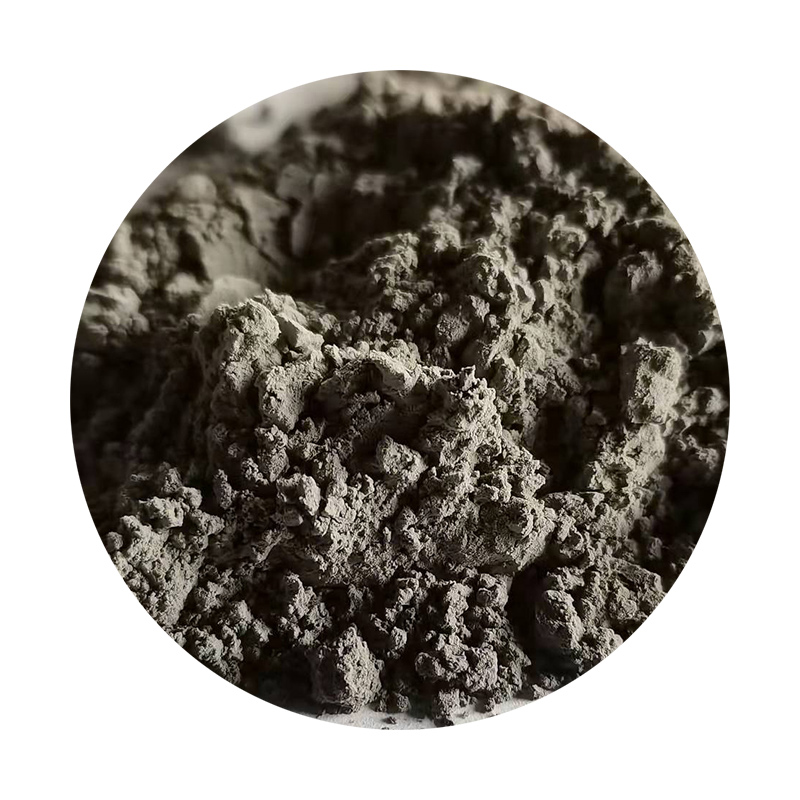
Advantages of Sand Casting
One of the significant benefits of sand casting is its cost-effectiveness. Unlike other casting methods, creating molds from sand is relatively inexpensive, especially when producing large quantities. The process also allows for the casting of large parts without the need for costly tooling. Additionally, the materials used in sand casting are readily available, further enhancing its appeal as a manufacturing choice.
Another advantage of sand casting is its versatility in casting various alloys and metals. This flexibility enables manufacturers to produce a wide range of parts that cater to different needs and specifications. Furthermore, sand casting can accommodate complex geometries, making it possible to create detailed components that might be challenging to achieve with other casting techniques.
Challenges and Innovations
Despite its advantages, sand casting is not without challenges. The process can be labor-intensive, and achieving a high level of precision can be difficult. Issues such as sand contamination, mold stability, and dimensional accuracy must be carefully managed to ensure high-quality outcomes.
However, advancements in technology have ushered in innovations that enhance the sand casting process. Techniques such as computer-aided design (CAD) and 3D printing have revolutionized mold-making, allowing for more precise and efficient production. Automation and robotics are also being integrated into the casting process, improving consistency and reducing labor costs.
Conclusion
Sand casting remains a vital technique in the manufacturing landscape. Its rich history, coupled with its adaptability and innovations, ensures its relevance in today's industrial world. As the demand for custom, intricate parts rises, sand casting not only preserves traditional craftsmanship but also embraces modern technology. This unique blend of heritage and innovation continues to shape the future of metalworking, making sand casting a timeless art form that will endure for generations to come.
Post time:نوامبر . 06, 2024 17:09
Next:Understanding the Role of Facing Sand in Modern Foundry Processes