Sand Preparation in Foundry A Crucial Step for Quality Casting
The foundry industry plays a vital role in manufacturing components for various sectors, including automotive, aerospace, and machinery. A fundamental aspect of the foundry process is sand preparation, which is critical for ensuring the accuracy and quality of cast products. This article delves into the significance of sand preparation, the processes involved, and its impact on the final product.
Importance of Sand Preparation
In foundries, sand serves as a mold-making material that must possess specific properties to create high-quality castings. Proper sand preparation is essential for achieving consistent mold quality, improving production efficiency, and reducing defects in the final products. The quality of casting is heavily influenced by the characteristics of the sand used, including its grain size, shape, and chemical composition.
Sand must be able to withstand high temperatures and provide adequate strength for the mold, preventing it from collapsing during the pouring of molten metal. Additionally, it needs to allow for proper permeability, ensuring that gases can escape during the casting process. Thus, thorough preparation of sand is a prerequisite for successful molding operations in foundries.
Sand Preparation Process
The sand preparation process typically involves several stages
1. Sand Selection The first step is selecting the right type of sand. Common types include silica sand, olivine sand, and chromite sand, each offering unique properties suitable for specific applications.
sand preparation in foundry
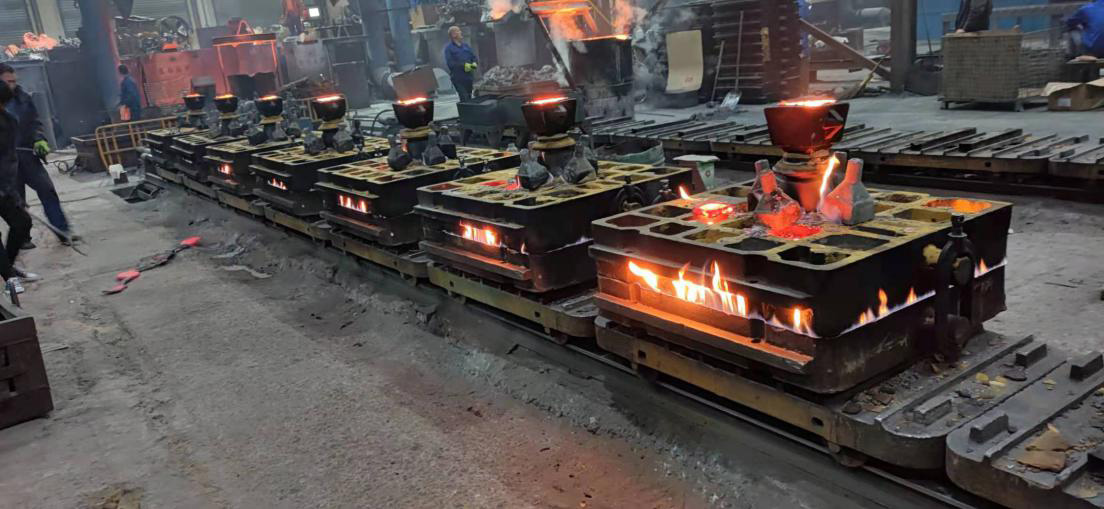
2. Sand Blending Different types of sand may be blended to achieve desired characteristics. This mixing process ensures uniformity and optimized performance for the mold.
3. Additives and Binders To enhance the sand’s properties, various additives and binders are often mixed in. These can include clay, resin, or other materials that improve the adhesive properties of the sand, ensuring that the mold holds its shape during pouring.
4. Sand Molding Once properly mixed, the sand is compacted into molds, often using a method known as rammed or jolt molding. The density and compaction level of the sand influence the final casting quality.
5. Reclamation of Used Sand After casting is complete, the used sand must be reclaimed for reuse, which involves processes such as cooling, cleaning, and sieving to remove any impurities or metal residues. This not only reduces costs but is also an environmentally friendly practice.
Impact on Final Product
The meticulous process of sand preparation directly impacts the quality of the final casting. Properly prepared sand molds result in smoother surfaces, accurate dimensions, and minimal defects such as sand inclusions or misalignment. Conversely, poorly prepared sand can lead to increased production costs due to rework and scrap.
In summary, sand preparation is a crucial step in the foundry process that significantly influences casting quality. By carefully selecting, blending, and preparing sand, foundries can ensure that their molds produce superior components that meet stringent industry standards. As the demand for high-quality castings continues to grow, investing in efficient sand preparation techniques will be pivotal for foundries aiming to enhance their production capabilities and maintain competitiveness in the market.
Post time:سپتامبر . 02, 2024 09:51
Next:make sand casting